The Property Manager’s Guide to
Battery Garage Repair and Refurbishment
How to turn old battery/system garages into new, or just repair damage caused by accidents or storms
This booklet and website lists and illustrates nearly 30 different Battery Garage Systems including coverage of the major structural problems and how to deal with them. Also the improvement of existing stock to give old garages a new lease of life without the need to demolish and rebuild from scratch. This is portrayed in some depth.
Before and after detail is shown for many of the types indexed in this book and on this website together with critical aspects such as water inflow and spalling concrete. An index of types starts at page 22.
Copies of the 40 page fully illustrated A4 booklet are available free-of-charge, and they are better than a smart phone web view as real close-ups are invaluable when looking for examples of damage or decay.
We hope that this information will prove useful in your work.
Colin Hammond, the author of this publication can be reached on 07817 692 284 for further information if needed.
Page 1
Some Completed Projects – Single / Twin Units

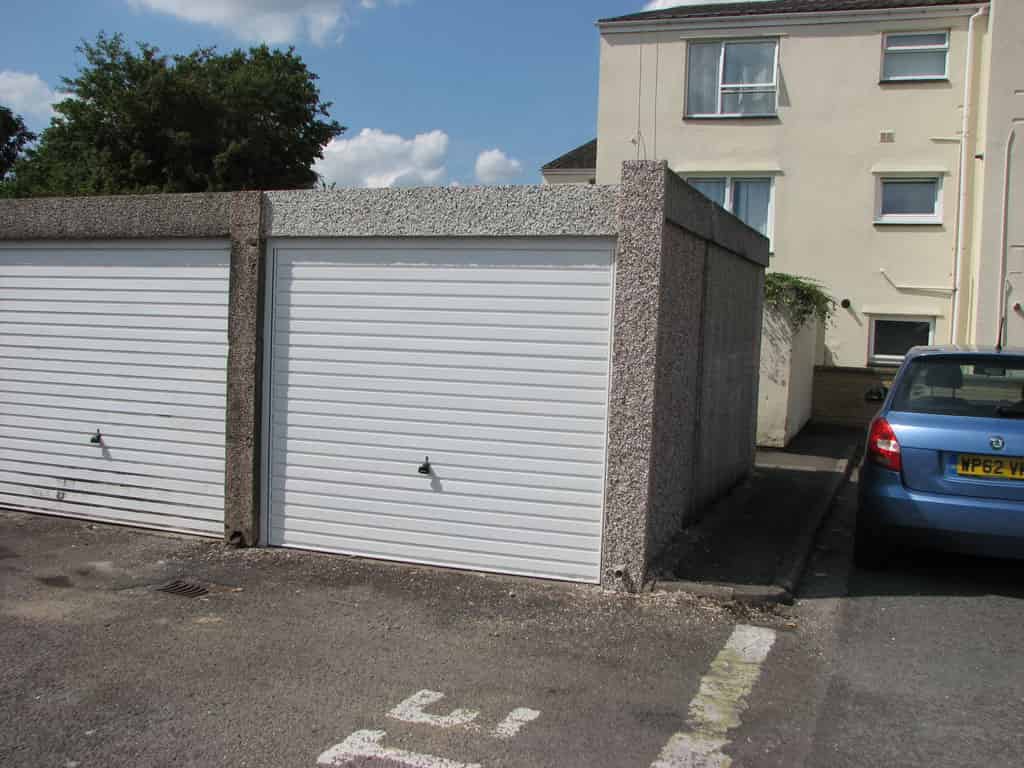
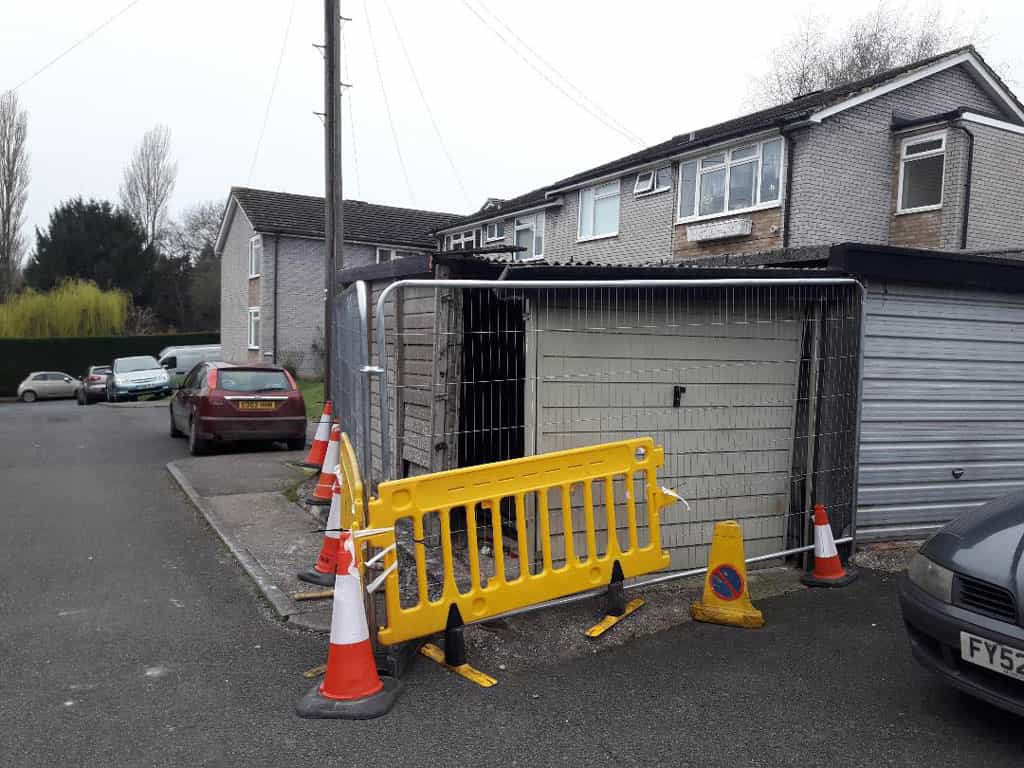
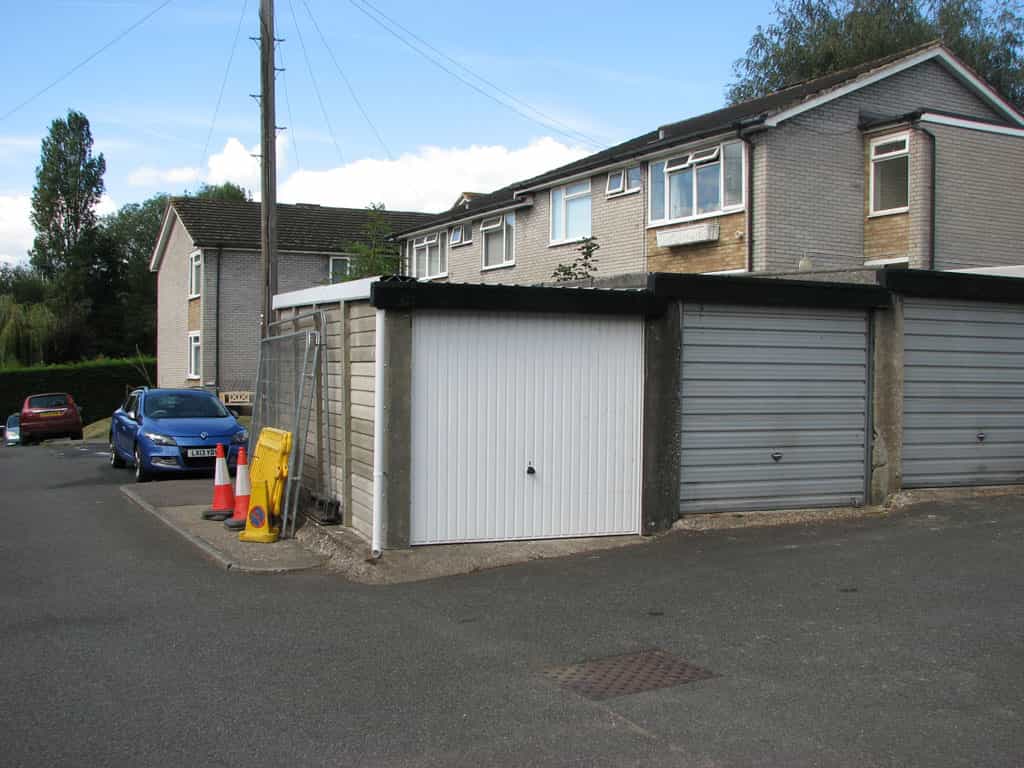
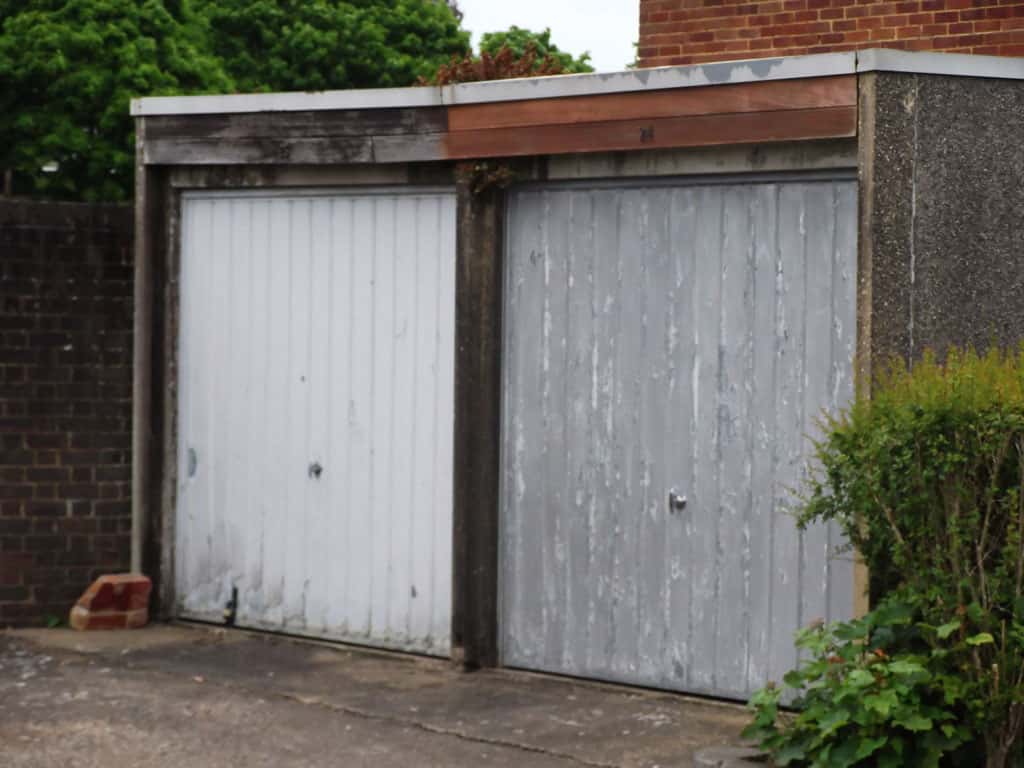
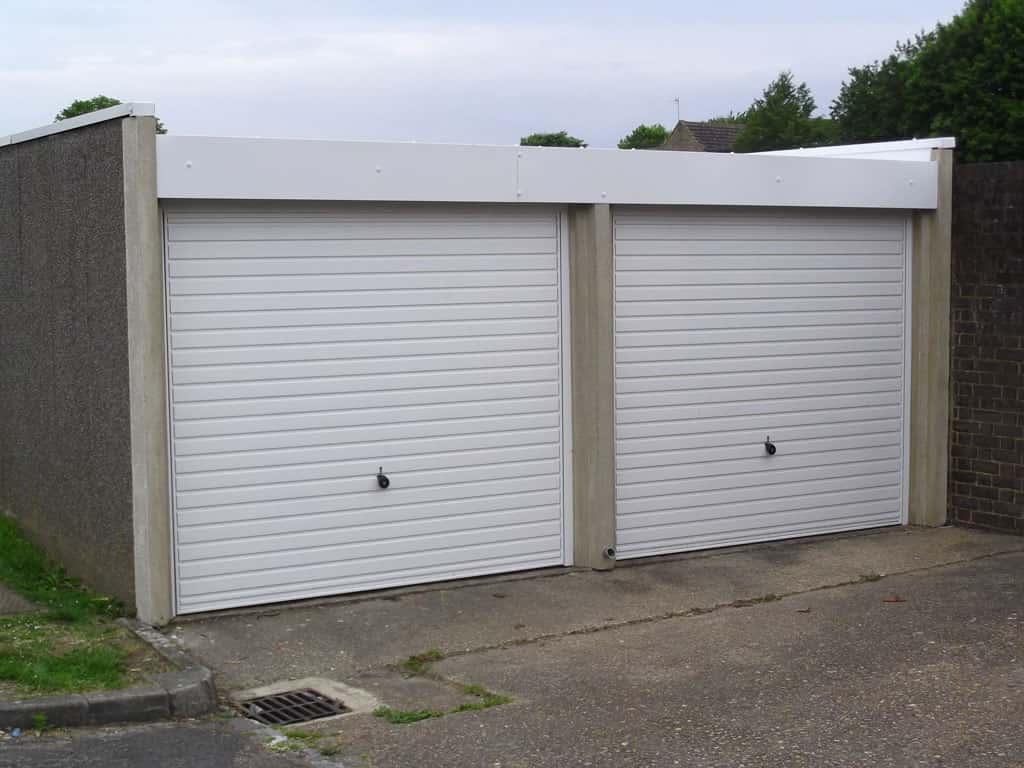


Page 2
Some Completed Projects – Multiple Units
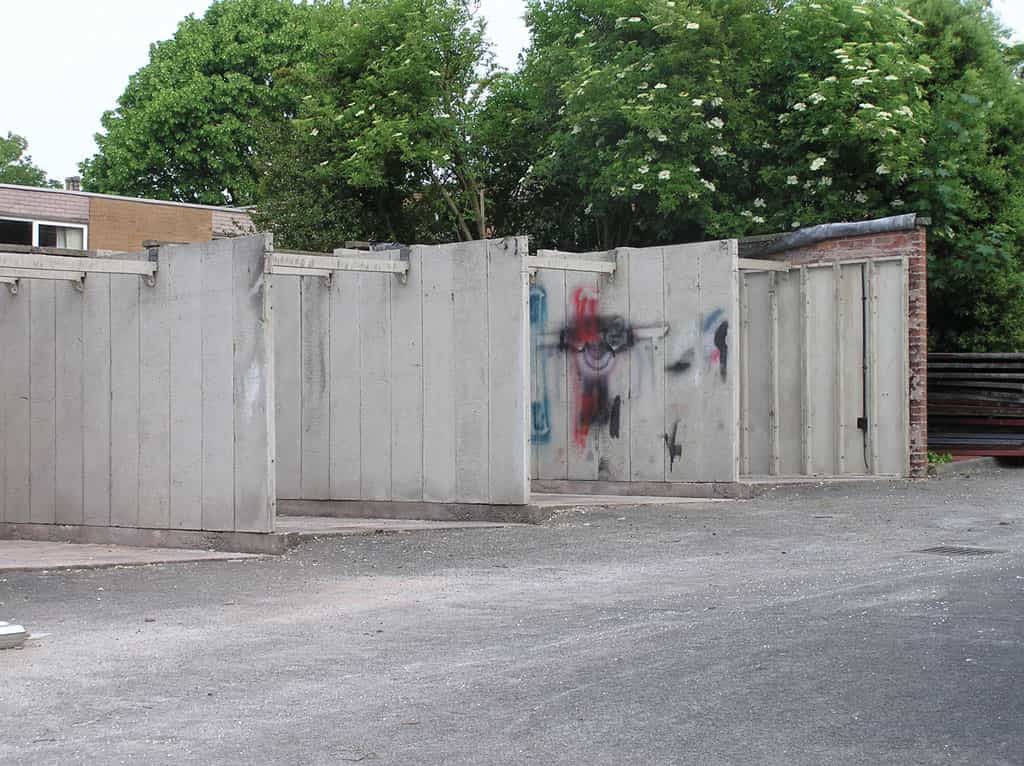
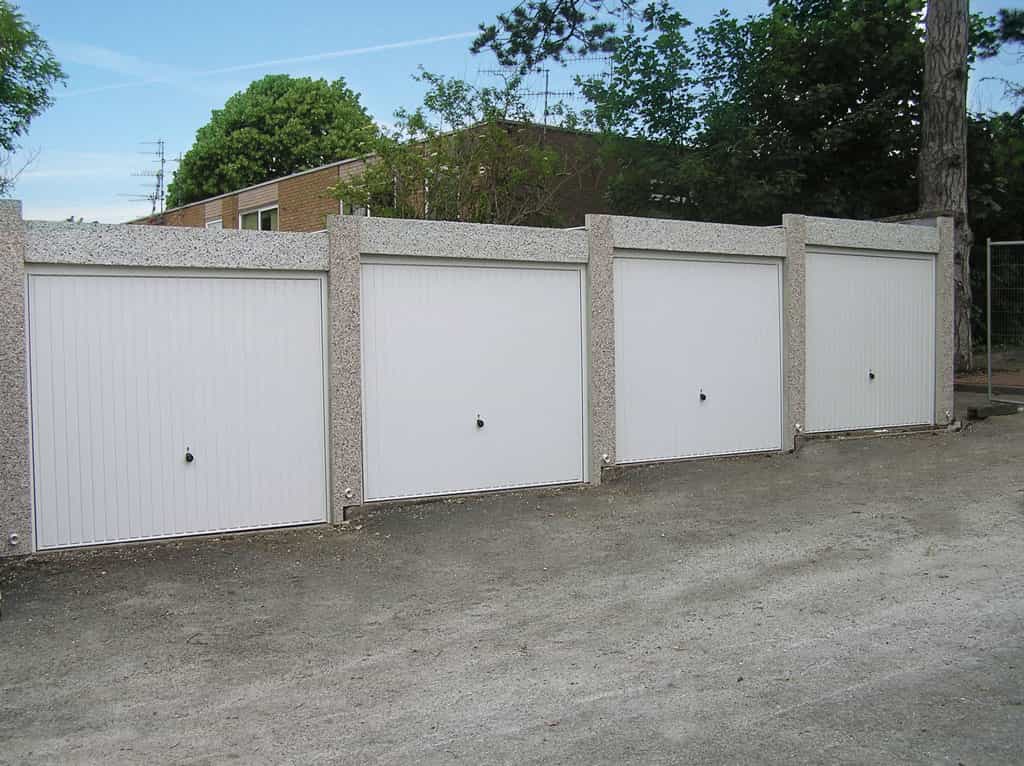
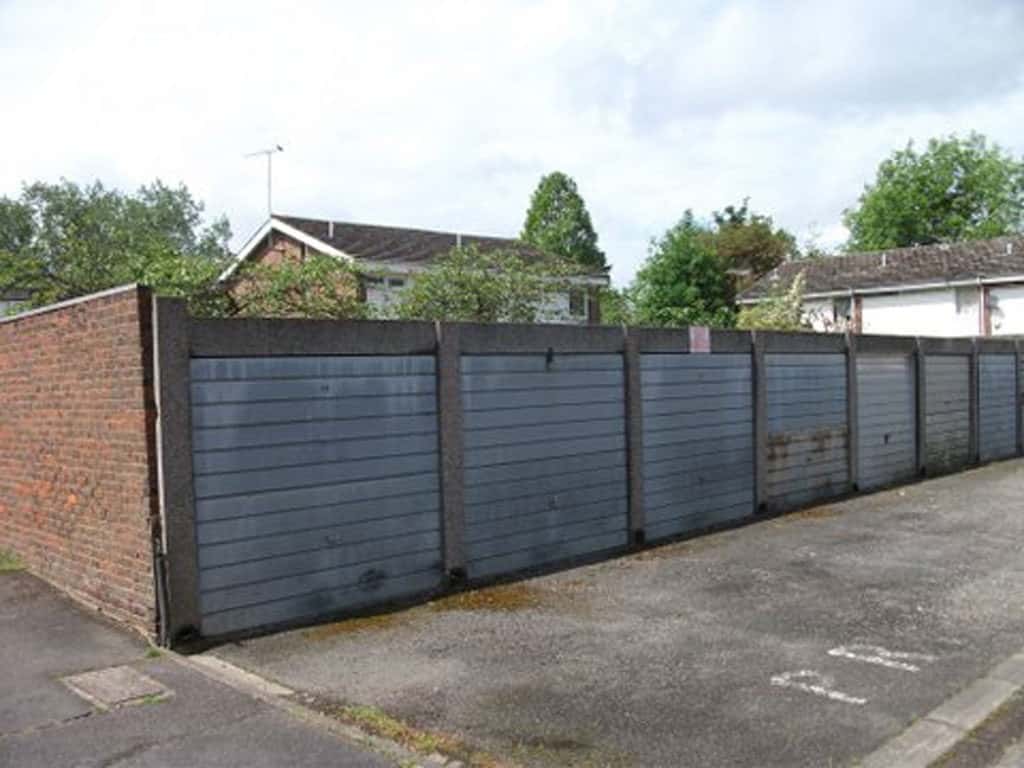
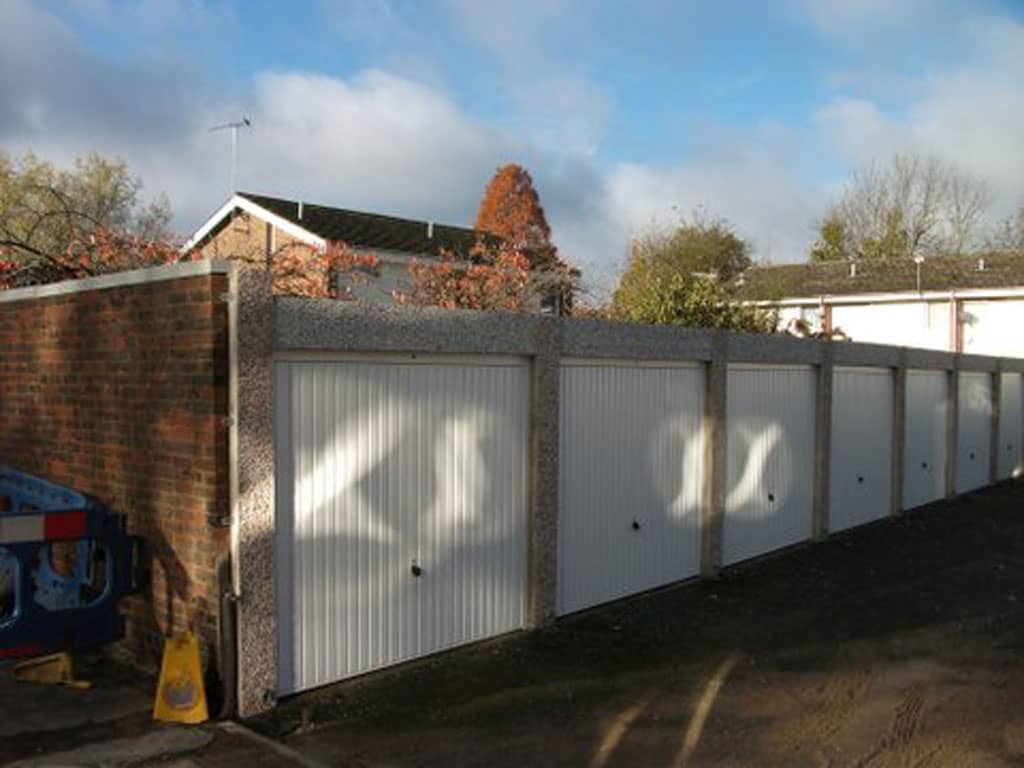
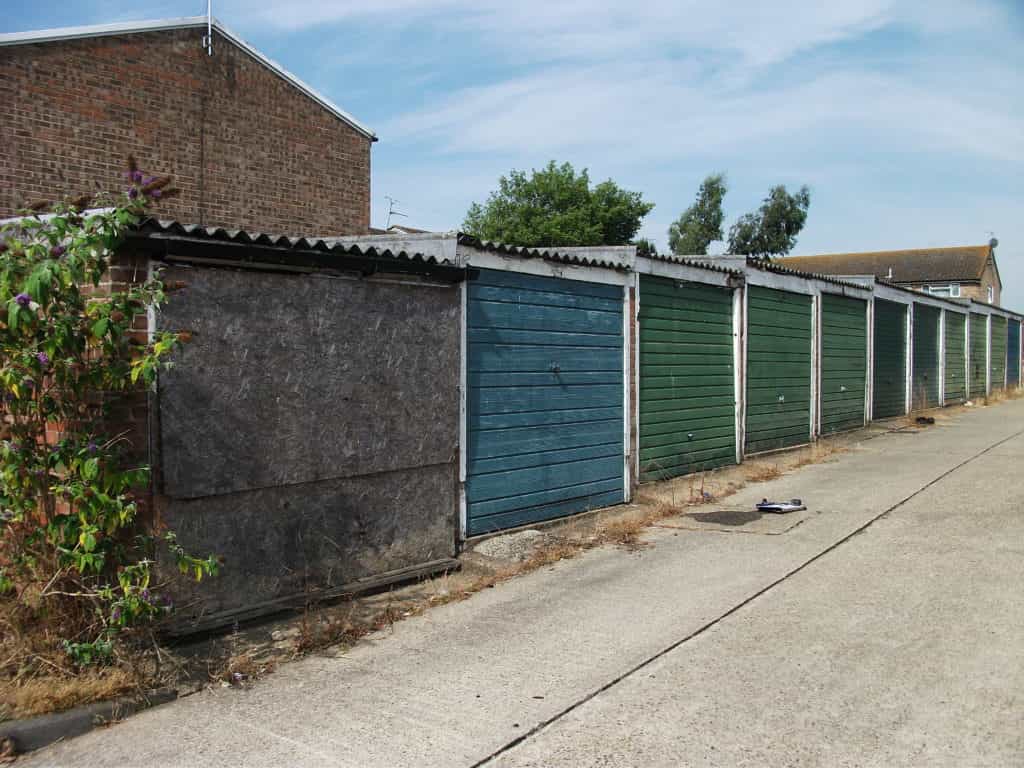
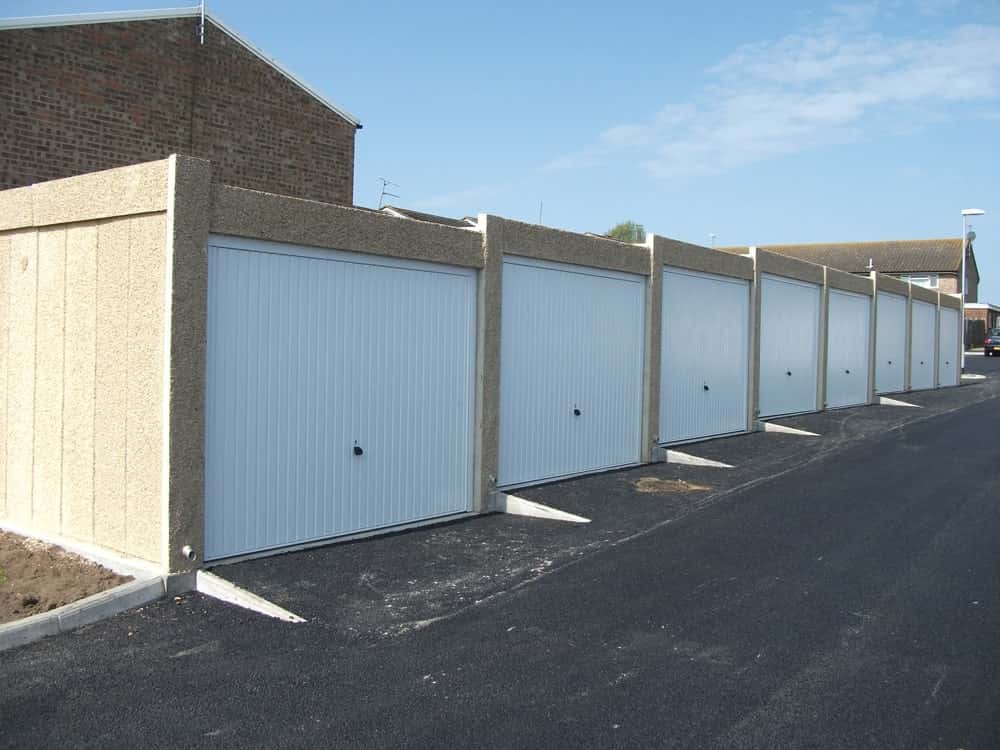


Page 3
More Before & After
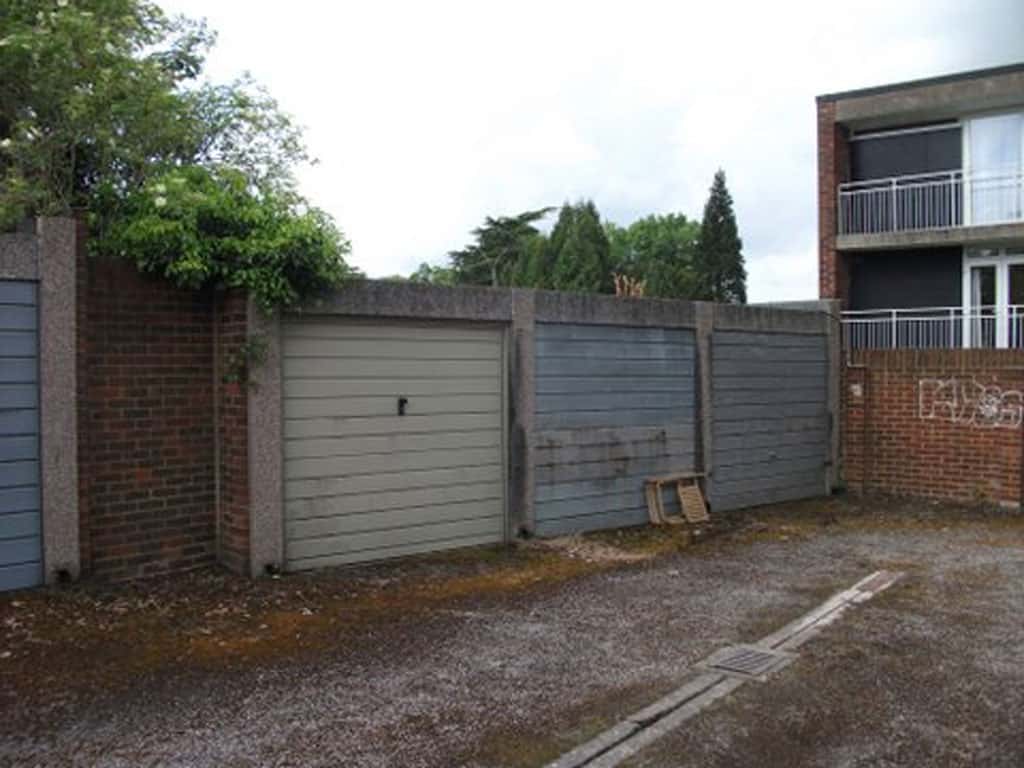
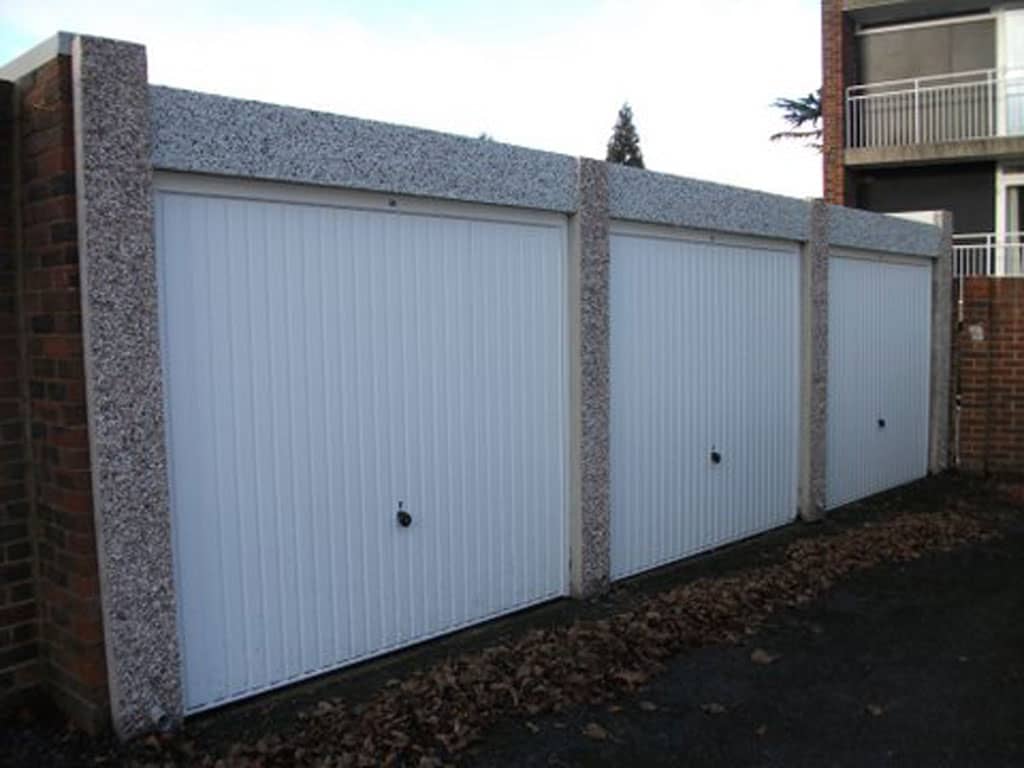


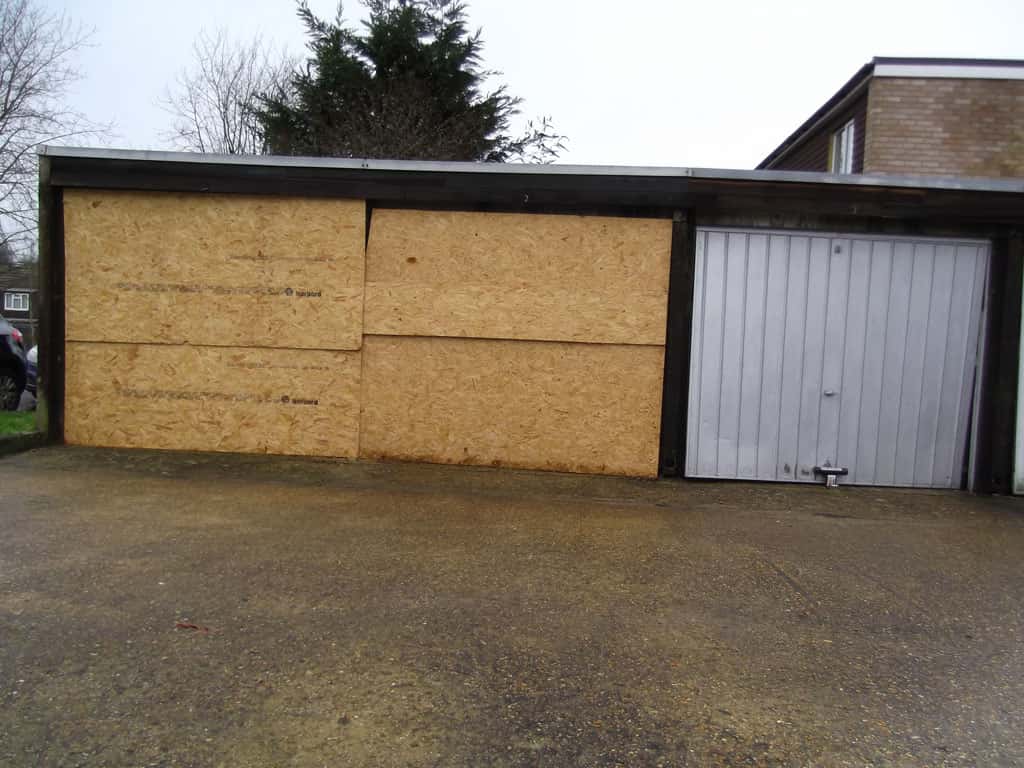
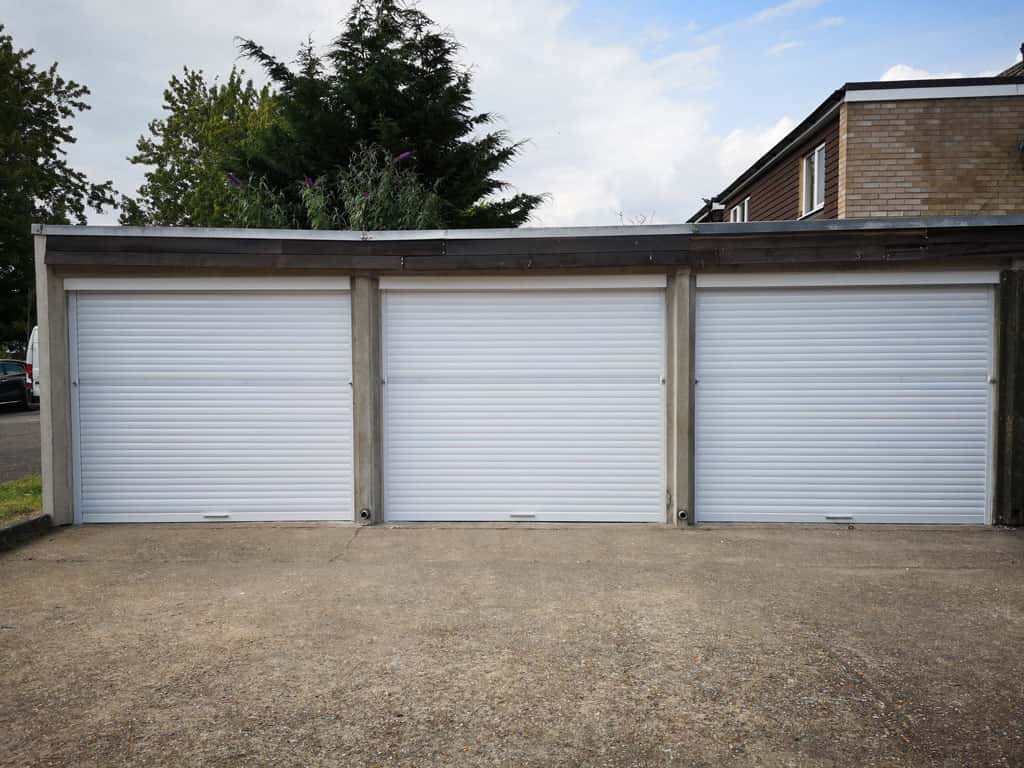

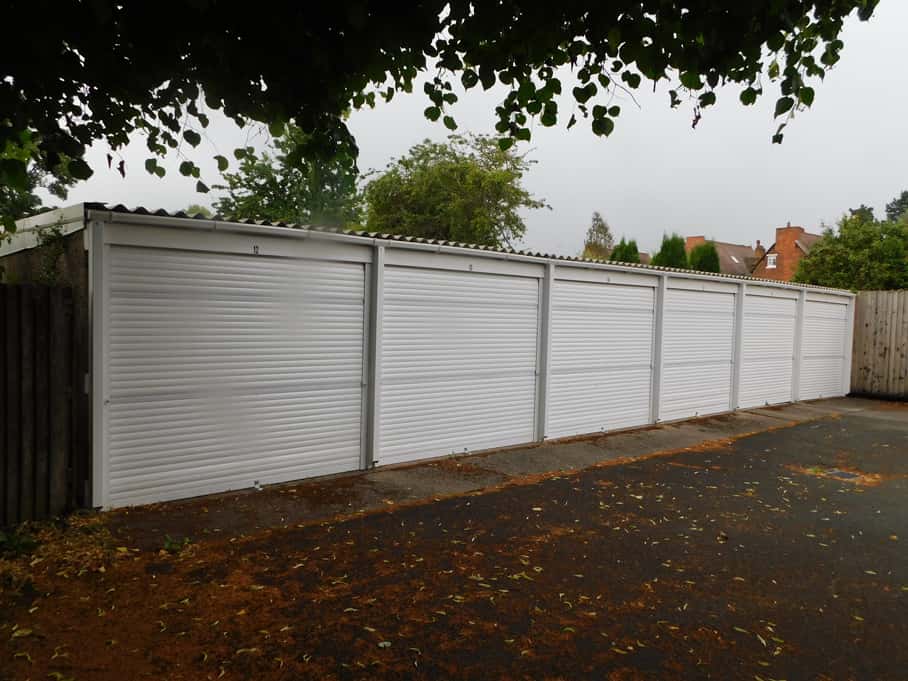
Page 4
Now for a more challenging refurbishment

This block of System B Garages was partly demolished by a large tree falling in the middle of the first four garages from the left hand end. While we have several moulds for the lintels and posts, of this type, we have but small numbers of moulds for the three types of panels used in this design. Without a quantity of the these moulds it would have taken weeks/months to make enough concrete panels to complete the job. Therefore we used standard Marley-Designed panels for the sides, rear and interwalls of the reconstruction.



Page 5
Another way to refurbish garages – but not our way!


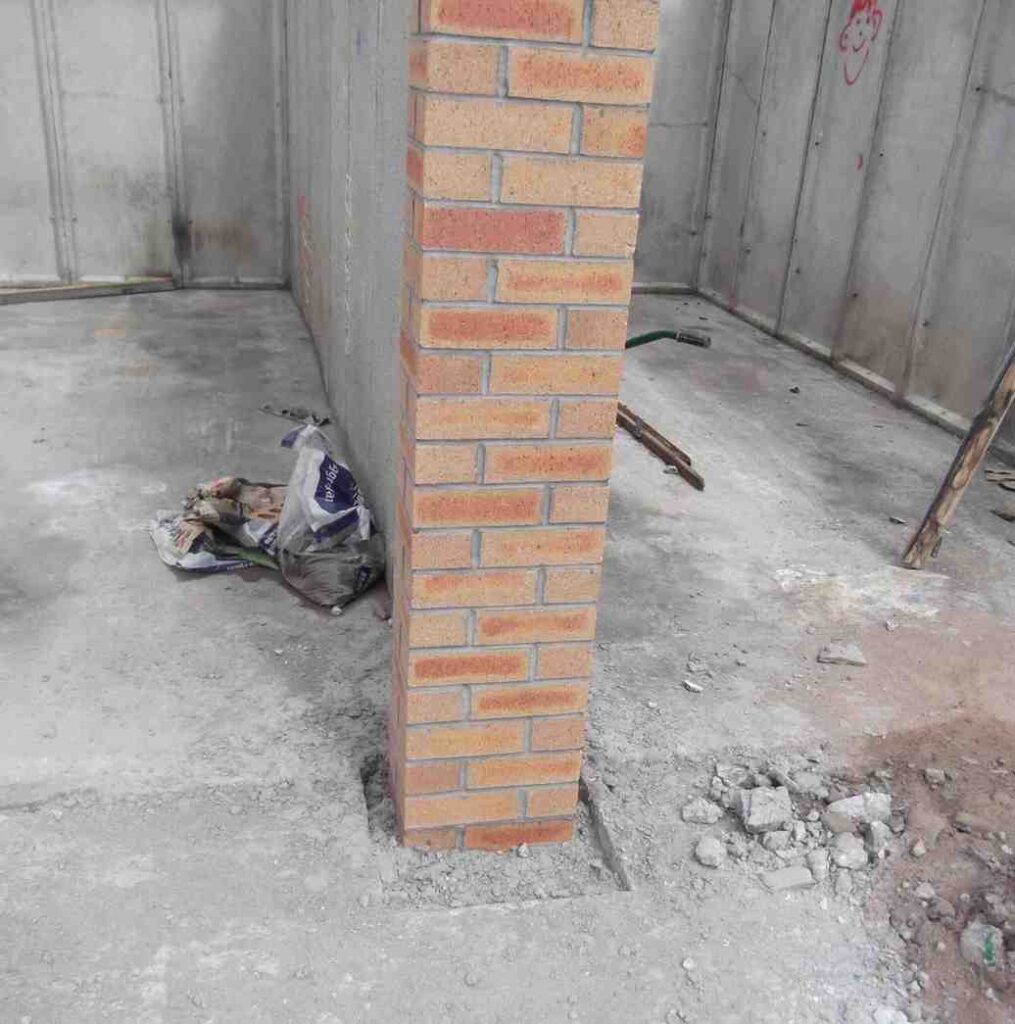
Page 6
And now for the Specifics
All about the Concrete
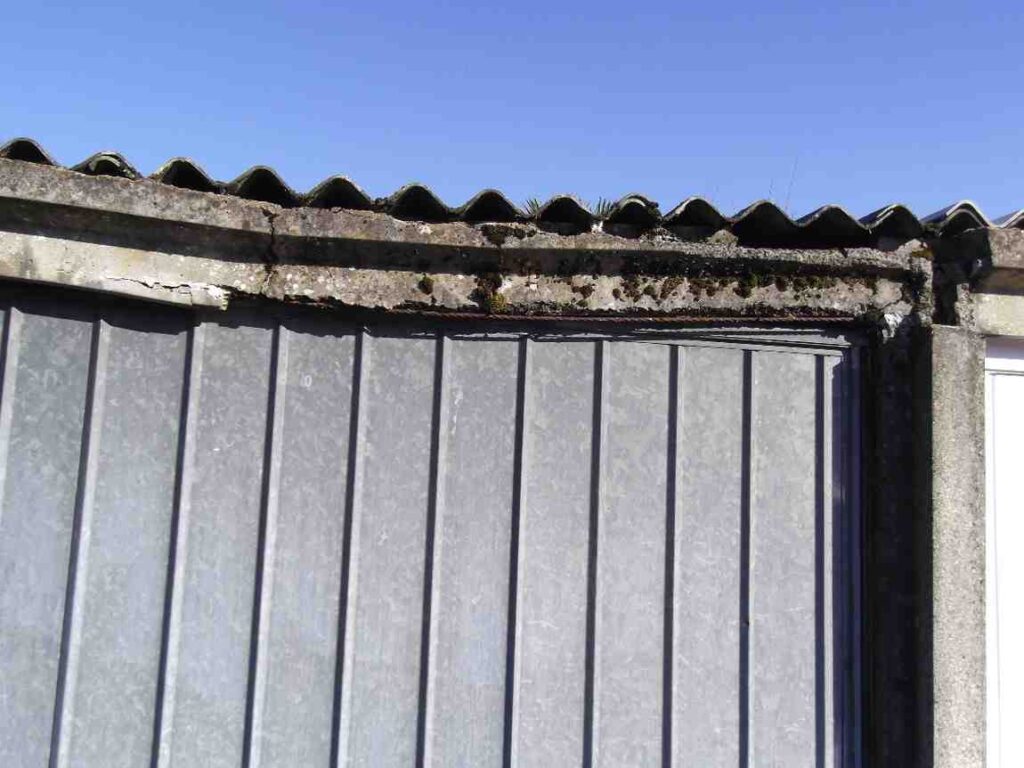
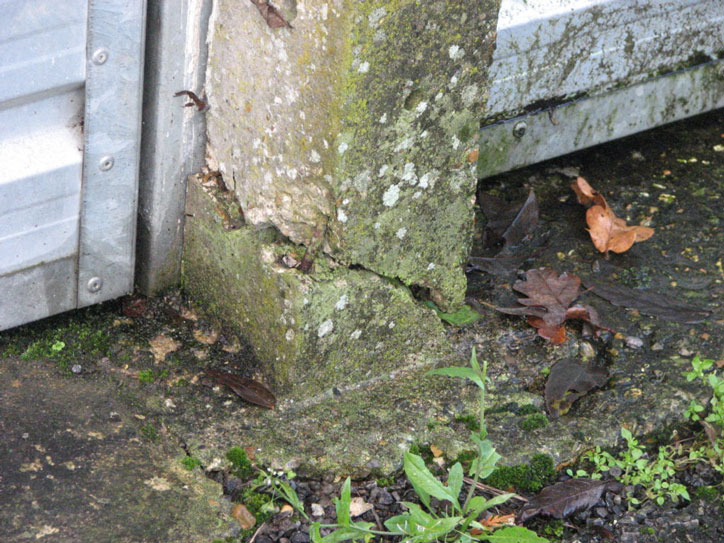

Block Refurbishment
Page 7
More problems with the concrete. With some Marley models there is a problem with the upstand at the top of the post/downpipe. This extension “blade” at the top of the post breaks off and falls. I weighs about 20lbs. This could injure anyone standing below it.
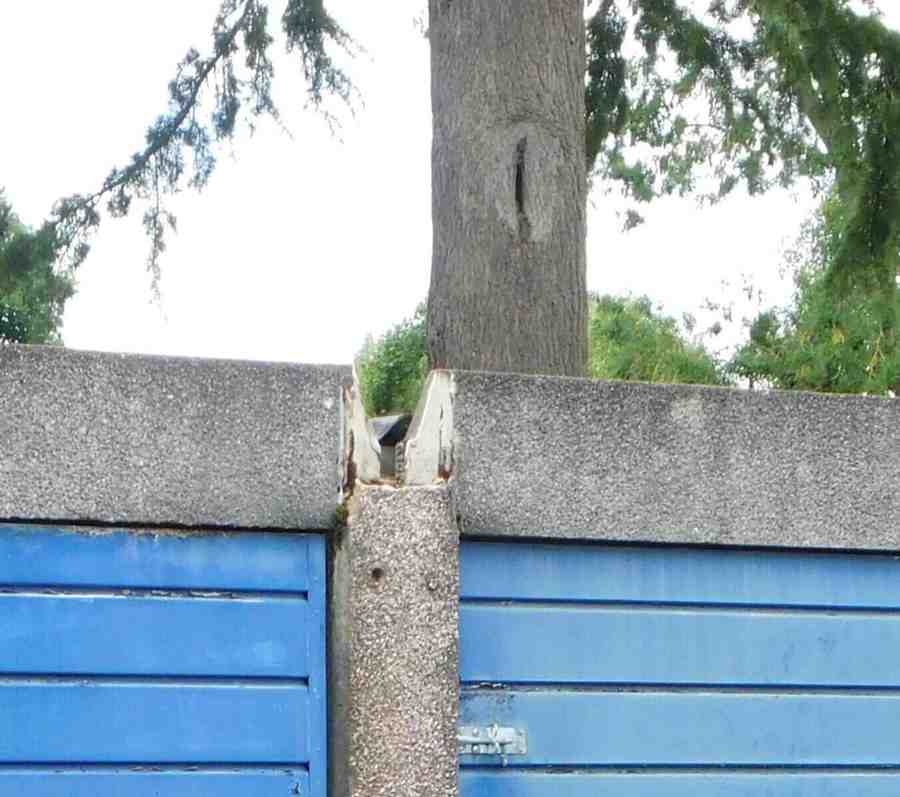
With System B and several other now obsolete types there are other problems.
An additional problem here is the post width used by Marley (and others using the same concept) to accomodate their rainwater downpipe. This measures 235mm in width and frames the door. This concrete post not only reduces the Wing Mirror Clearance (WMC) but splits or spalls zing shown. This is a result of water freezing in the blocked downpipes.
Wih a roller shutter door the post/downpipe is the same thickness as the garage dividing wall only the roller shutter door guides protrude into the WMC thus increasing the WMC to 2294mm. Therefore the extra WMC obtained over the original Marley door is 2294-2179=115mm (nearly 5 inches) and over a Hormann door 2294-2024=270mm (over 10 inches).
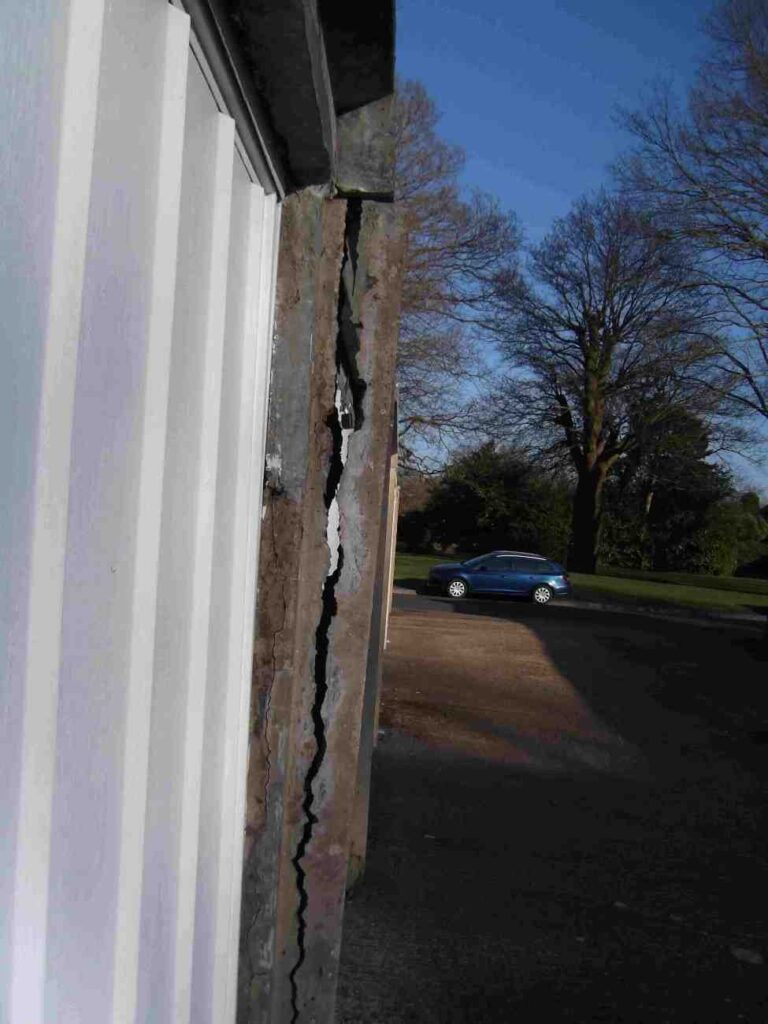
With all types – Purlin failure.
Inside the garage there are more hazards, in particular cracking purlins that support the roof. They start as hairline cracks, often resembling cobwebs. It they don’t then they need to be replaced, and soon.

Page 8
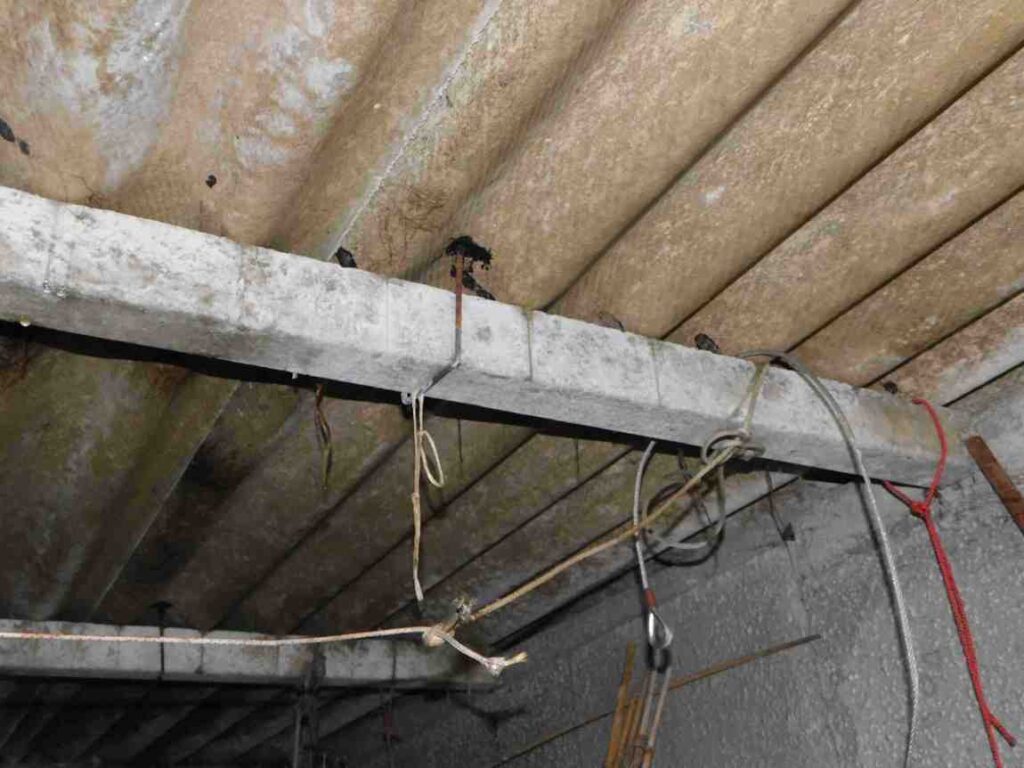
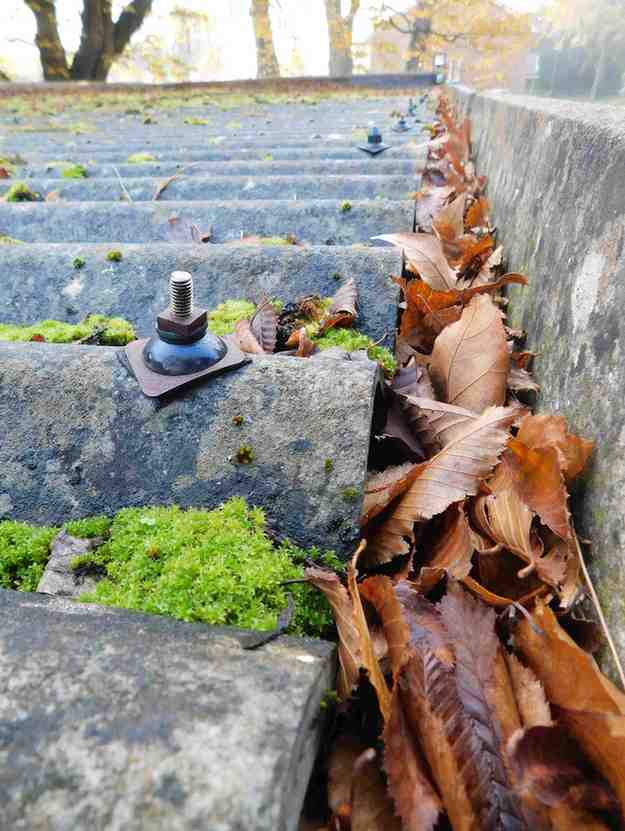
With System B the problem is much the same.


Page 9

All about Water and Drainage
System or battery garages have very nearly flat roofs, usually only about two degrees. They are naturals for allowing moss and vegetation to take hold as shown opposite. The original asbestos material and the replacement fibre cement sheets are a suitable growth base for such organic material and the sheets become porous, break up and leak. Plastic coated steel does not provide a surface for such vegetation to attempt to root and therefore does not become porous and remains waterproof.
Rain has to be allowed to drain away rapidly and without the obstruction of leaves and blown debris filling gutters and downpipes. Gutters often need cleaning out depending on the location, under trees for instance. The gutters in concrete lintel/gutters are small and easily block causing water to rise over the gutter-to-post joint and into the garage. This water then runs over the spring/lever mechanism of the door causing it to rust and eventually fail.
With the System X the moulded concrete lintel/gutters are replaced with powder coated aluminium extrusions which will never rot, spall, rust or crack. The concrete posts which contain the downpipes are replaced by square section aluminium extrusions which are also powder coated. The aluminium downpipe channel cross section has an area of 5250sqmm whereas the downpipe contained inside the concrete post is only 2043sqmm, or roughly two and a half times the capacity. So the aluminium post/downpipes are less likely to block and even if it did then frozen water in the downpipe will not cause the pipe to crack or split which happens with the original concrete versions.
Page 10
All about Ground Level Problems
On at least one in four sites we find that since the garages were built 50-70 years ago, resurfacing of the common access area has been carried out, one or more times causing the garage floor level to become lower that the access area. Naturally water flows into the garage.
When we refurbish garages our work is in regard to the replacing of the old components, not in building up the floor level. Another trade is involved which we can organise but it may be cheaper to obtain quotes locally.

Condensation – the facts
Anti-condensation material, sprayed-on, is a cost effective way to minimise the problem of condensation forming on a single skin steel or uPVC sheet. A compound is applied to the underside of the roof and this allows the sheet to absorb up to 1kg of water per square metre, reducing water dripping. This material can be applied to a variety of profiles both traditional corrugated and box profile.
Why condensation forms:
Condensation forms on un-insulated metal or on sheets of other material when the temperature and humidity conditions reach the dew point. The moisture in the air condenses onto the underside of the sheet. If there is a lot of condensation, drops of water form and start to follow gravity.
The traditional method for dealing with condensation is to try to insulate the roof so that the sheet temperature never reaches the dew point. An insulated roof is much more expensive than a single skin roof and is not always the most suitable choice.
How anticon material works:
Anti-condensation sheets reduce dripping by absorbing water and retaining it within the anticon material. When temperatures rise the water that has been absorbed by the material will start to evaporate back into the air and the material will dry out. It is vitally important to ventilate the building when using this type of material for this reason.
As mentioned above the material can only hold so much moisture and if a wet vehicle with a hot engine is parked in a garage during cold weather the temperature of the air in the garage is increased by the hot vehicle and thereby, the air in the garage can absorb more water from all over and under the vehicle. As the temperature falls during the night moisture will be deposited on the coldest surfaces which can be so intense that droplets form and fall resembling a leaking roof which is not, in fact, leaking.
All about Doors and Locks
Door Functions and Security
We are all aware that today’s vehicles are, in the main, wider and higher that those constructed at the time when Marley Garages first came onto the market (over sixty years ago). Of all the limitations that these older garages possess wing mirror clearance (WMC) between the door posts is the biggest problem for most of today’s users.
Page 11
At the time of their introduction and in order to provide maximum wing WMC, Marley designed and built their own doors, which went from post to post with no frame, however the operating mechanism decreased the WMC by 94mm (47mm on each side). Thus their WMC of 2273mm was reduced to 2179mm.
Part of the problem here is the post width used by Marley (and others using the same concept) to accommodate their rainwater downpipe. This measures 235mm in width and frames the door. This concrete post not only reduces the WMC but splits or spalls with time. This is as a result of water freezing in the blocked downpipes (more later). With a roller shutter door the post/downpipe is the same thickness as the garage dividing wall only the roller shutter door guides protrude into the WMC thus increasing the WMC to 2294mm. Therefore the extra WMC obtained over the original Marley door is 2294-2179=115mm (nearly 5 inches) and over a Hormann door 2294-2024=270mm (over 10 inches).
Recently the German door manufacturer, Hormann, have taken over the market, even to the point of buying out the last remaining UK manufacturer, Garador, so that low cost up and over doors no longer exist. Furthermore in order to sell a replacement product that is easier to ship, Hormann place a frame around their door and have labelled that format a “cassette door”. Whilst this is a practical solution that helps keep the door in good shape during transportation and fitting, it does mean that the WMC is substantially reduced. The apparent door width of 2108mm is further reduced by the operating mechanism to 2024 mm(42mm on each side)
Locking Systems
With our roller shutter door we offer two locking systems. Either or both can be fitted. One is the simple hasp and clip padlocking the base rail to ground which can be employed singly, or in pairs, the other is a plunger that engages with one of the solid slats in the door at mid-height so that locking and unlocking is possible without bending down. Cutting these side locks with an angle grinder is not so easy and very noisy. Even cutting the slats doesn’t work as the linkage continues in the guides which would require a 7′ long vertical cut to remove (difficult).
With our roller shutter door there is no mechanism. The spring and other parts are contained within the roll of slats. And, as an added benefit, there are no levers and springs exposed which could be a safety hazard. Plus all of the interior space is available for storage and shelving.

Doors – Up and Over
The problems
Once one of these doors suffers impact they distort and as they cannot be straightened. Then they jam and/or no longer lock properly. Also with time the lever/spring arrangements jam and the doors stick and require significant force (often beyond that of seniors) to operate
Page 12
Doors – Roller Shutter
The benefits
If the fronts of our new System LX Garage looks like its nearly all door, well it is! This is due to the use of customised roller shutter doors to make entry easier over conventional up-and-over doors. In real terms the side-to-side clearance increases by as much as 13 inches and the pass under clearance increases by up to 8 inches over that provided by current system (battery) garages. This is a valuable benefit as today many new vehicles are higher and wider.
Then on bottom edge of the base rail we have chosen a foam rubber seal as used in industrial applications to keep ground water out, and, as this is a standard industrial product it will be available for years to come, unlike purpose-made seals that cannot be found some years later. This seal is just visible under the base slat of the door. By comparison, up-and-over doors have a knife-edge “wiper-blade” seal that does not follow the minor bumps in the floor concrete.
Then there is the matter of opening and closing the door. To this end our roller shutter door has a handrail slat that can be seen in the photographs at just about waist level. This slat enables the door to be opened and closed without bending down or reaching too high. It was positioned by an MS sufferer.
The doorslats and frame are made from powder-coated aluminium extrusions so they can never rust. The single coil spring that counterbalances the door can be adjusted but from new the door requires very little effort to raise and lower. Ideal for older folk!
One final and huge benefit relates to damage rectification. One sees dented and damaged up-and-over doors all too often. These doors cannot be straightened and have to be replaced or they jam or can no longer be locked. Our roller shutter doors require only new slats to be slid into place at a cost of a few pounds each, as opposed to around £900 for an up-and-over door with fitting!
Storage
System Garages are often used for general storage and not for vehicle garaging. To provide more options for community storage Leofric have developed a new range. MiniStores as shown below. Call 01386 430 121 for further details or check on this site under Our New Models – MiniStores. Those shown below were built for Oxford City Council.
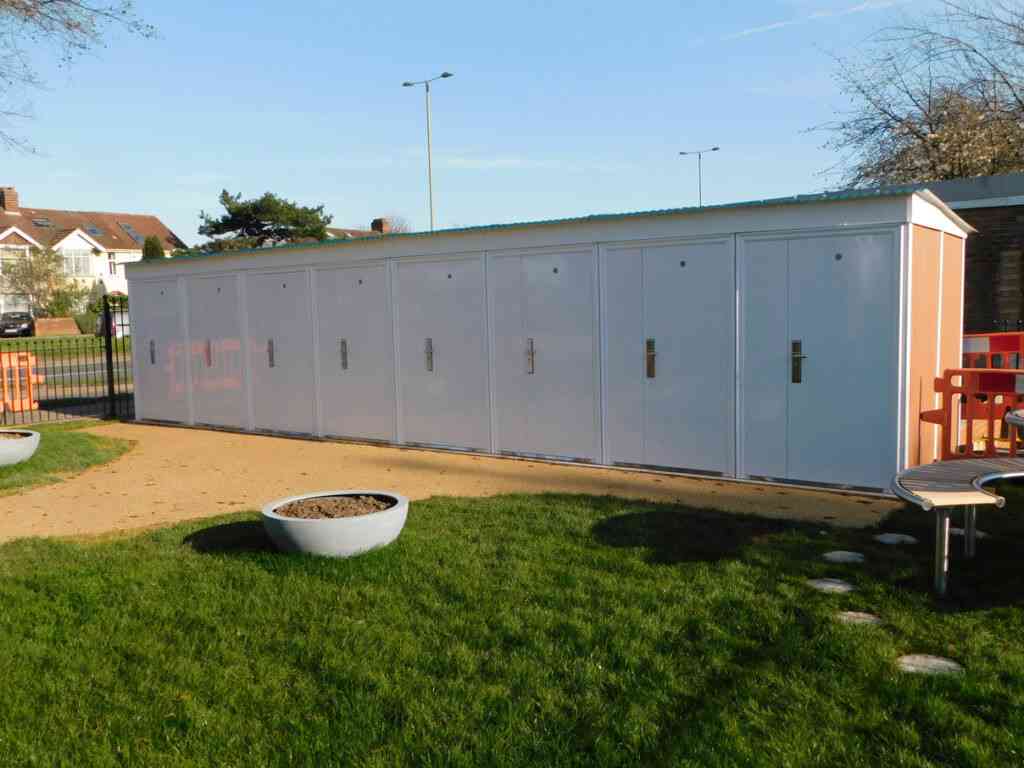
Page 13
More about Safety, Liability and Security
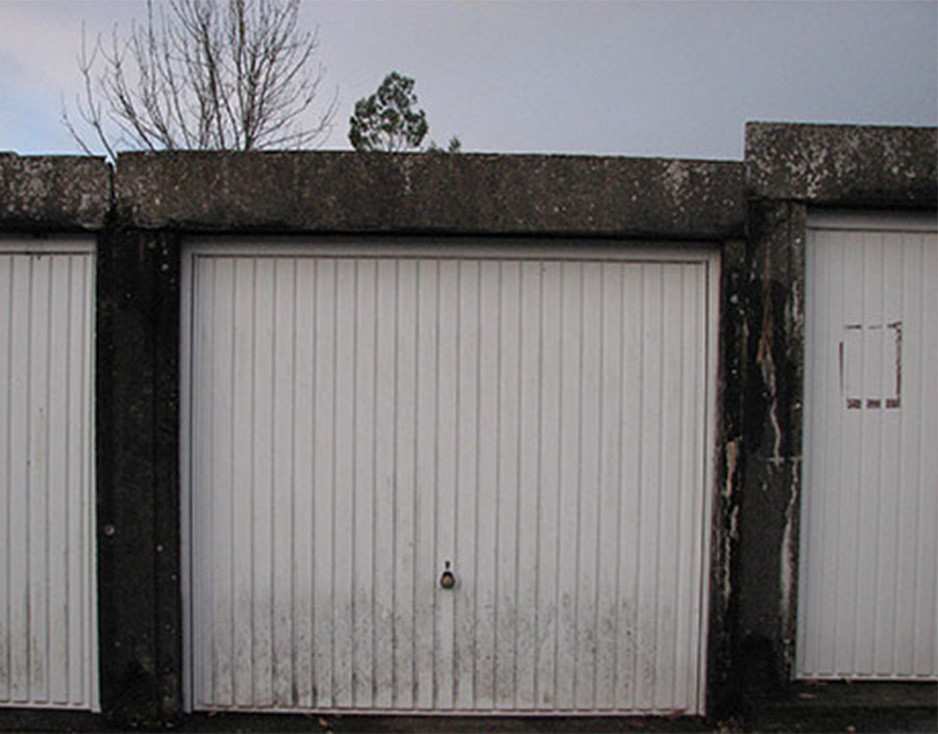
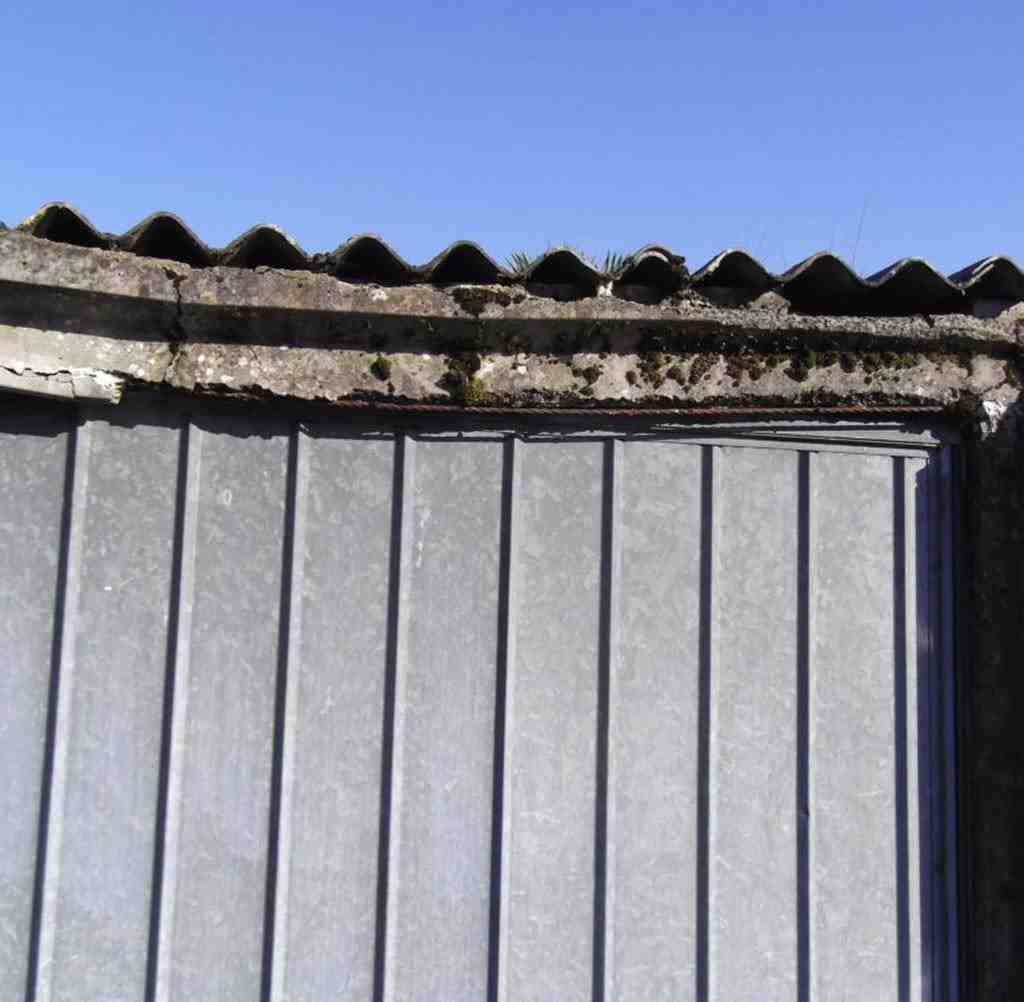
So the ideal System or Battery Garage would have non-corroding lintels, non-corroding downpipe posts to carry the rainwater away, a component to stop under panel water ingression and inexpensive, current guttering to add a modern look at very low cost. Our new System LX meets all of these criteria.
Page 14
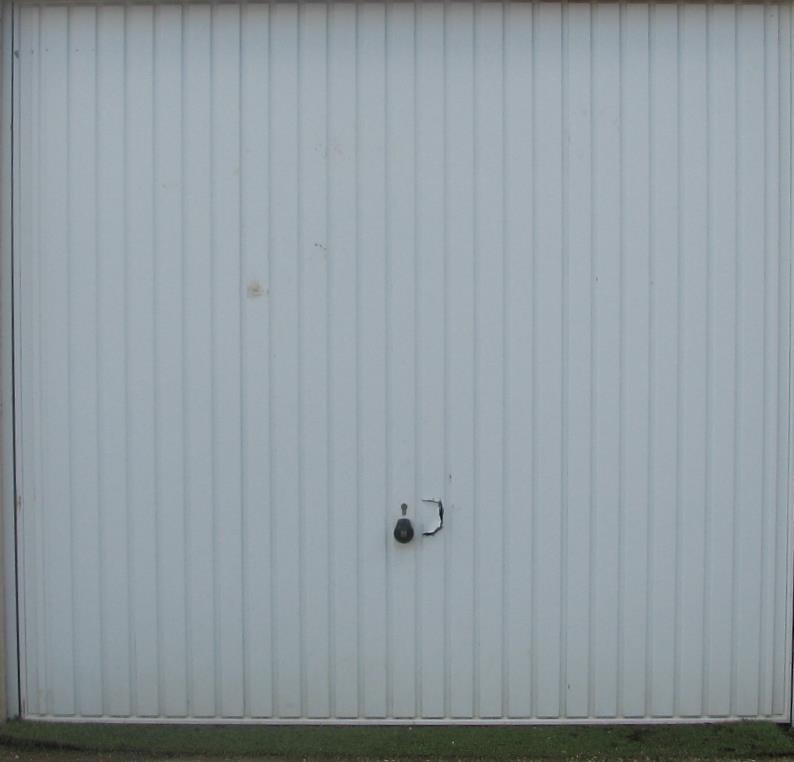
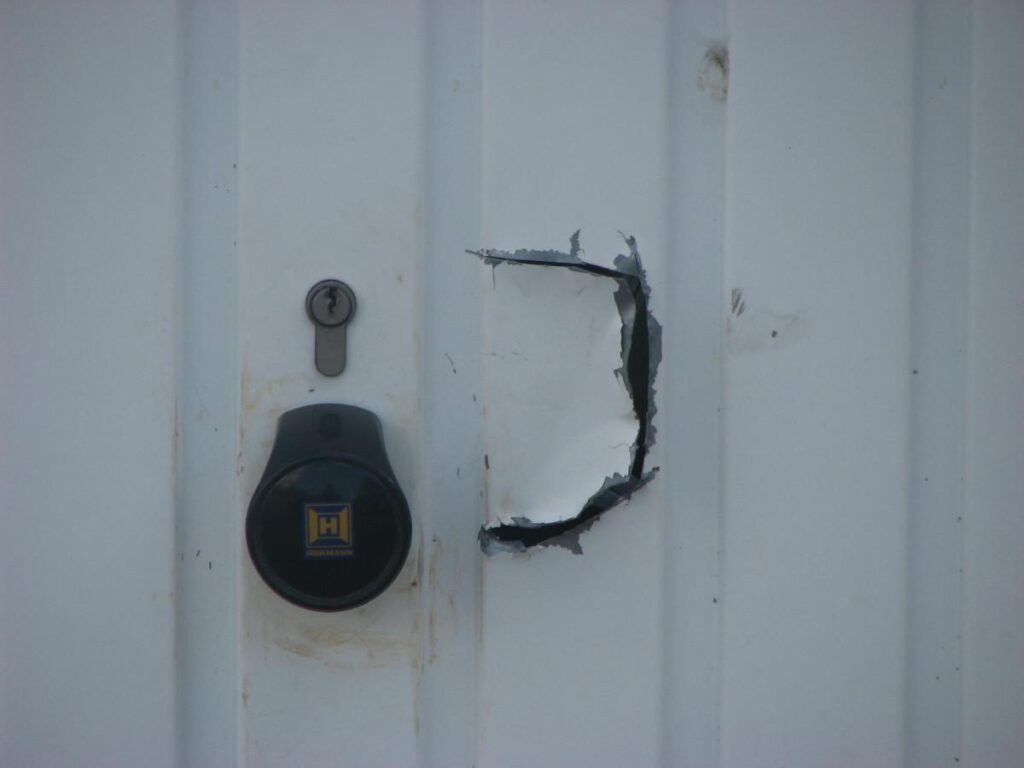
Page 15


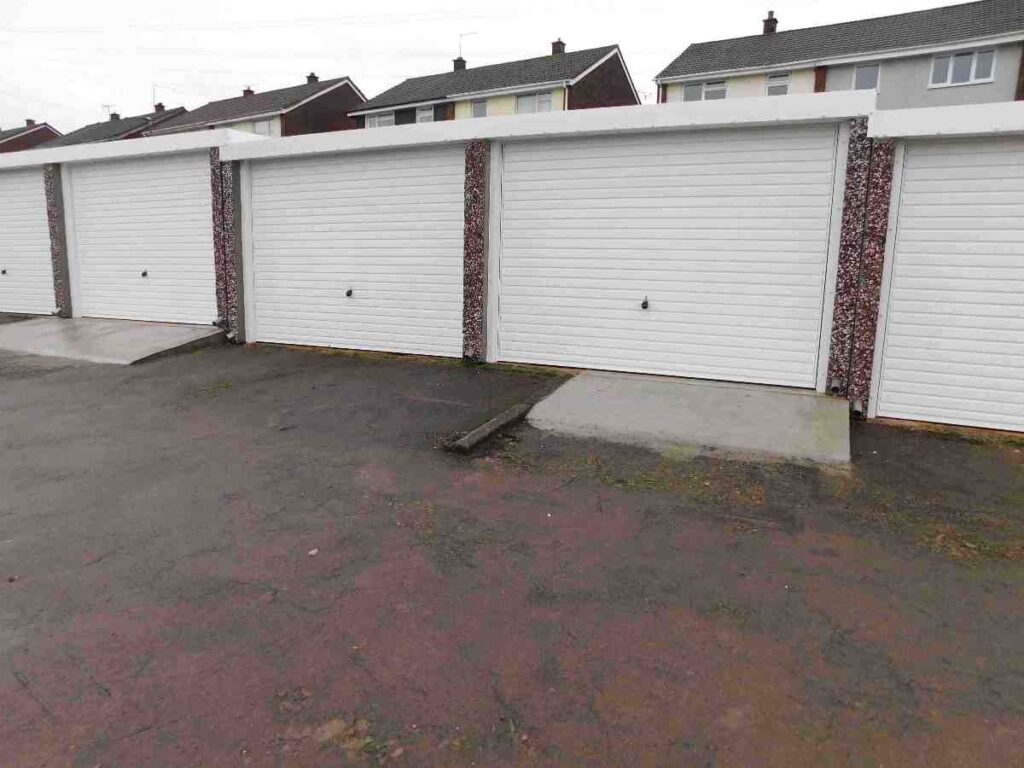
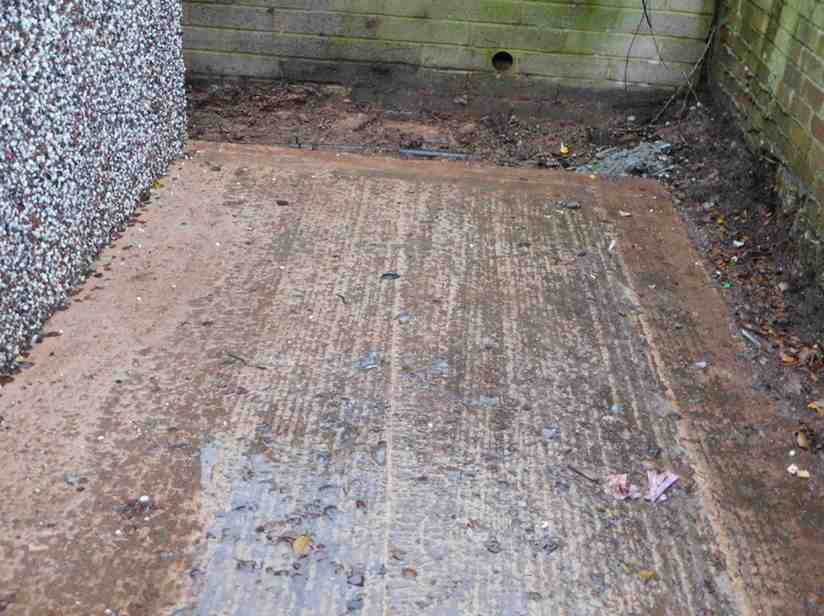
Note the aluminium joining post in the centre of the rear wall. In this garage this post has increased the width by 76mm (3″) which means 3″ of extra wing mirror clearance when driving in. Also on the outside of the building the post has sockets to support solar panel arrays or lighting or security camers, even flower baskets! These posts can be inserted into the walls at any point giving a multitude of options.
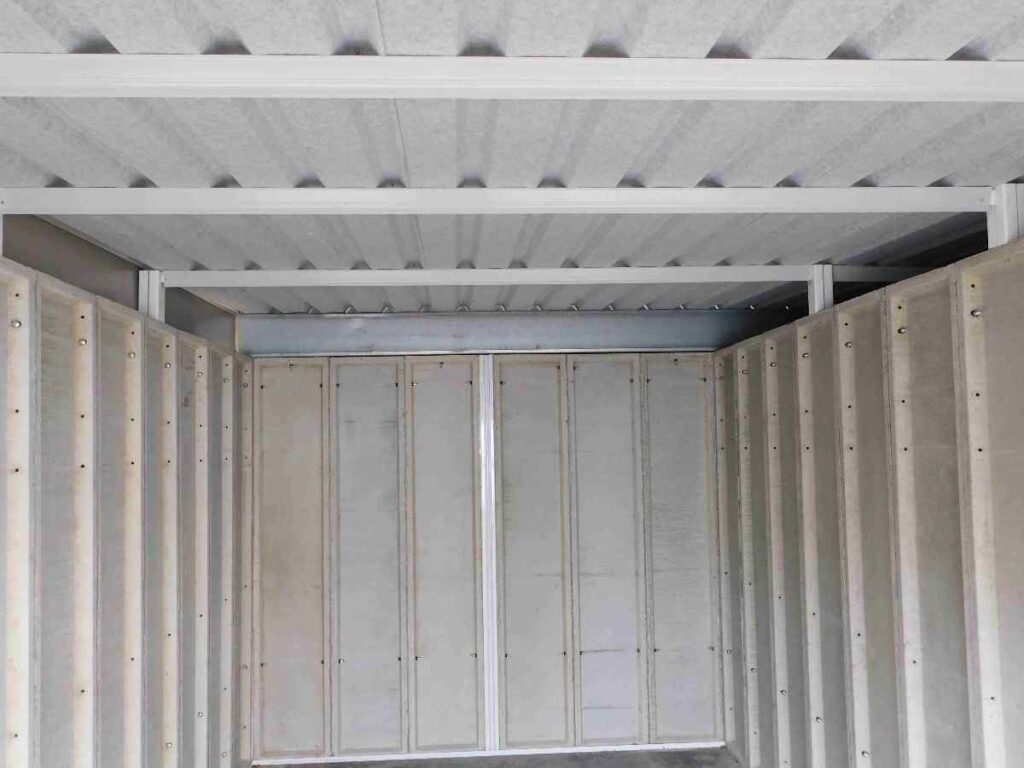
Page 16
All about Maintenance Problems
The fascia gutter cover on the right (not ours) needs to be removed for gutter cleaning. This envolves removing and replacing 30-40 self tapping screws, which after a few removals will have opened up their hole so that they no longer hold and larger screws will be needed. With our gutters you just blow or brush them out. See the roof view on page 10.
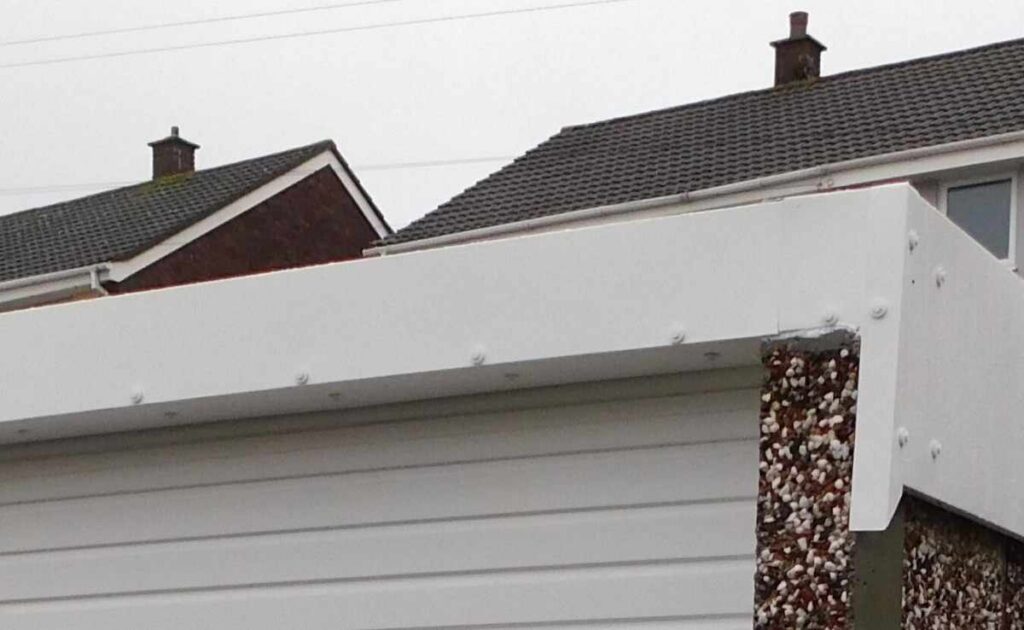
Yes, this is the front of the garage. In our System 8FX we use accessible square flow uPVC guttering that is easily cleaned by anyone with a short ladder and no tools.
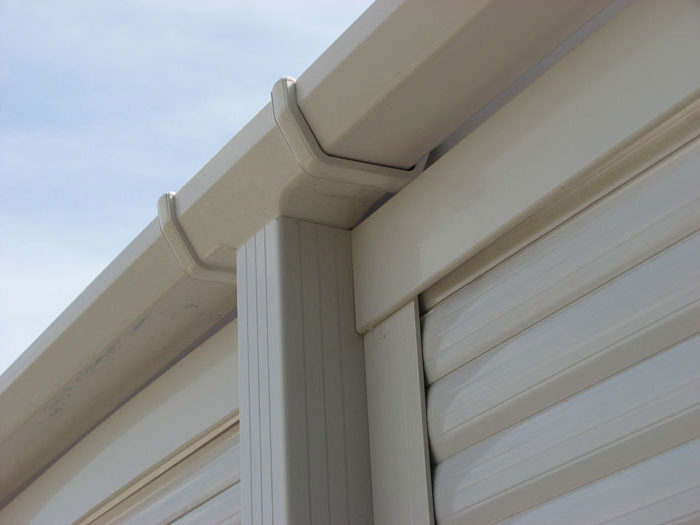
All about Collision Damage
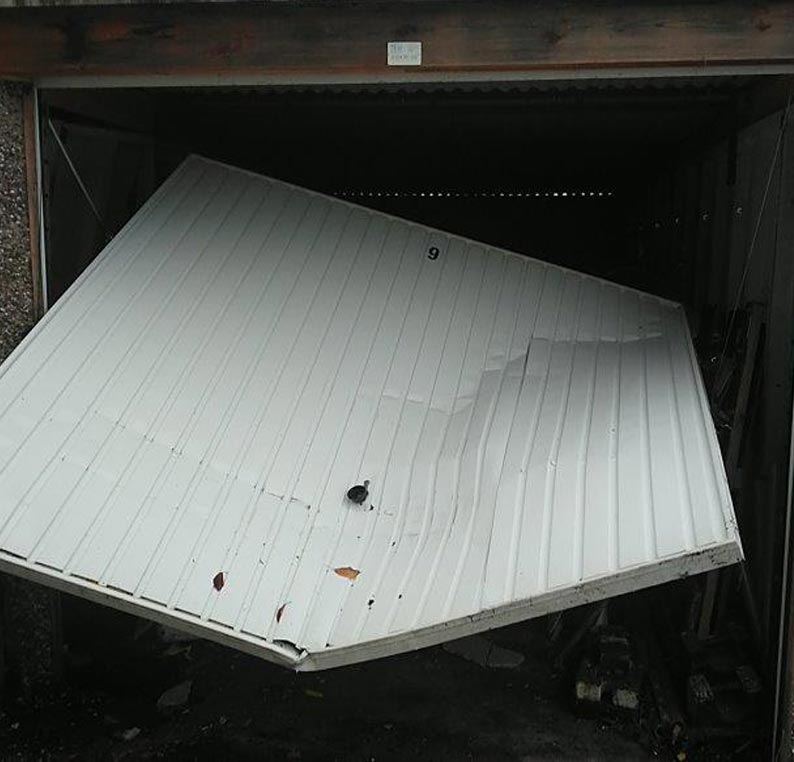
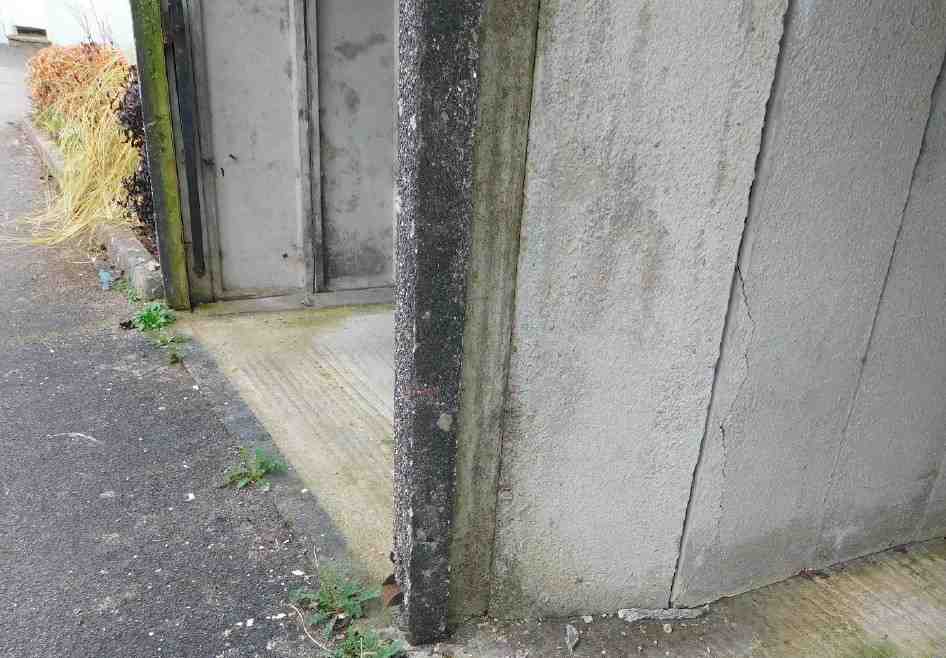
Page 17
All abouts Costs
There are two kinds of expense related to battery/system garages – one off repairs and block refurbishment and the approach is different.
All One-off repairs
This is required where there has been some kind of impact. A vehicle hits the garage or a tree falls on the roof for instance. Occasionally a garage within a block may have deteriorated to the extent that chunks of concrete are falling from a lintel that is breaking up. In this case it is better to look at the block as a whole for there will be other garages in the block in a similar state and total refurbishment of the block will prove to be much more cost effective. Apart from the Marley and Leofric Ranges of garages we have moulds for other brands long since defunct and can usually provide a viable solution. However these replacement parts contain hand-made wire re-enforcement elements and require careful handling to ensure no cracking in the hardening stage, and even with great care taken the yield is not high and the costs reflect that. Evidence of the difference in the re-enforcement between Marley and other brands can be seen in how they disintegrate. Marley units spall (concrete comes away from the rebar) System B from a manufacturer long since gone, breaking up along the lintel. Note in the photograph how the concrete has collapsed onto the door which is now the only thing holding it up!
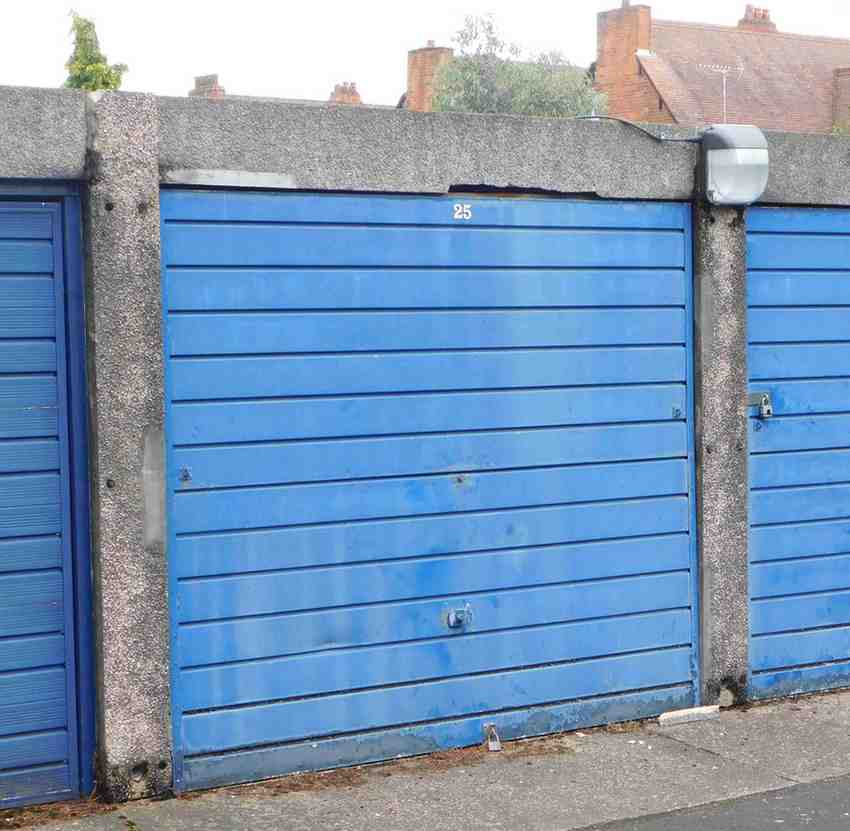
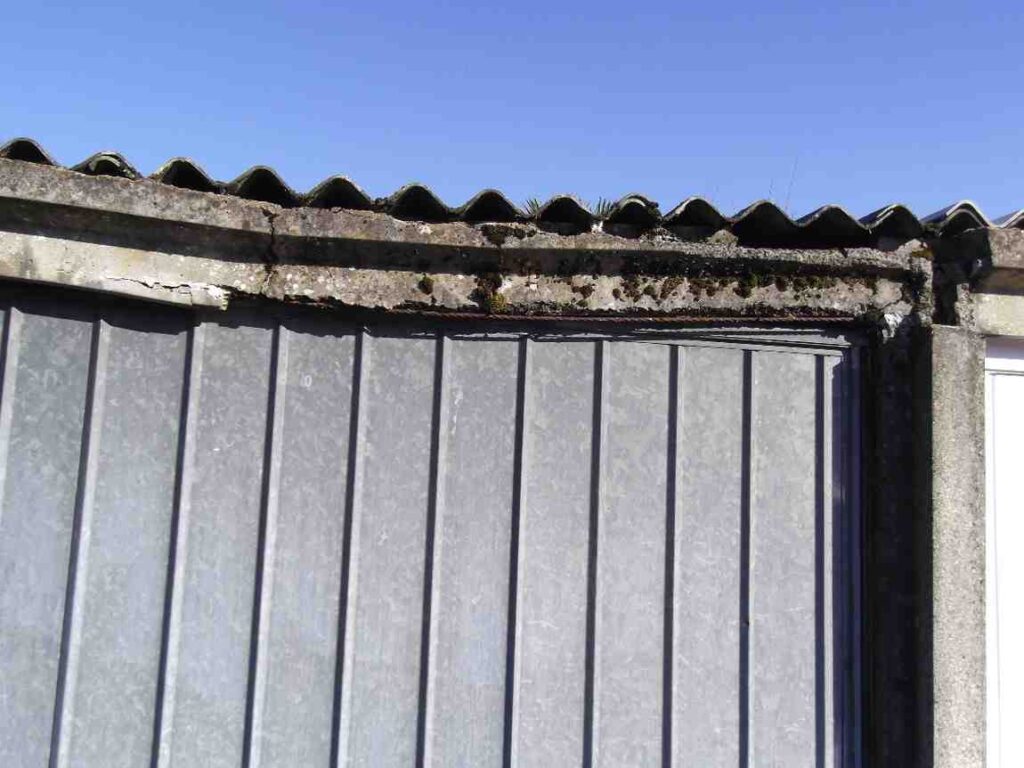
Page 18
System LX Battery Garage Detail

The front post which doubles up as the down post with 2.8 times the capacity of the current pipes that are encased in concrete. Virtually no chance of a blockage.
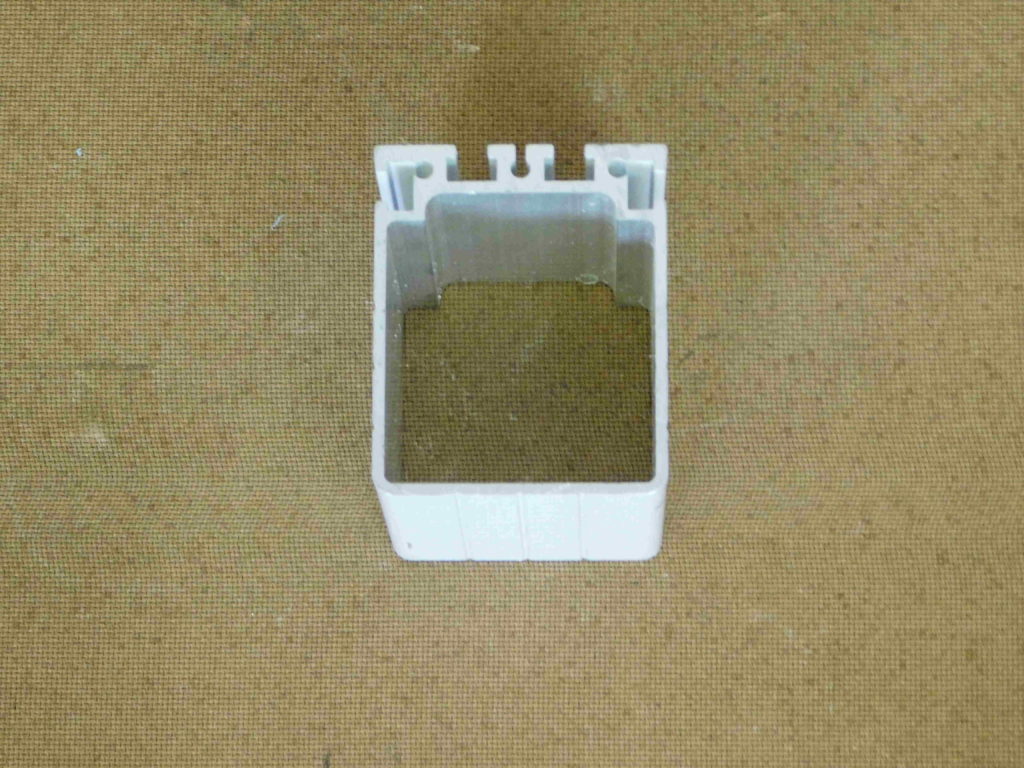
The roller shutter door guides slide into the front post. This gives an integrated lintel support section equal to an “I” Beam measuring 200mm by 150mm and 5mm thick. Which is massive.
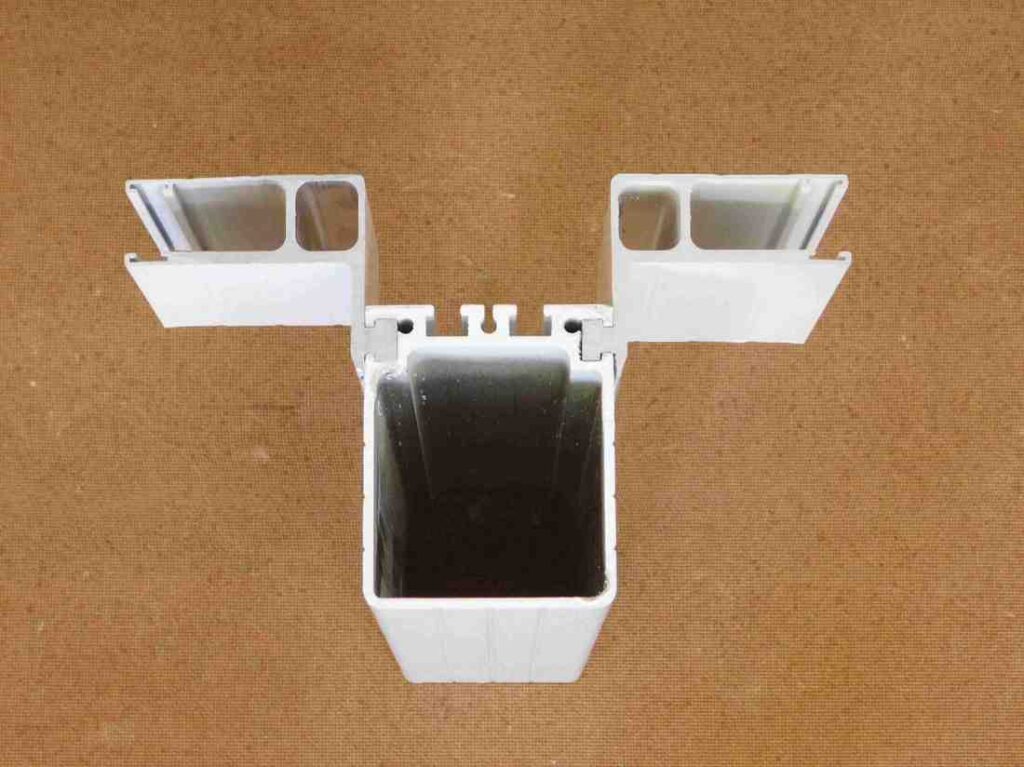
The “Z” shaped alumnium lintel which supports the roof sheets is fixed to the post/guides combo.
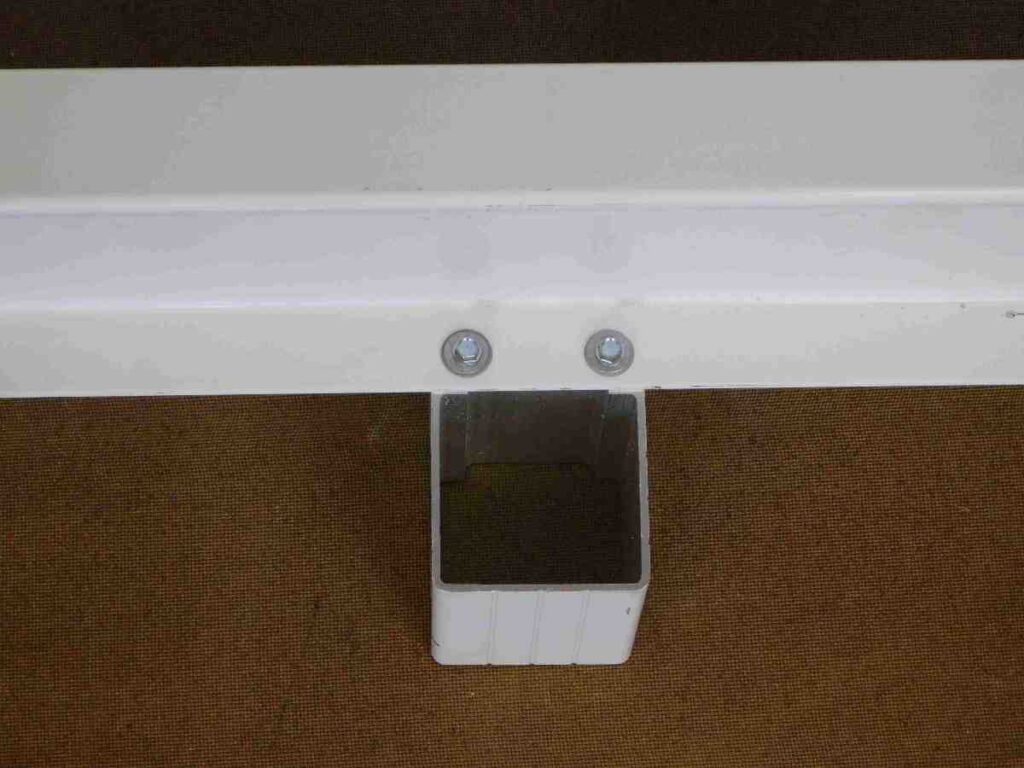
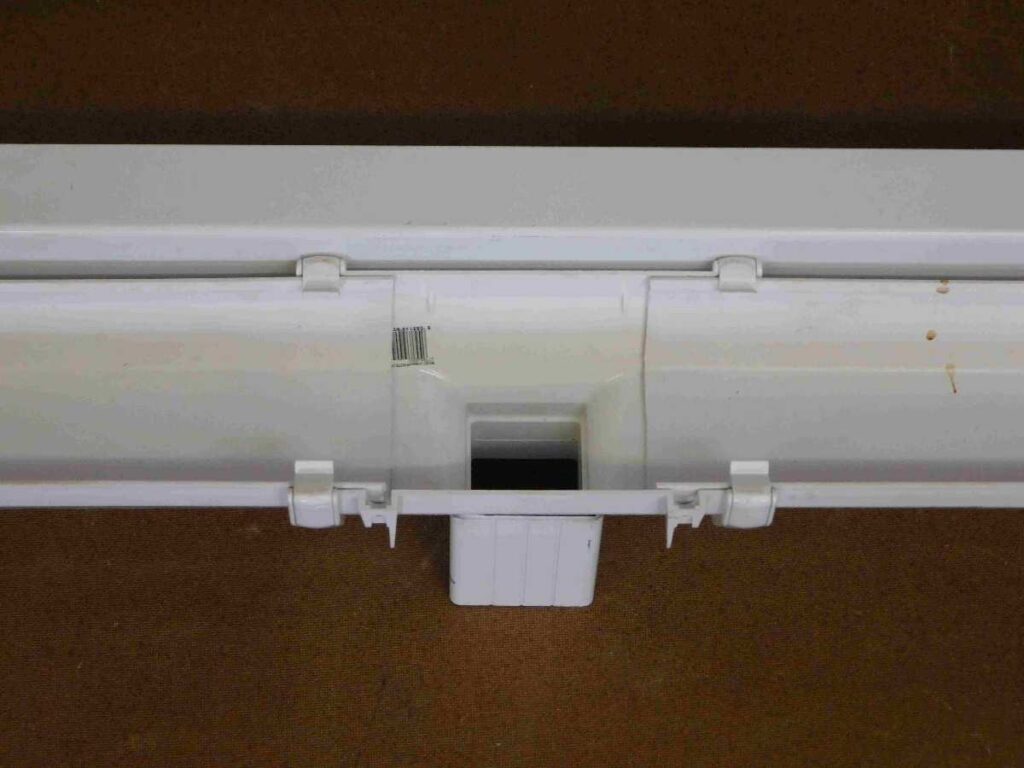
Page 19
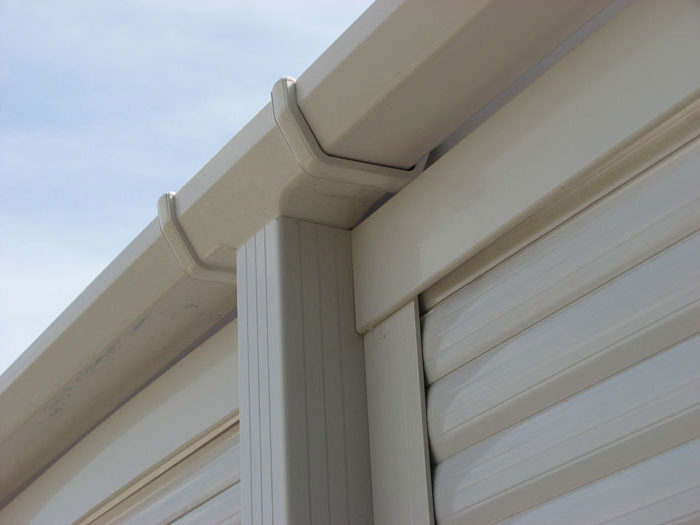
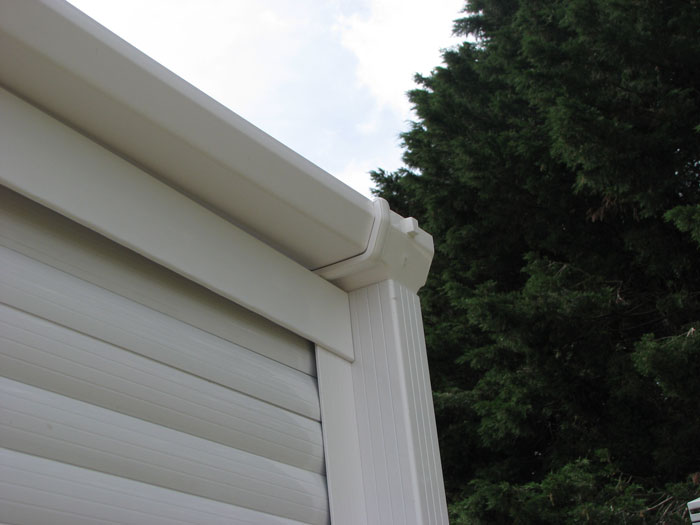
The aluminium downpipe/post will not block easily, unlike the interpost pipes of earlier models. In fact the new post/pipe has about three times the capacity of the original Marley design or the System “B” Type .Debris drops out of the pipe and is easily brushed away.
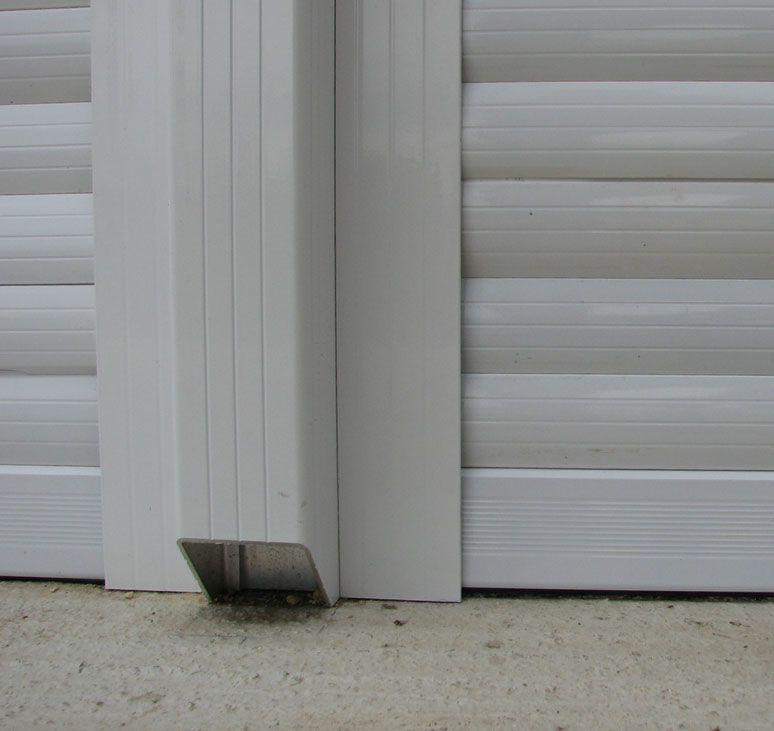
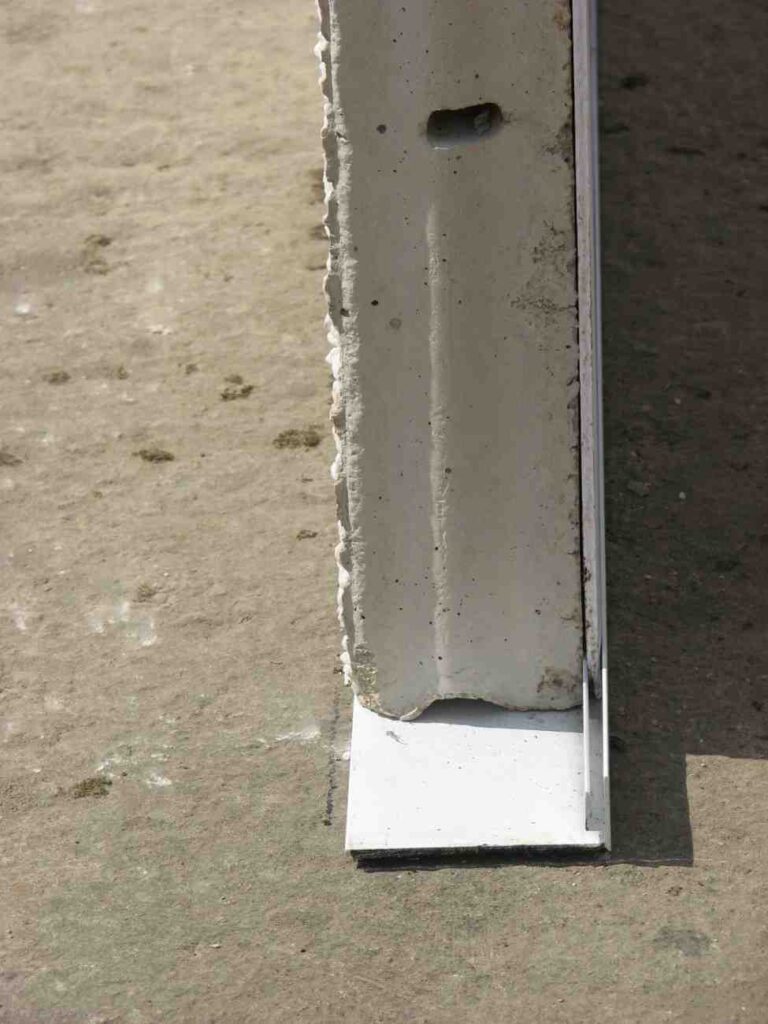
Page 20
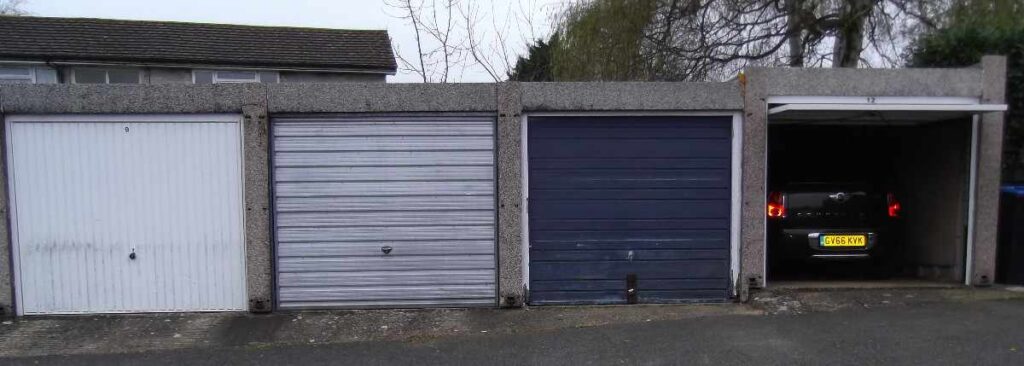
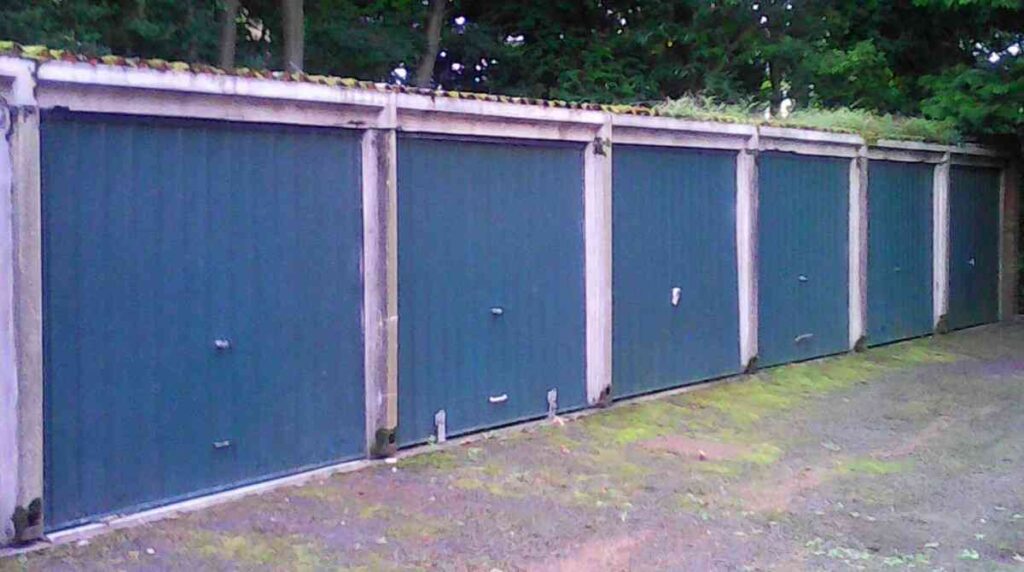
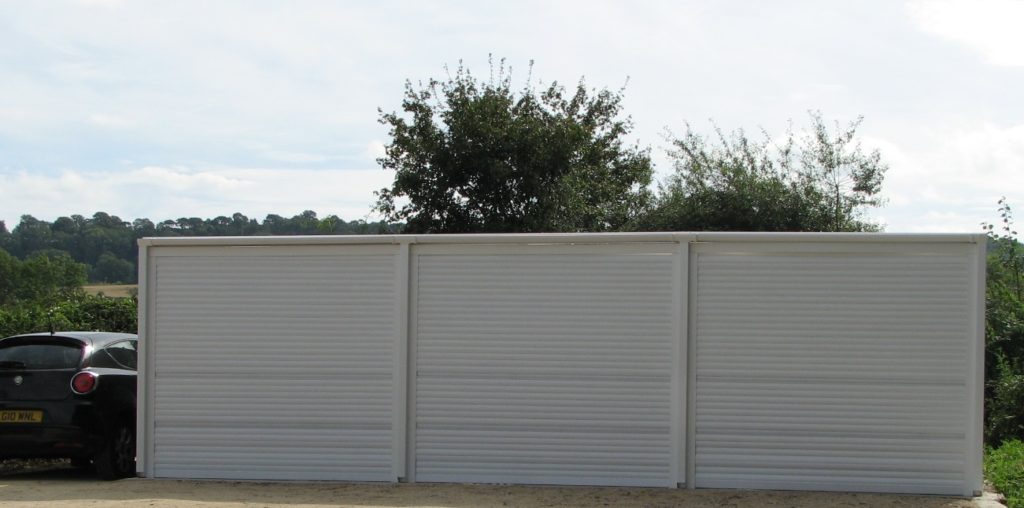
Page 21
The listing of Existing
Systems Garages
with Details of the
Options Available
System B
Very popular design. Often seen in the Midlands and the South. Manufacturer went out of business probably 50 years ago. All parts have been re-moulded by Leofric and are available. Can be converted to System X fronts and Roller Shutter Doors. For more information see Page 27.

Page 22
System C
Similar to Marley and Leofric Models in that they feature 16″ wide wall panels that are 7′ high. Not tongued and grooved like Marley. Manufacturer went out of business about 10 years ago. Can be converted to System X fronts and Roller Shutter Doors. Few examples around.
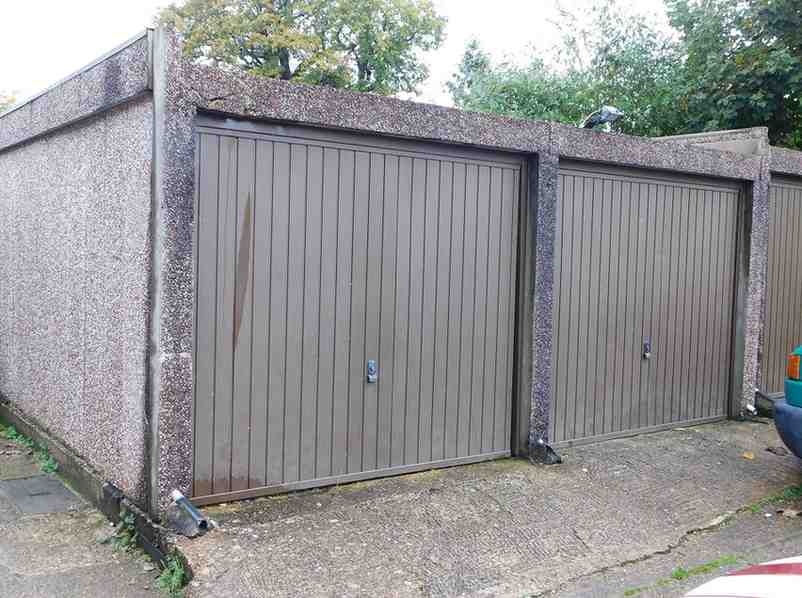
System E
Unknown manufacturer. Posts are embedded in the base. Walls are Post and panel construction. No parts available. Best demolished. No Further information.
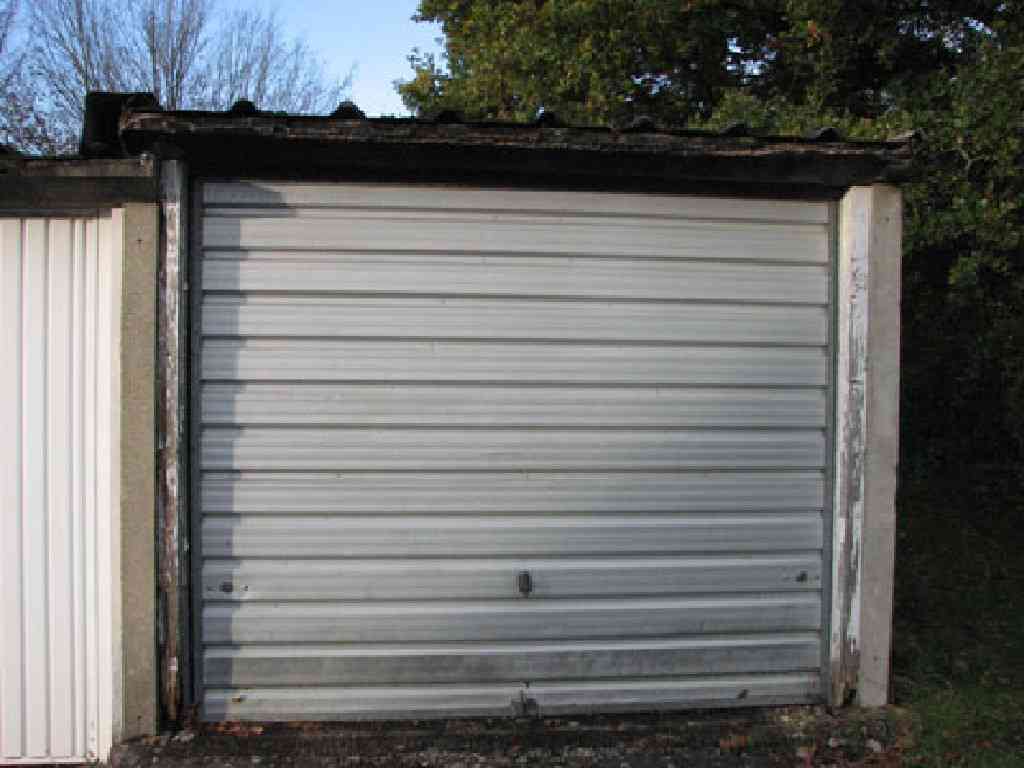
System K-8F
This is a Post and Panel Garage System with concrete fascia/gutter/lintels and downpipes. No parts available but easily converts to System X fronts.
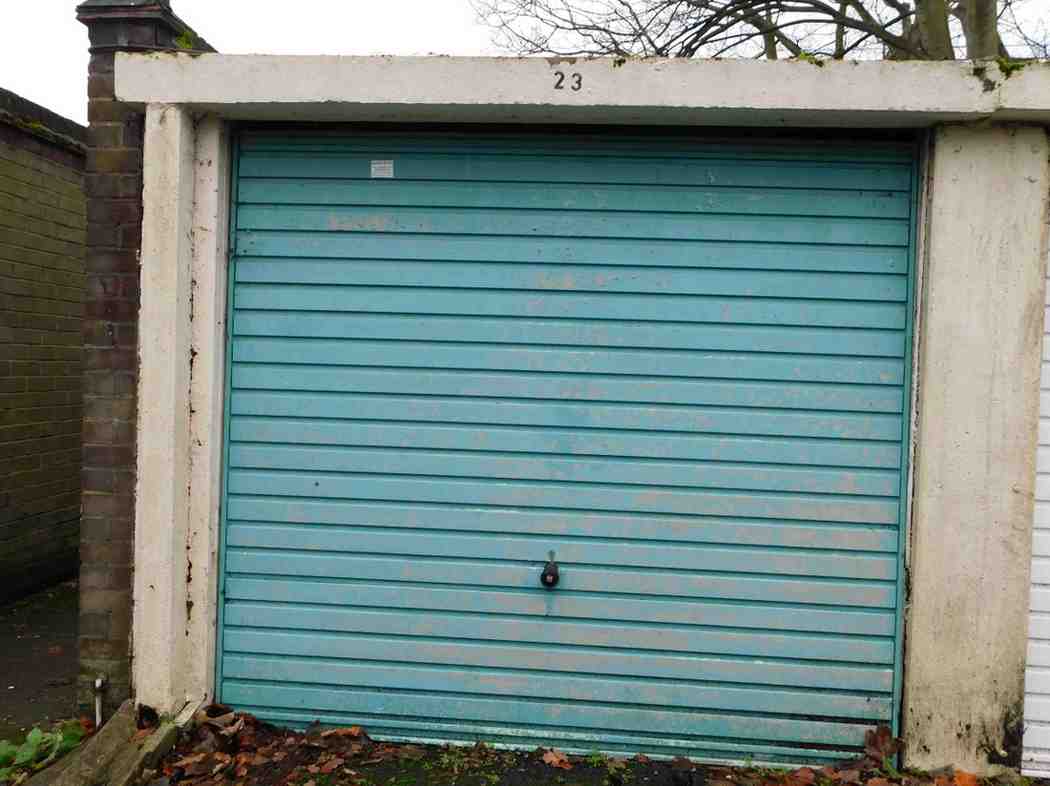
System L
Early Leofric Model – all parts available. Can be converted to System X fronts and Roller Shutter Doors. For more information see Page 28.
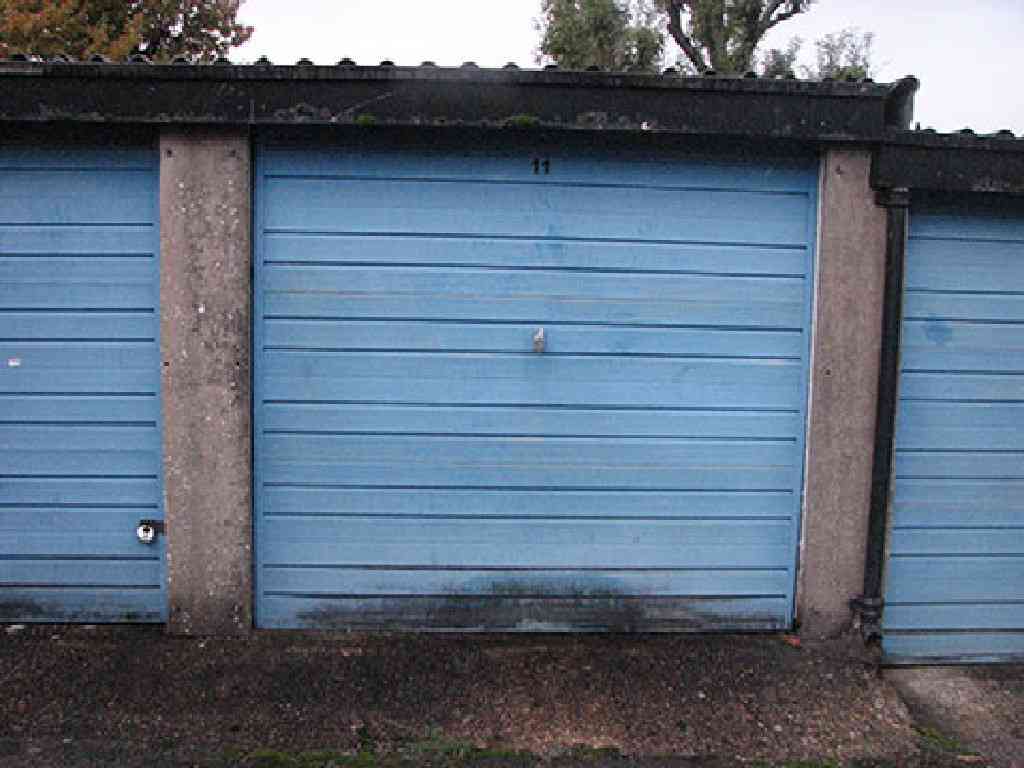
System M-8G
Early Leofric Model – all parts available. Can be converted to System X fronts and Roller Shutter Doors. For more information see Page 29.
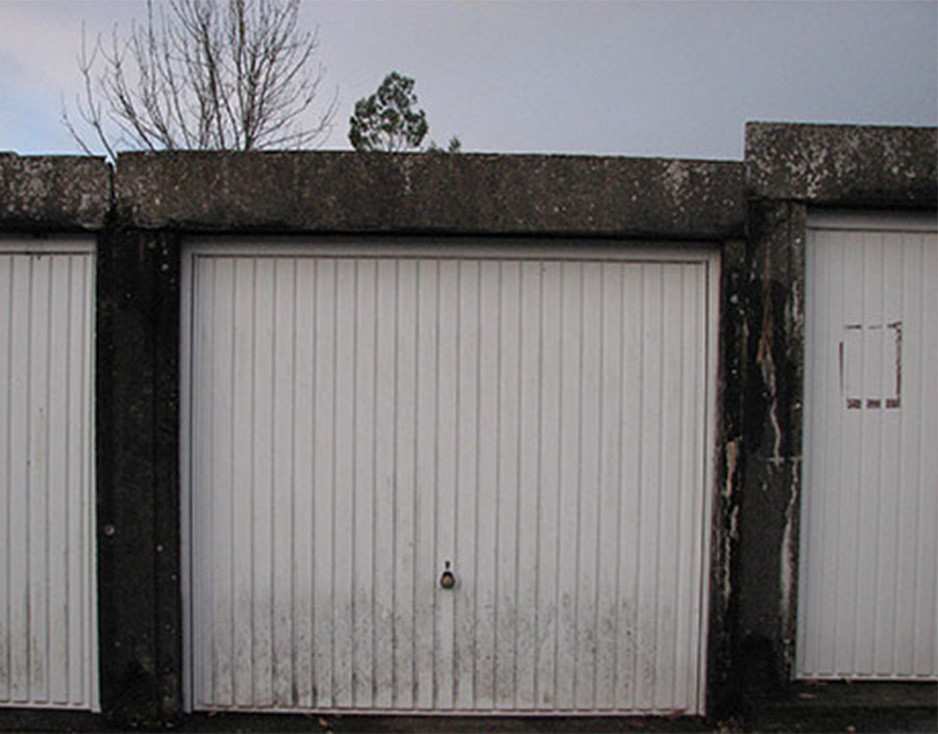
System M8/9R
Very early Marley Garage – extra wide rear-sloping design using Marley A63 panels. Can be converted to System X fronts and Roller Shutter Doors.
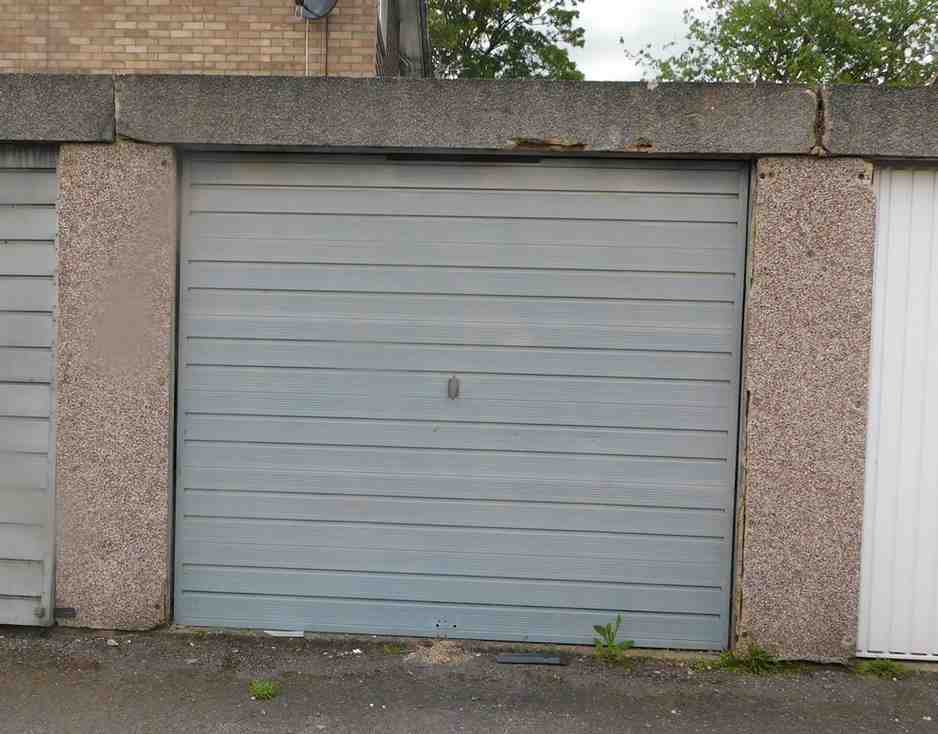
Page 23
System M-H
This garage style used Marley’s Top-of-the-line Heritage Range in a
Battery format. All parts are available. For more information see Page 30.
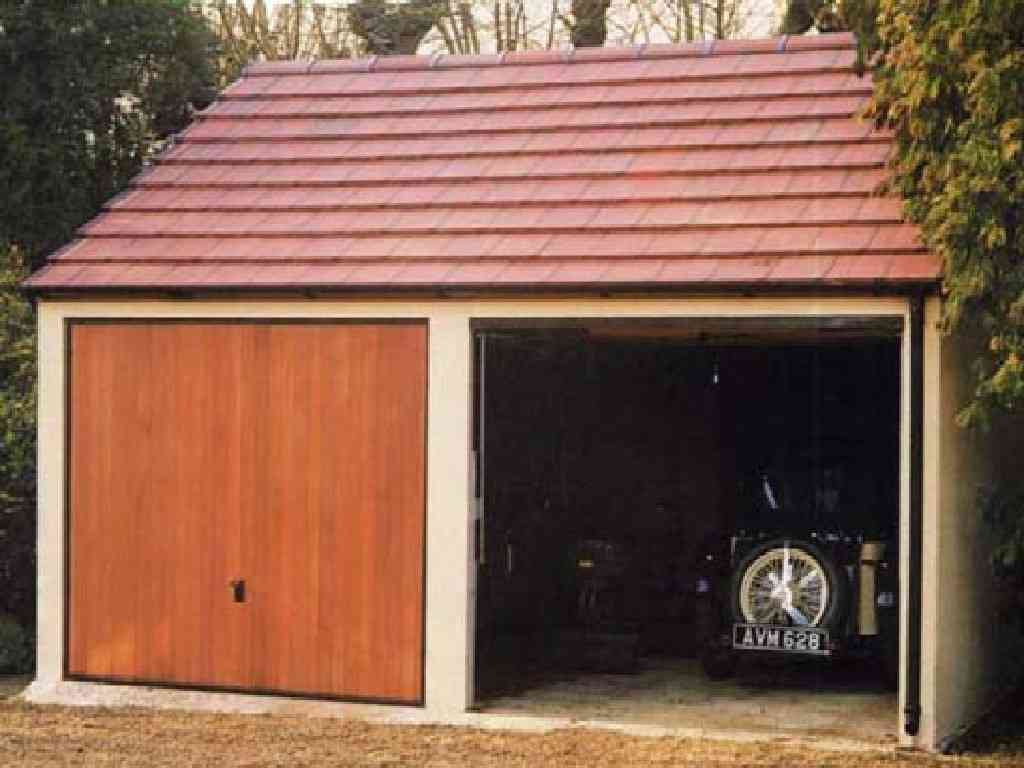
System M-Q
Another early Marley design. Can be converted to System X fronts and Roller Shutter Doors. For more information see Page 31.
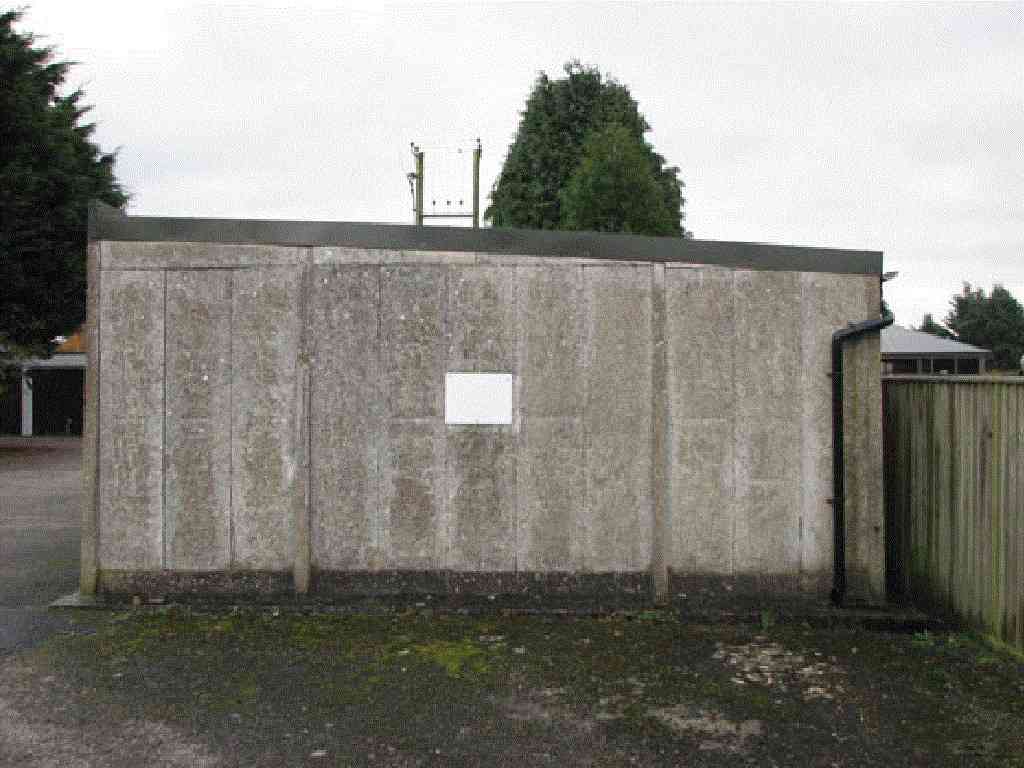
System M-E8/9 F/R
Marley Economy Range. Available with 8′ or 9′ interior widths. All parts available. Can be converted to System X fronts and Roller Shutter Doors. For more information see Page 30.
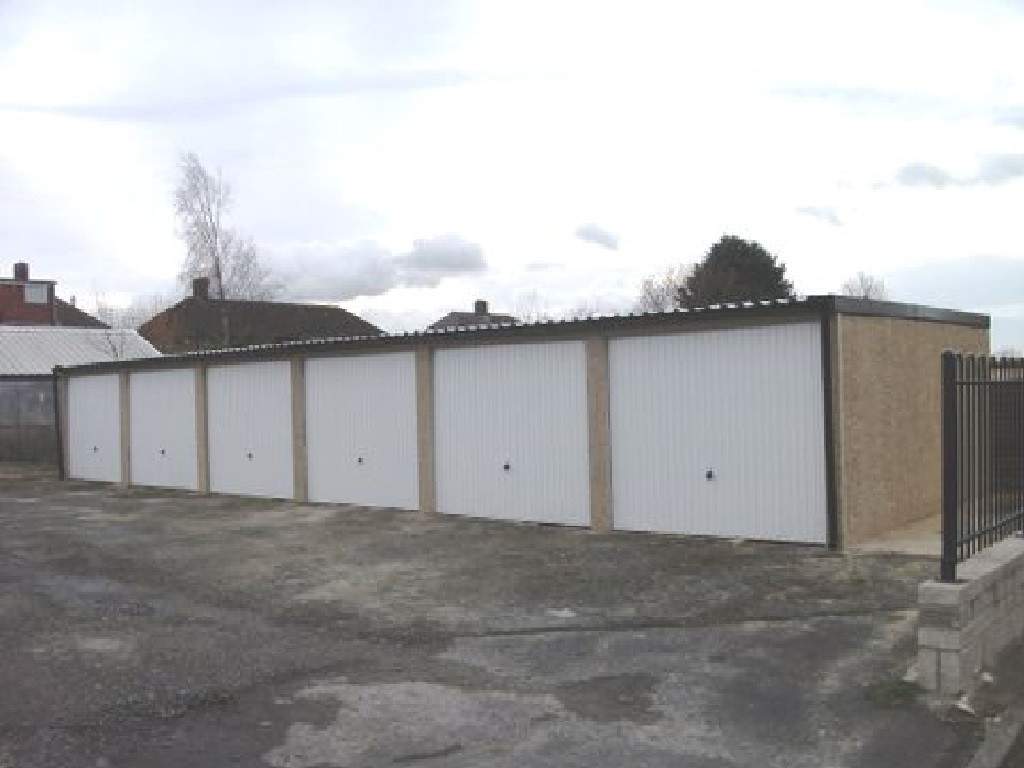
System M8/9F
Current Marley design. All parts available and can be converted to System X fronts and Roller Shutter Doors. For more information see Page 32.
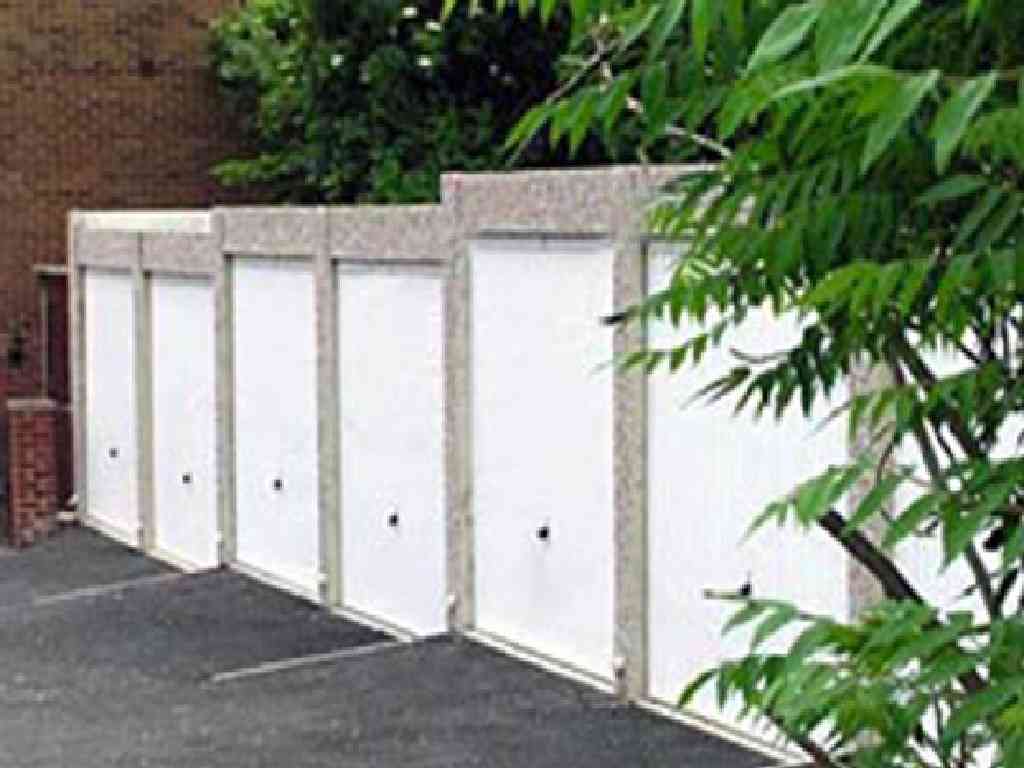
System M8/9R
Current Marley design. All parts available and can be converted to System X fronts and Roller Shutter Doors.
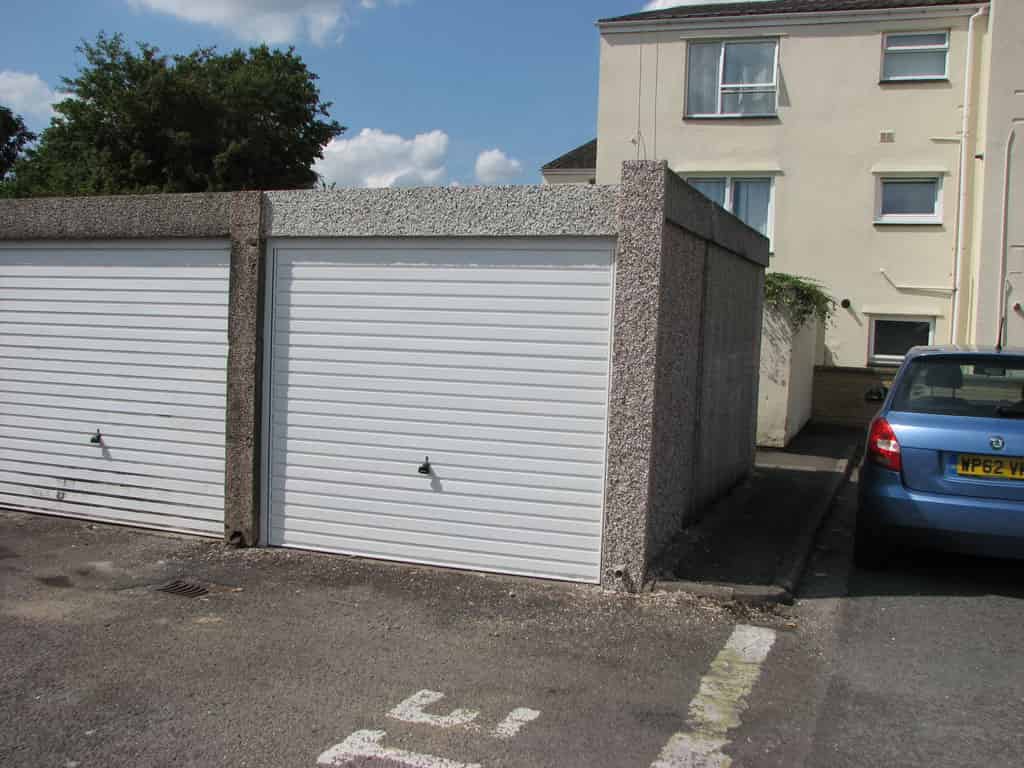
Page 24
System FMTF
Unknown manufacturer. Probably best demolished. For more information see Page 32.
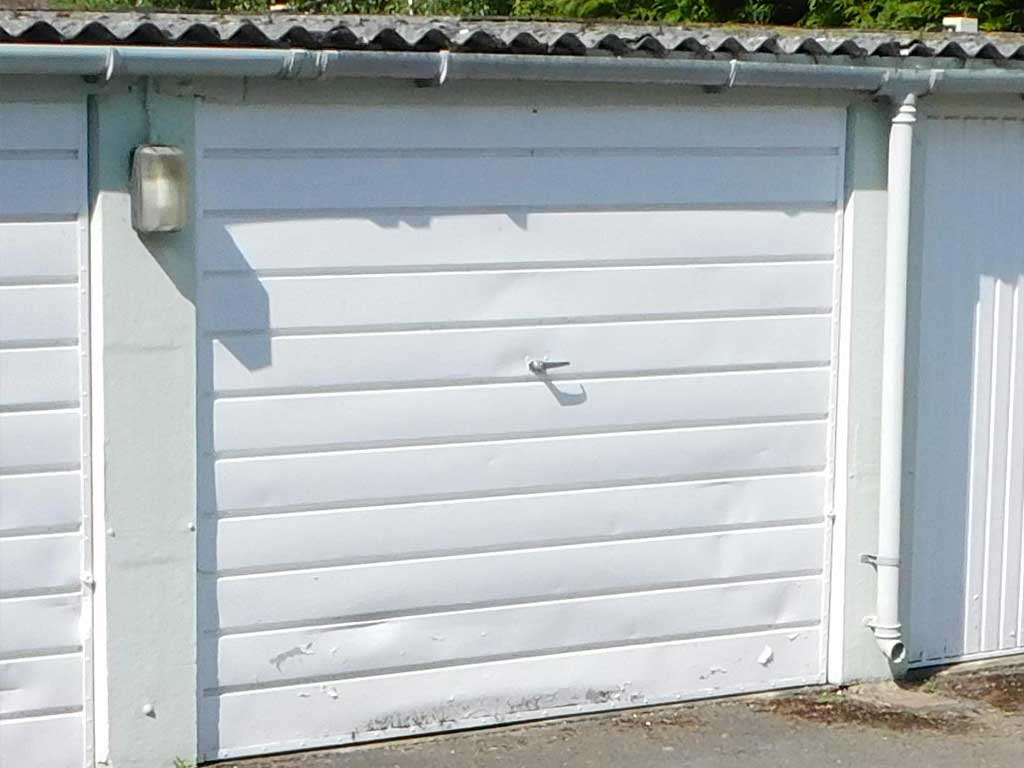
System TAR
Manufacturer long gone. If significant quantities of parts are required then moulds can be made. For more information see Page 35.
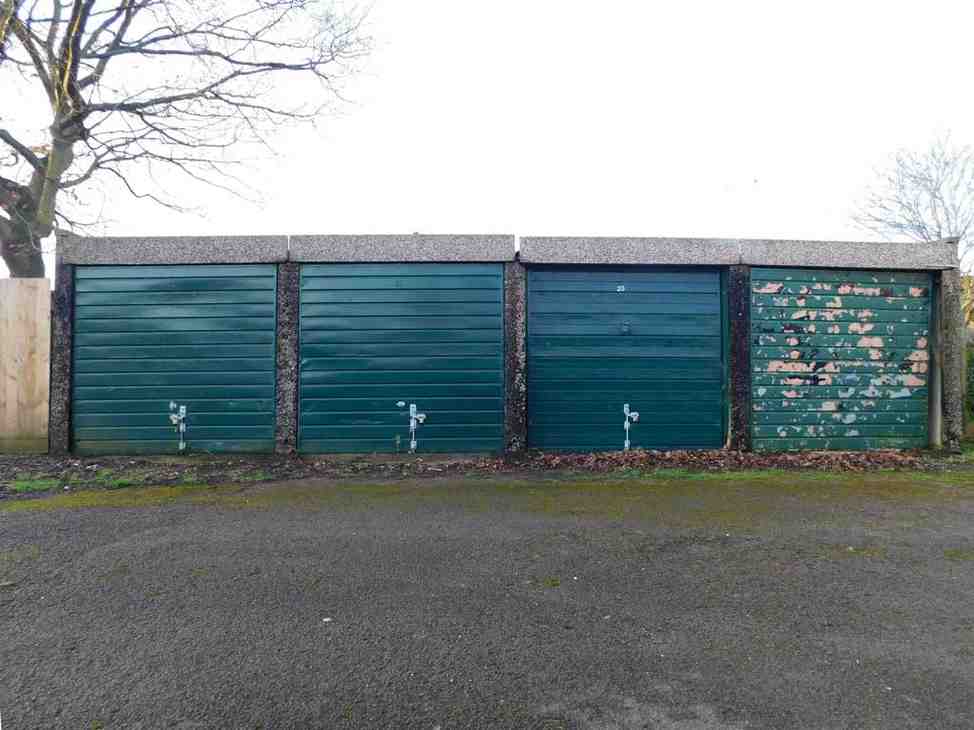
System TPP
Probably Cotswold. Long gone, no parts available. Walls are large Four foot square panels. No parts available. For more information see Page 36.
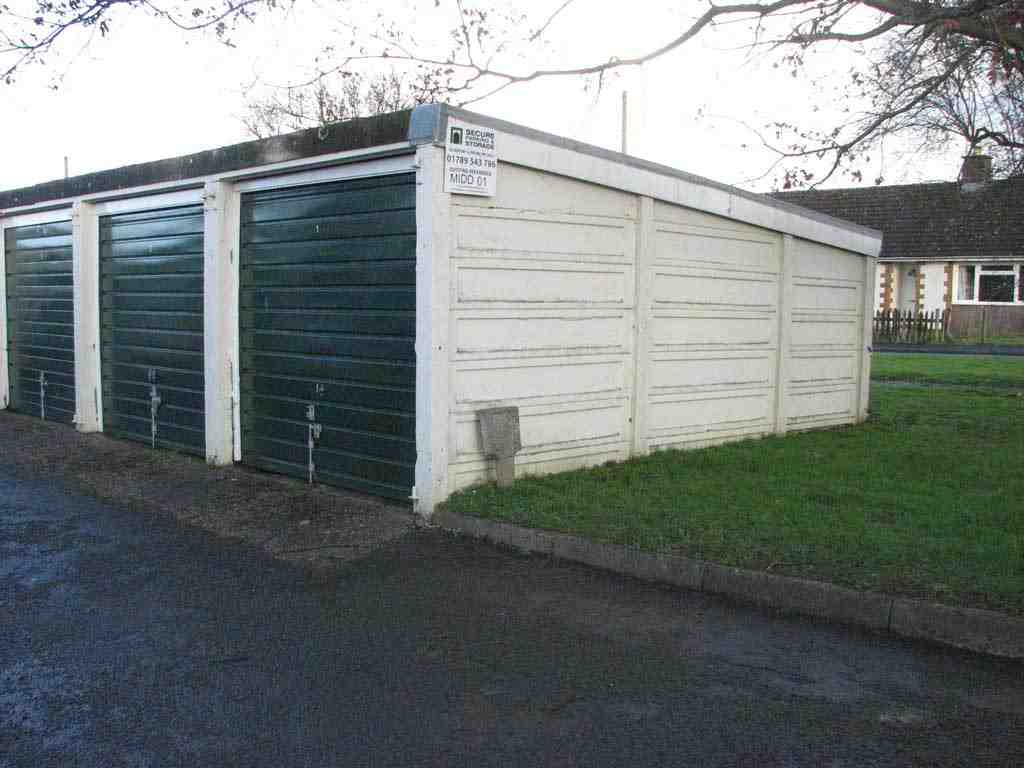
Page 25
System V
Probably Cotswold. Long gone, no parts available. Walls are large Four foot square panels. No parts available. For more information see Page 36.
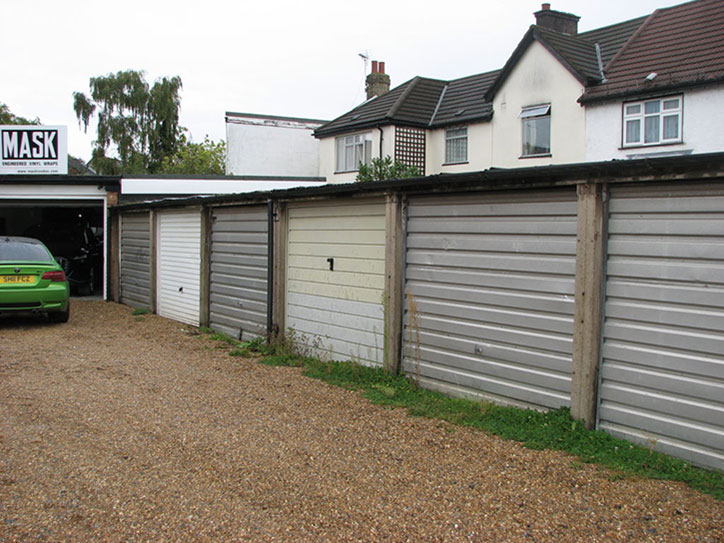
System WMR
Obsolete design. No parts available. For more information see Page 37.
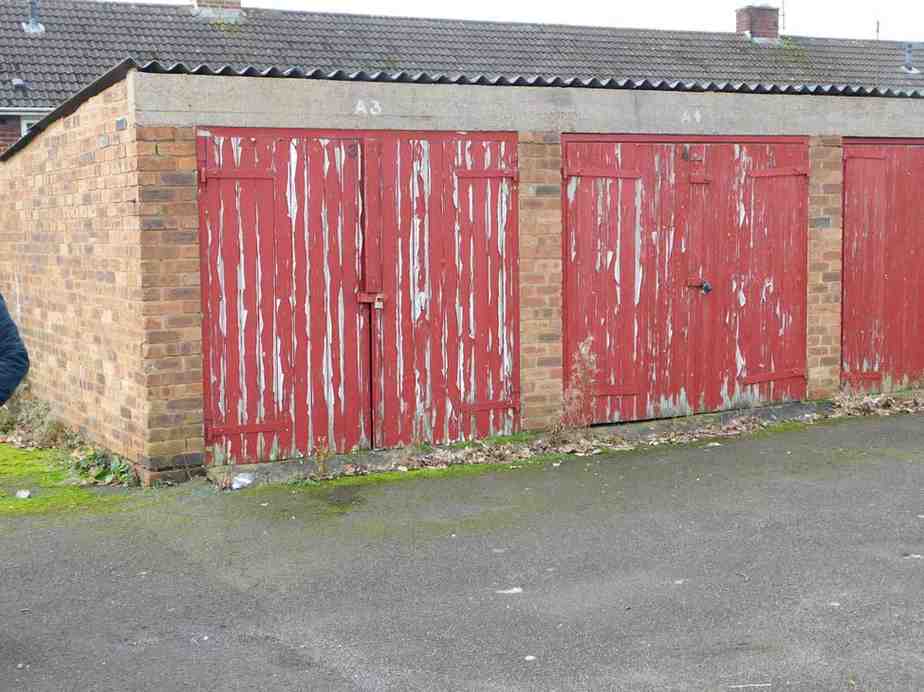
System WPF
Obsolete design. No parts available. For more information see Page 37.
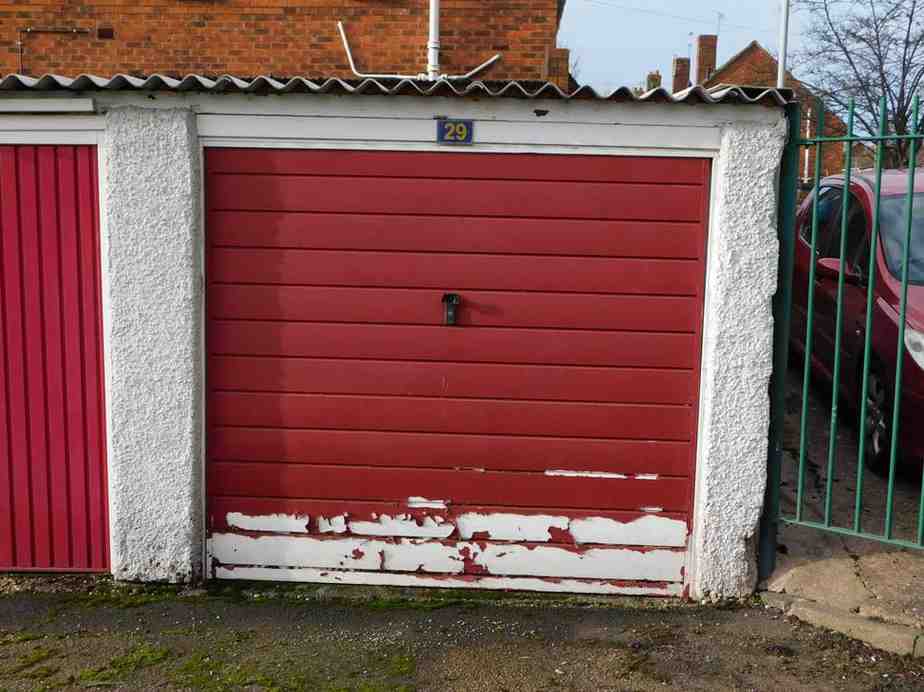
System WNR
Obsolete design. No parts available. For more information see Page 38.
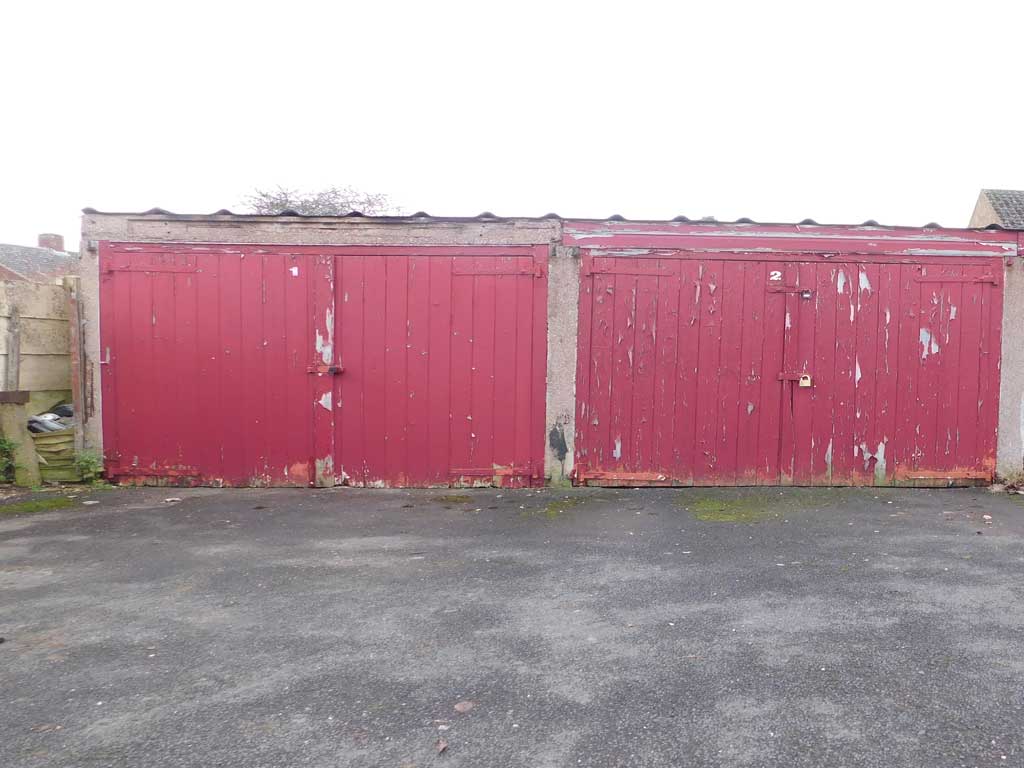
System YPP
Obsolete design. No parts available. For more information see Page 38.
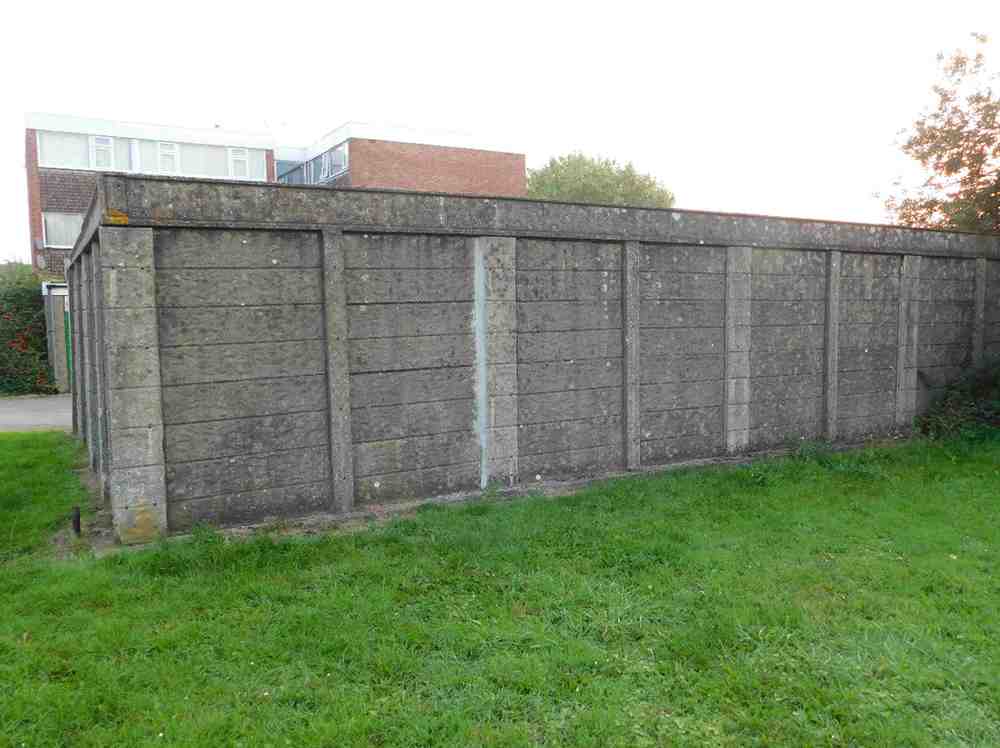
Page 26
System B Battery Garage Detail
System B battery garage form the garage stock of many local authorities and as the original mnufacturer went out of business 30-40 years ago we have manufactured moulds for all 12 concrete components.
Common problems are lintels failing, posts disintergrating, and door mechanism mounting panels cracking.
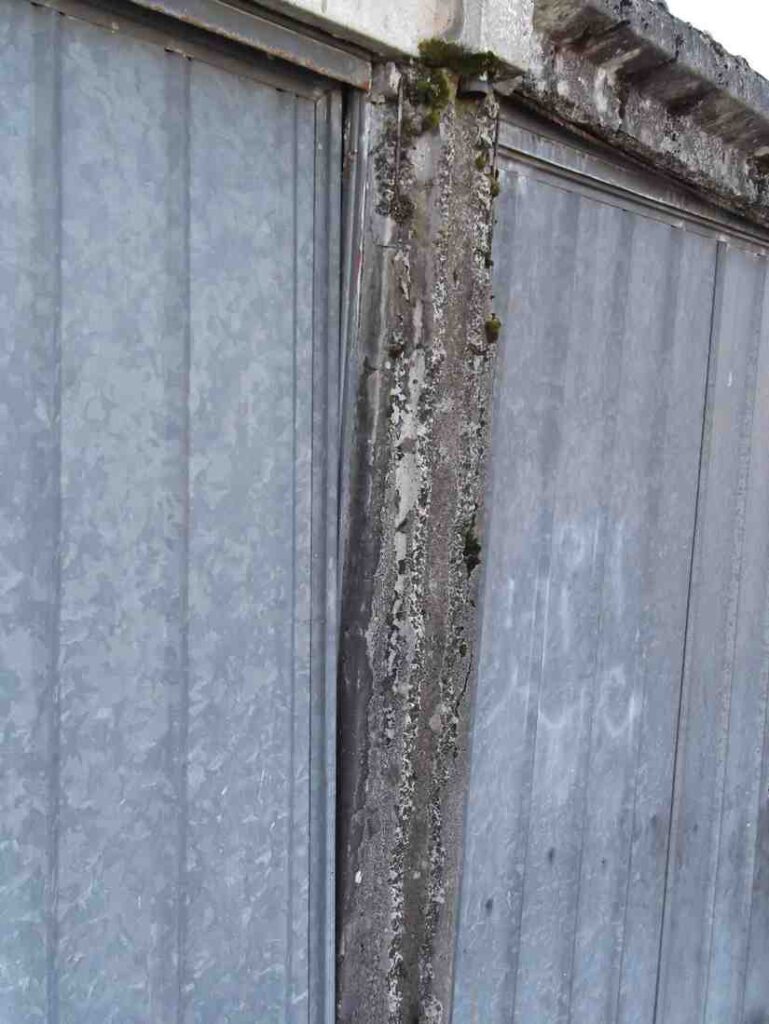
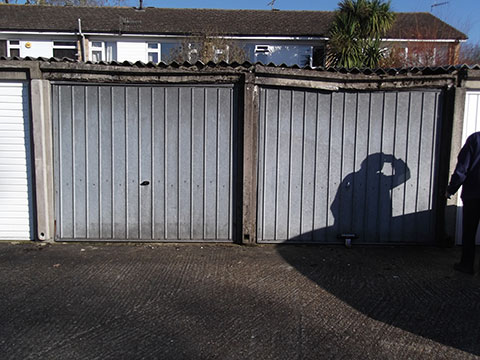
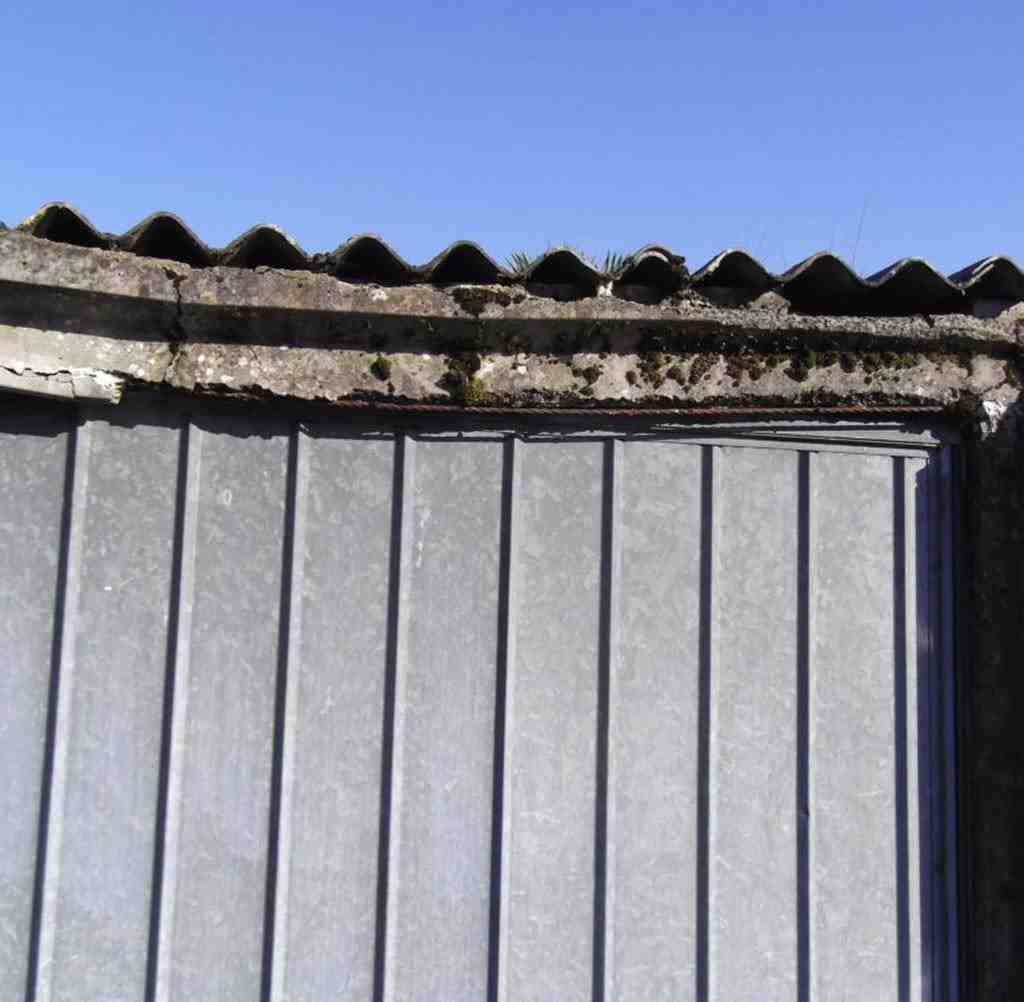
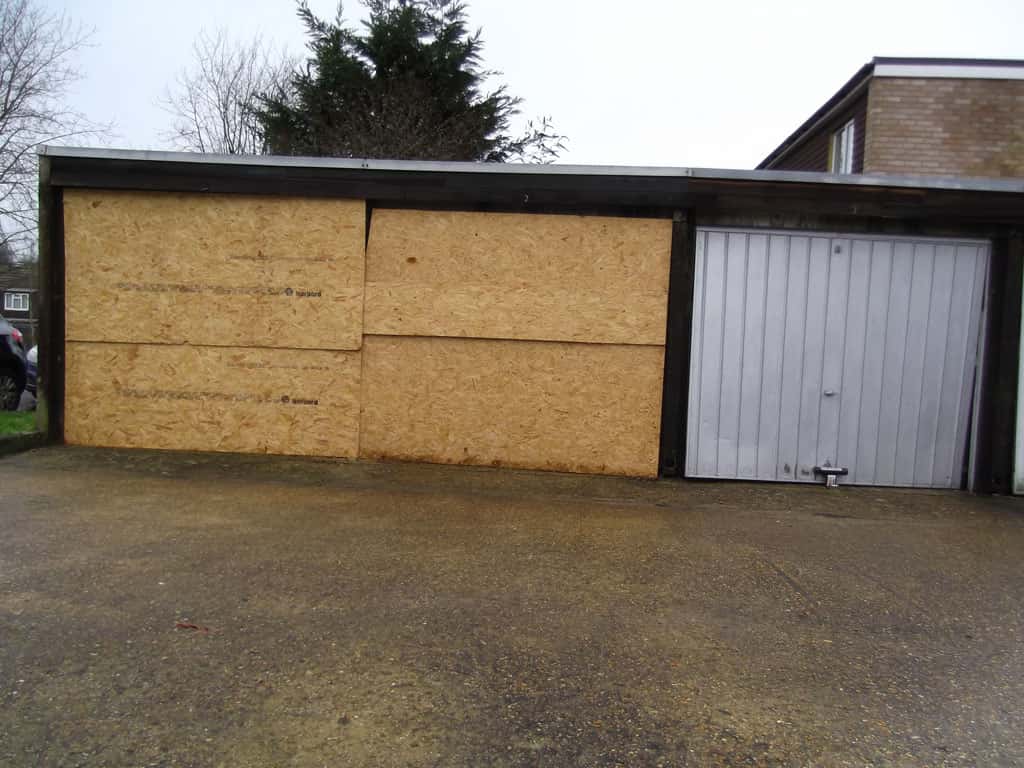
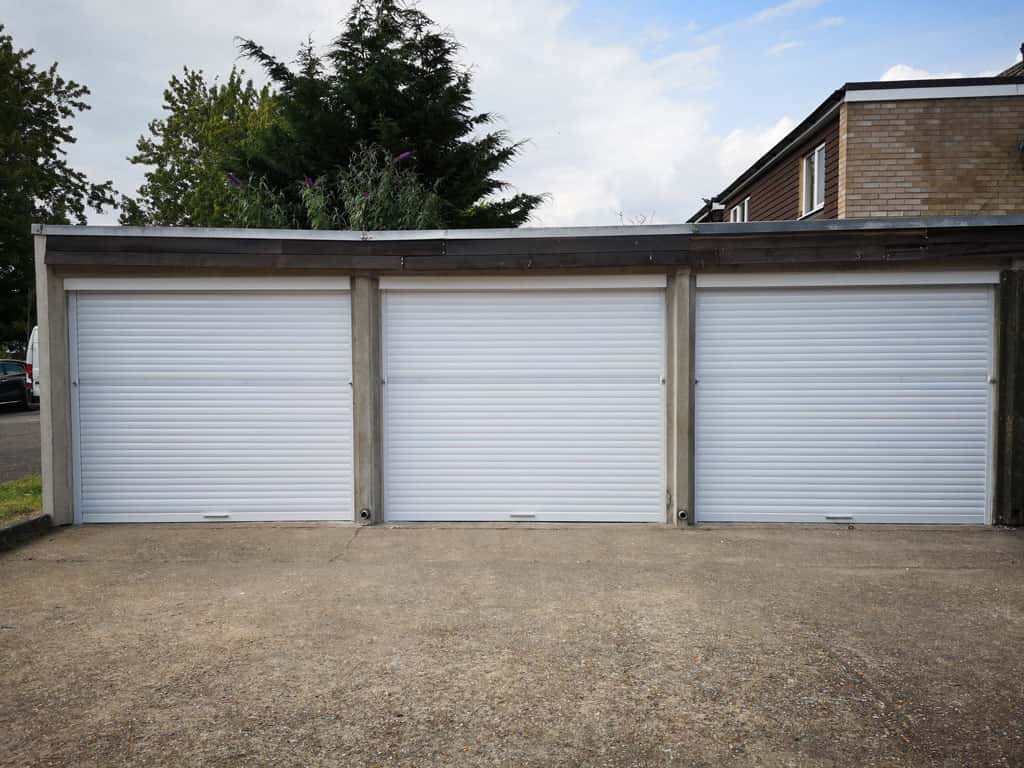
In the event of a door collision our roller shutter doors are far easier and cheaper to repair with damaged slats costing only a few pounds each in replacement costs, versus about £900.- or more for a new up and over door with fitting.
Page 27
System L Battery Garage Detail
System L battery garage (for Leofric) started life as a Banbury Garage. When Banbury split into
Compton and Leofric, Compton dropped Battery Garages but Leofric continued with the product. That is why we can still supply parts, fifty or so years later. The main difference between System L and System E is that the System L is built from the rear corners forward whereas System E relies on posts sunk into the concrete base and then built backwards.
System L battery garage is simple. However the original lintel and front gutter design used a metal section, largely hand made. Today we would replace the fronts with System X components.
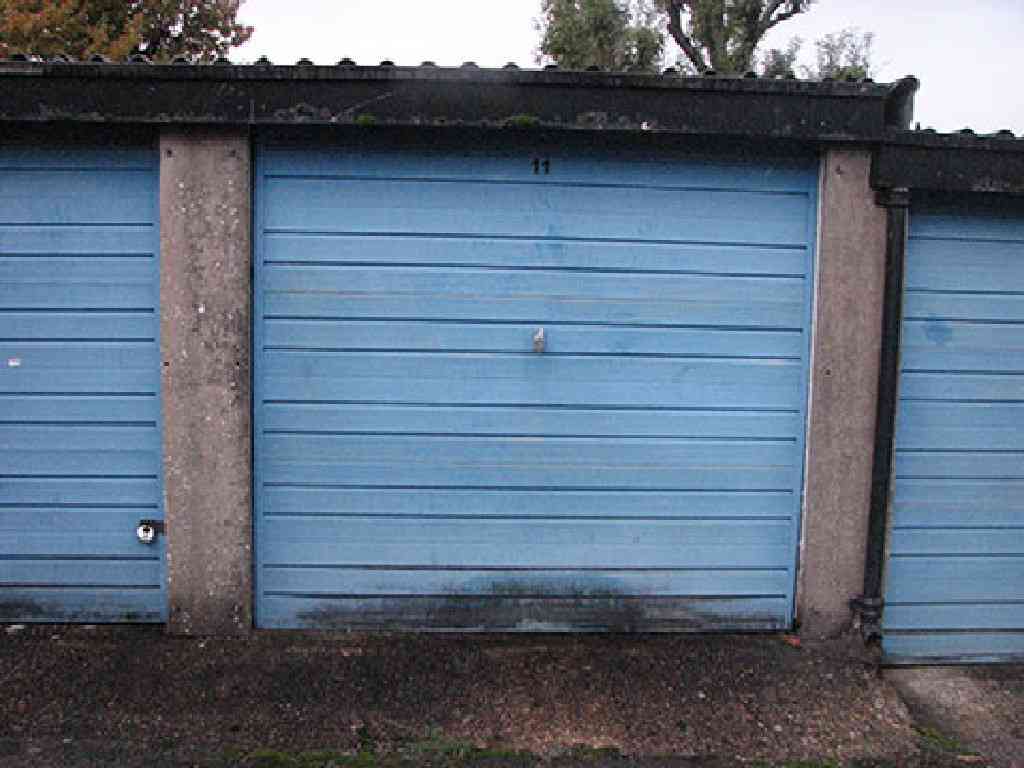
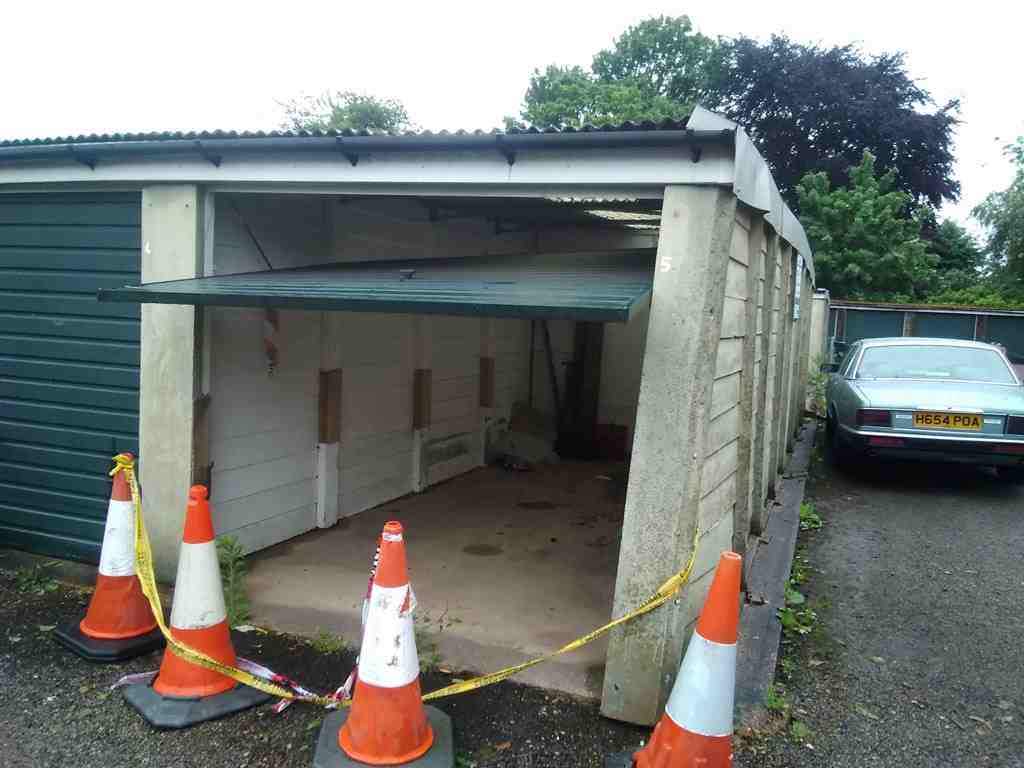
Before
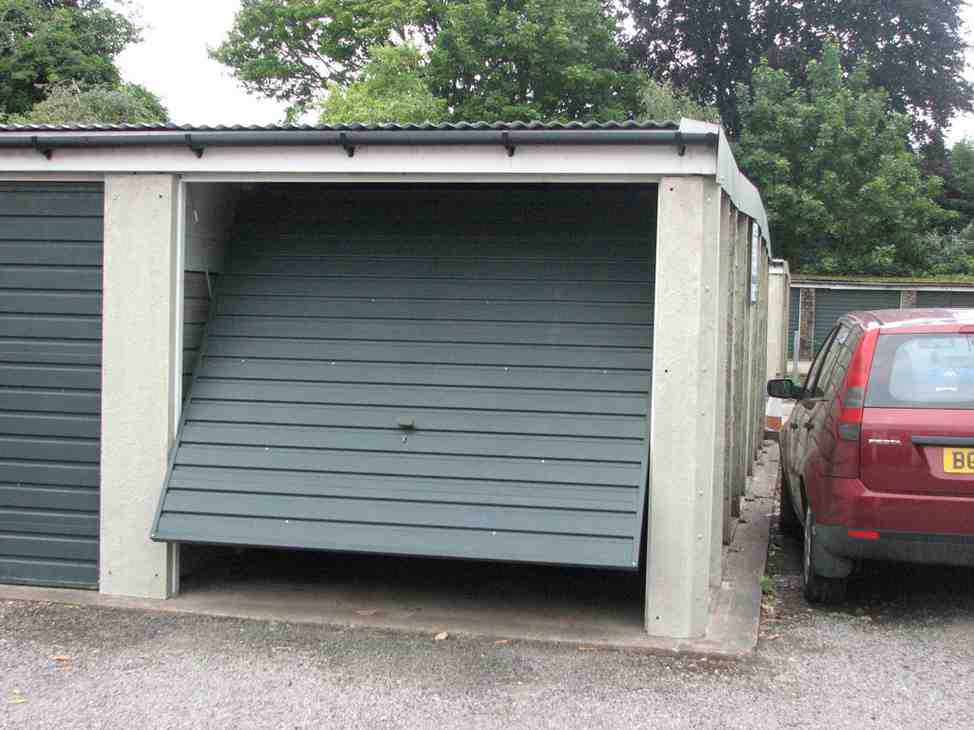
After
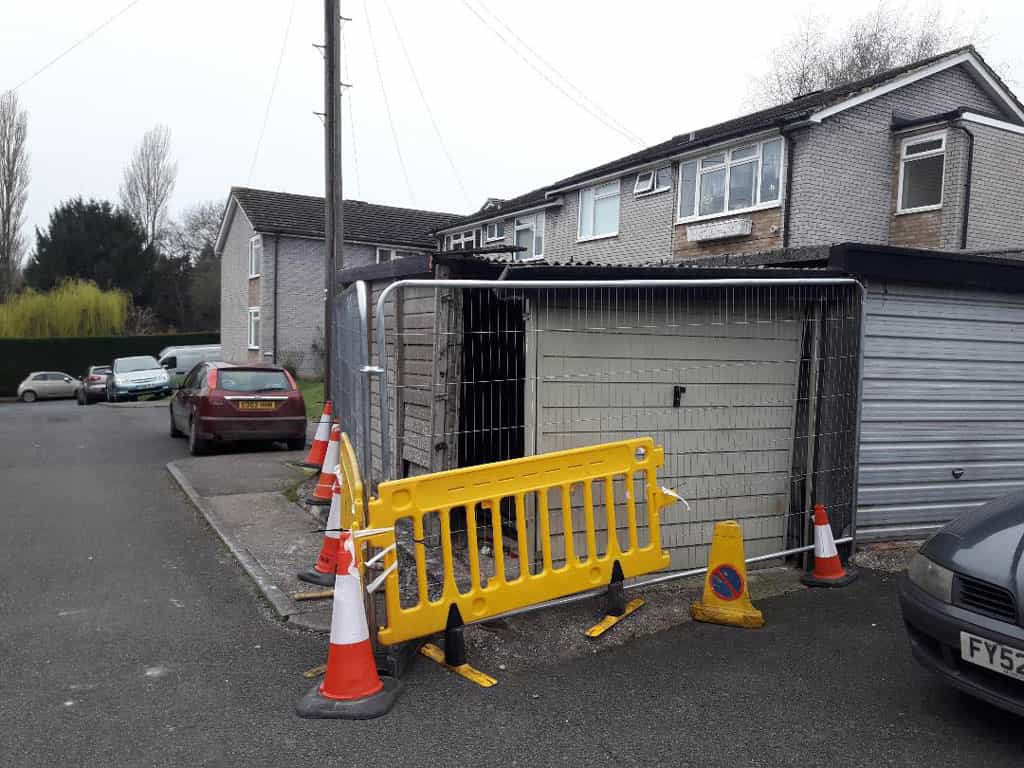
Before
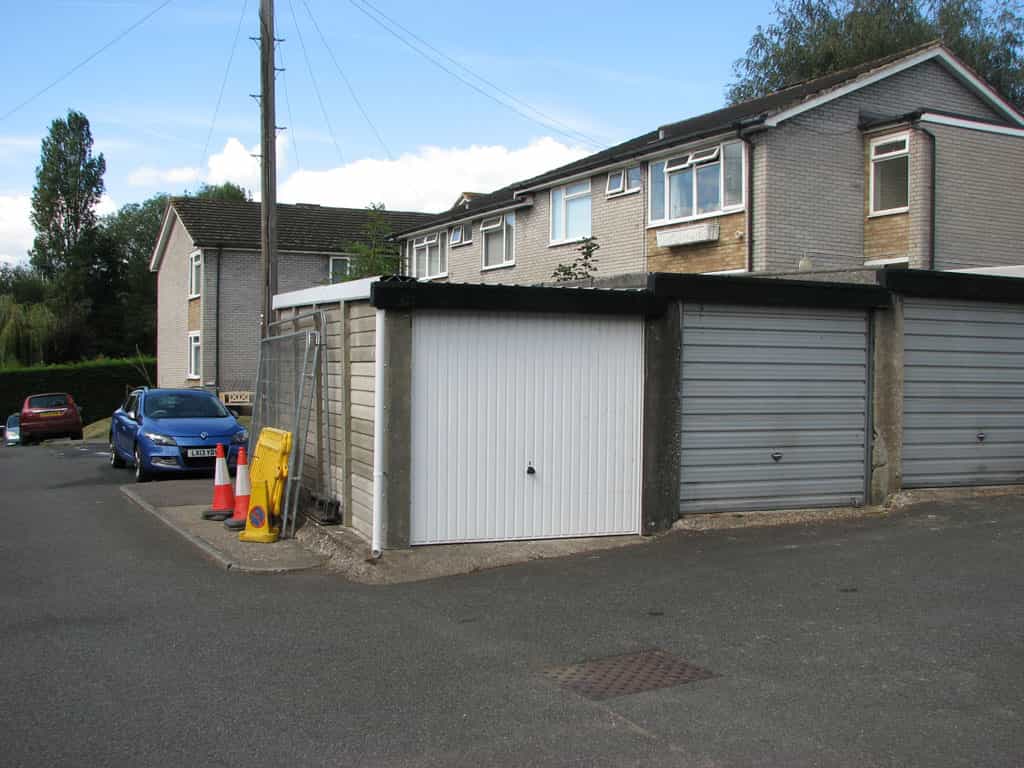
After
Page 28
System M-8G Battery Garage Detail
The System M-8G battery garage was an early Marley product and can be identified by a number of characteristics but the two instantly recognisable ones are the construction using 16″ panels combined with the unstoned, rounded-off edges of the panels.
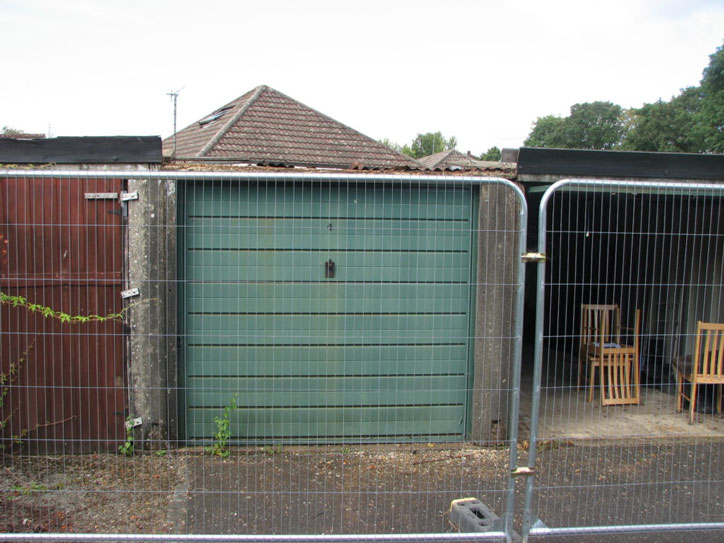
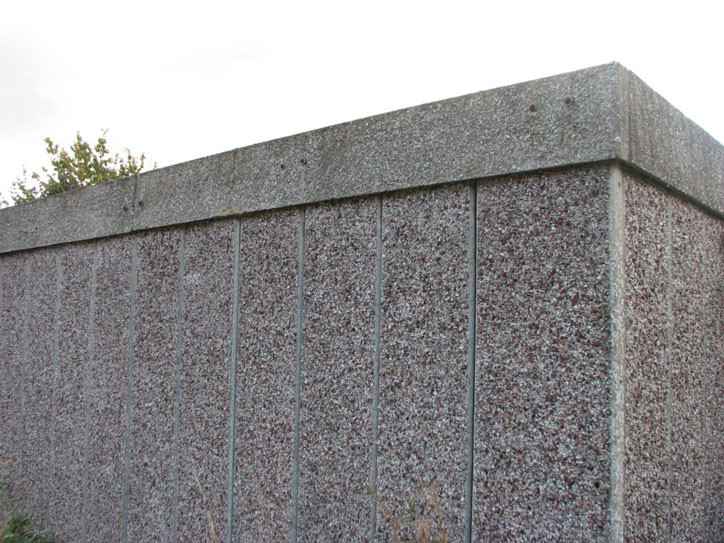
Recently the lady using this System M-8G garage shut the door (perhaps too vigorously) whereupon the lintel on her garage, similar to the one on the right, crashed to the ground just missing her. Obviously this is dangerous to the person shutting the door or to children using the garage front for soccer practice or similar activity.
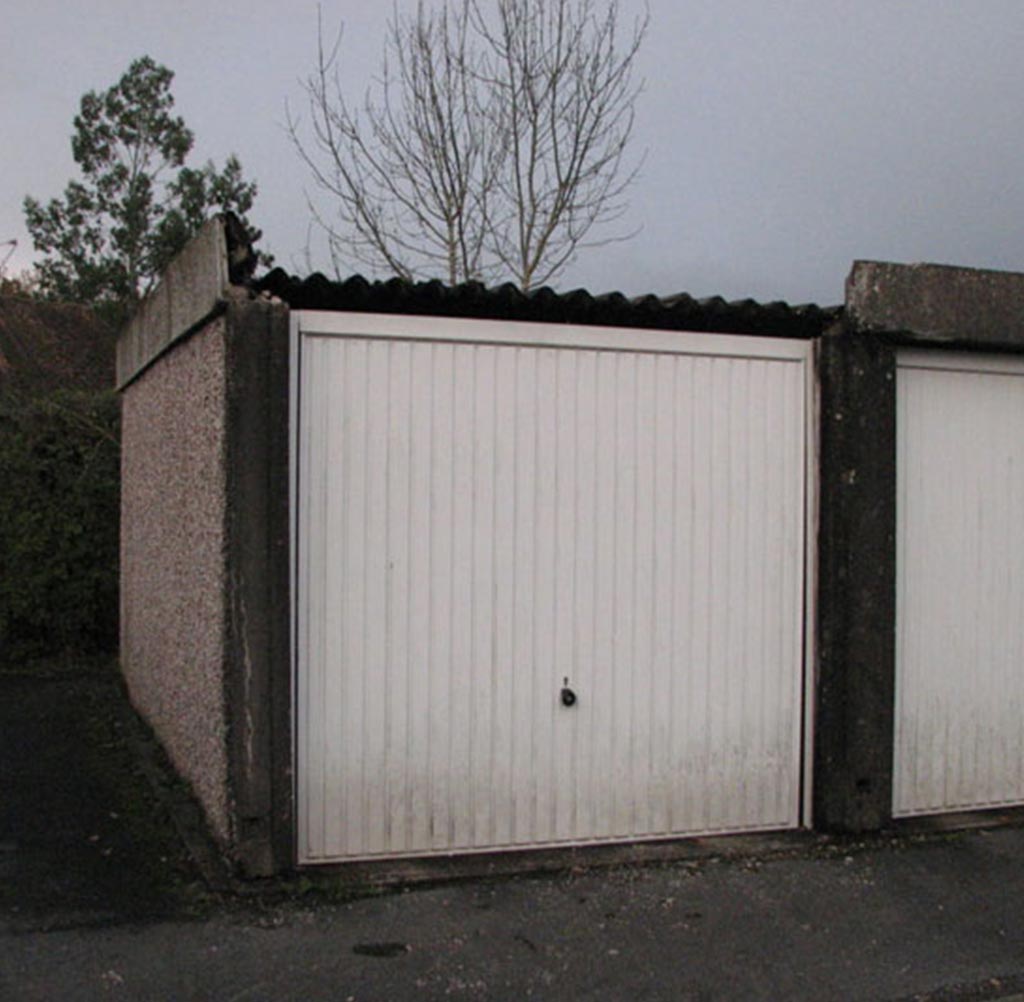
Page 29
System M-E8/9 F/R Battery Garage Detail
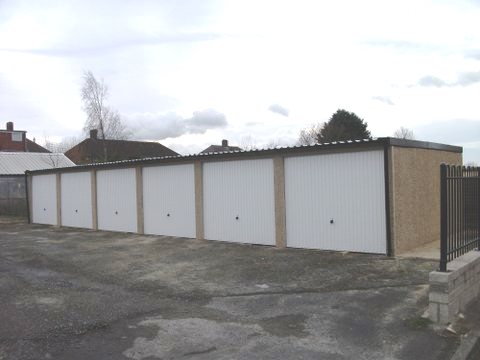
These System ME8/9 battery garages are current Marley-designed Leofric built Models and seldom need refurbishment for deterioration but often require repair following vehicle collisions and falling trees or base disruption due to adjacent tree growth. All parts are available, however System LX components will fit to these units to extend building life and enhance apprearance.
System M-H Battery Garage Detail
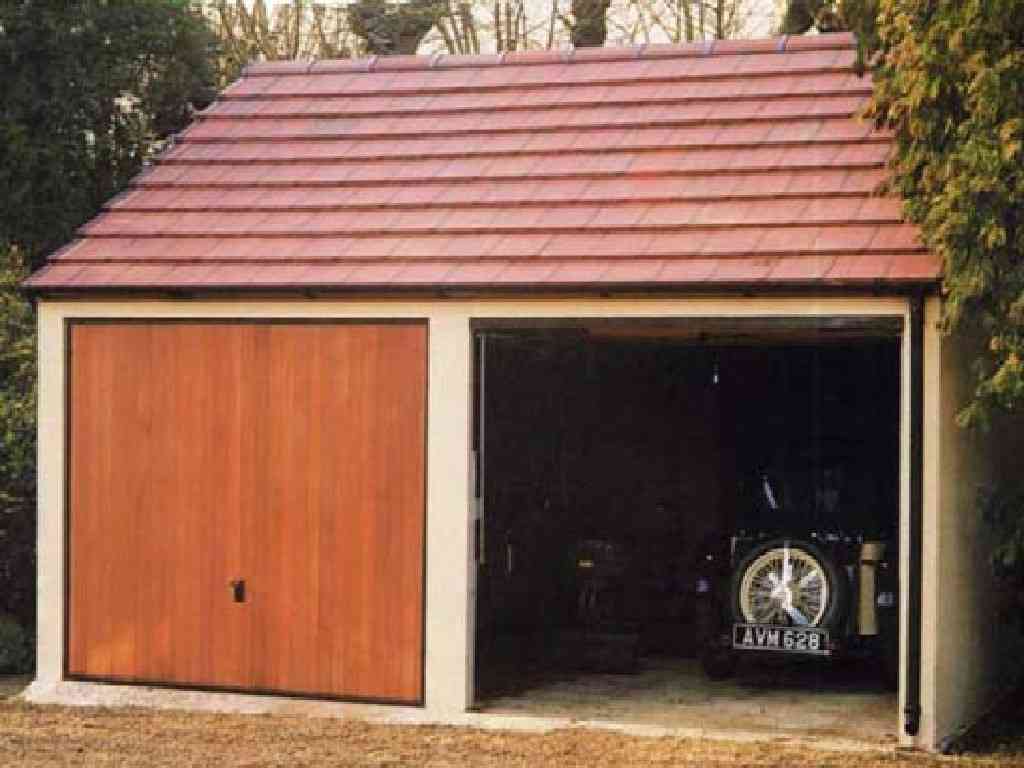
Page 30
System M-Q Battery Garage Detail
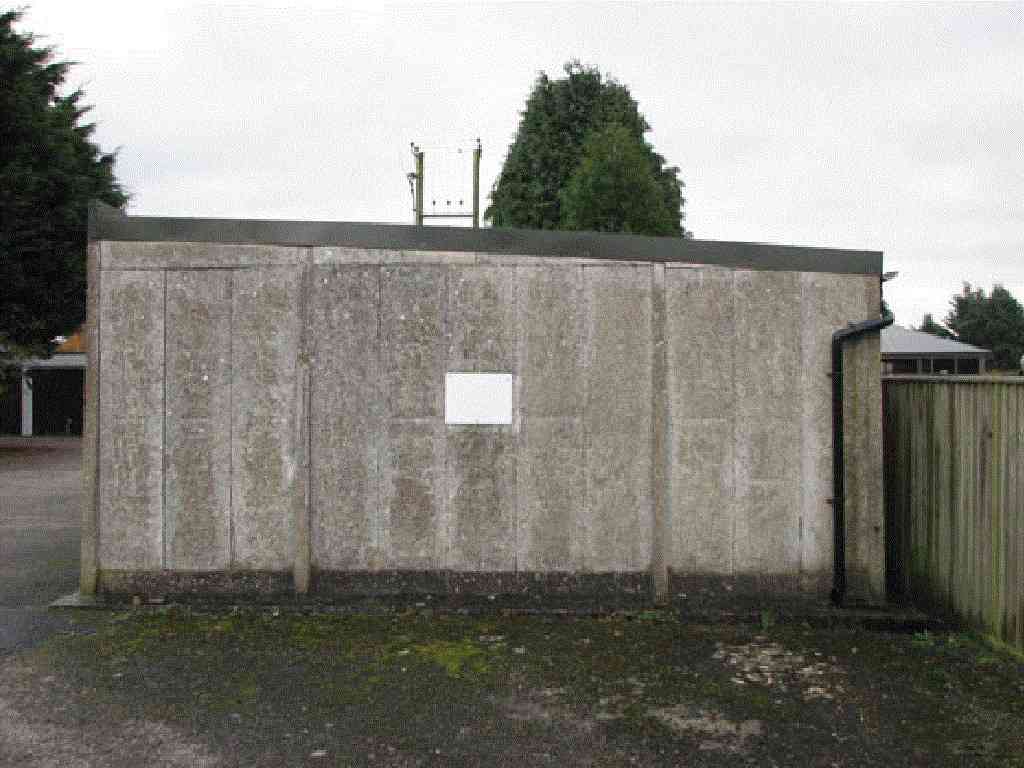
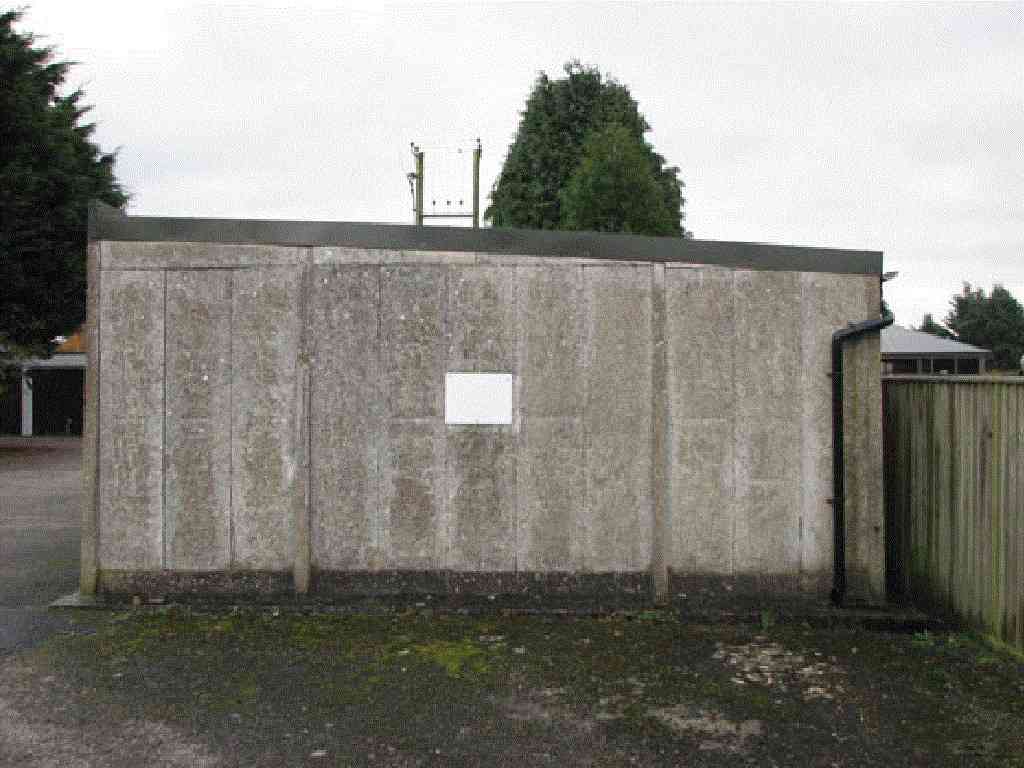
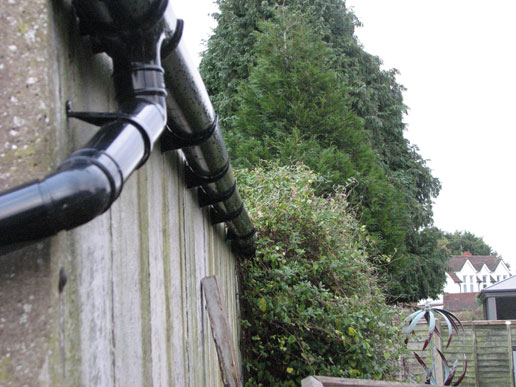
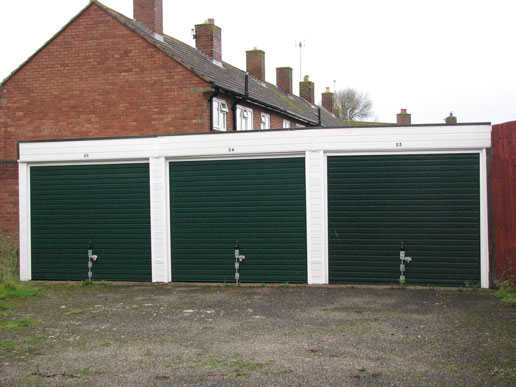
Page 31
System M8F/R Battery Garage Detail
These system M8F/R battery garages are still in our current range. Most are in good condition but they do suffer from collision damage from time to time. All parts are available.
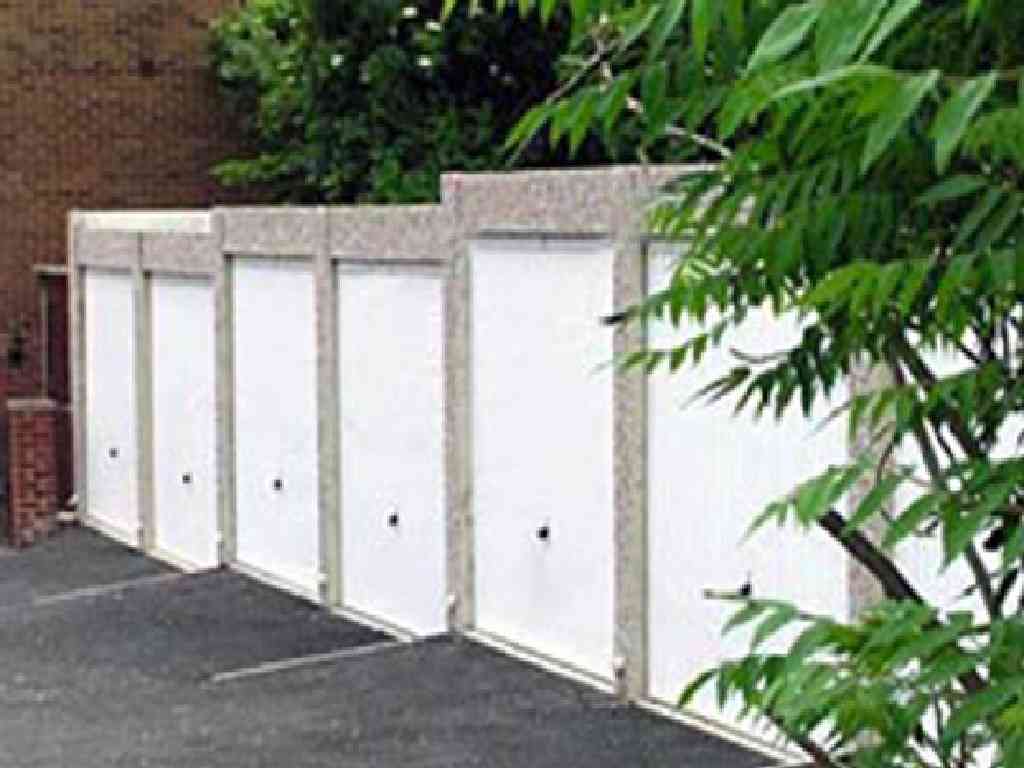
This is how the M-8F looked after a repair. The Type indicates the slope of the roof, F slopes and drains to the front. The R slopes backwards and drains to the rear. The 8 or 9 indicates the internal width of the garage. All System M8F/R Garages can be converted into System X format.
System FMTF Battery Garage Detail
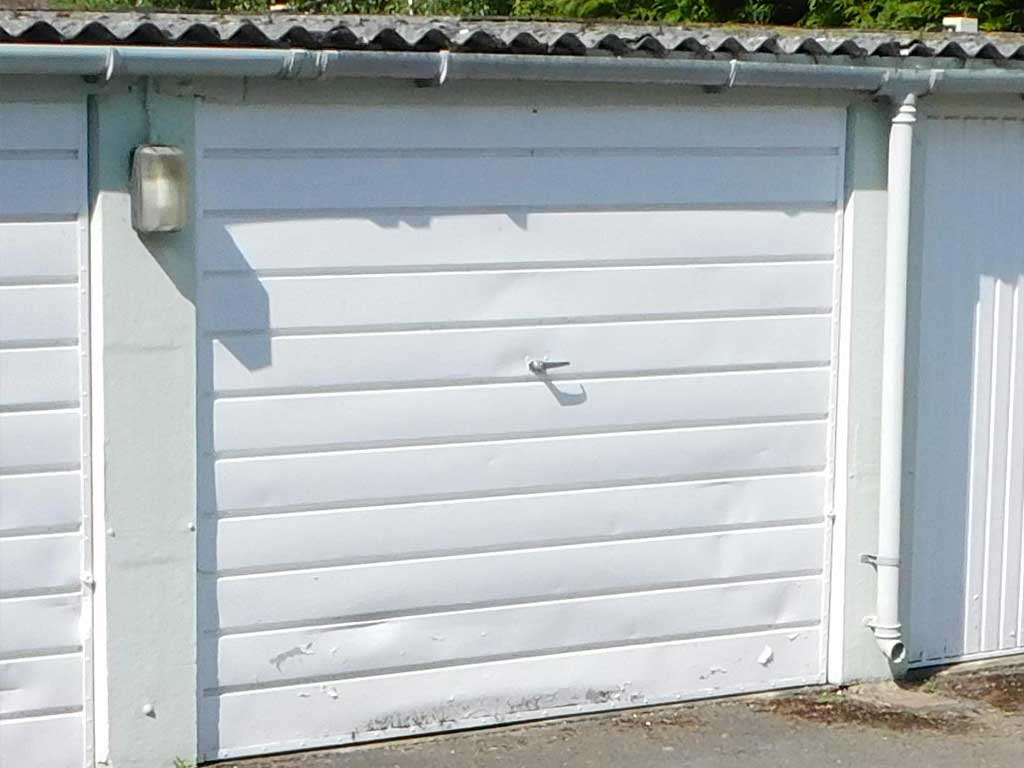
Page 32
System FMTR Battery Garage Detail
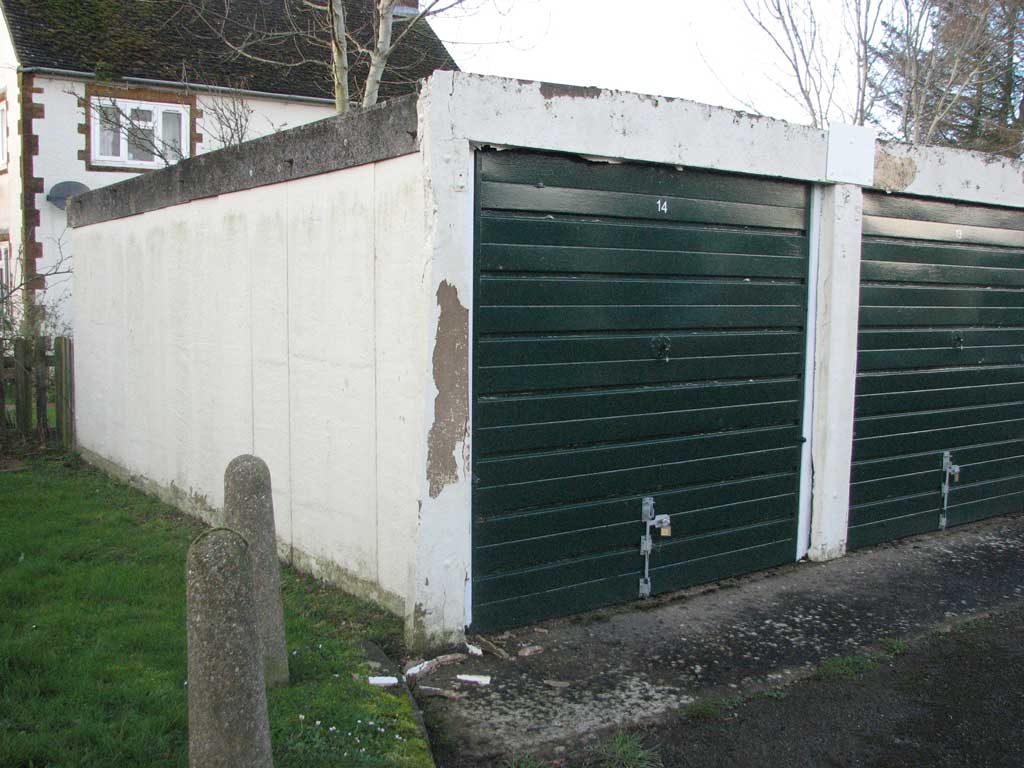



Page 33
System P Battery Garage Detail
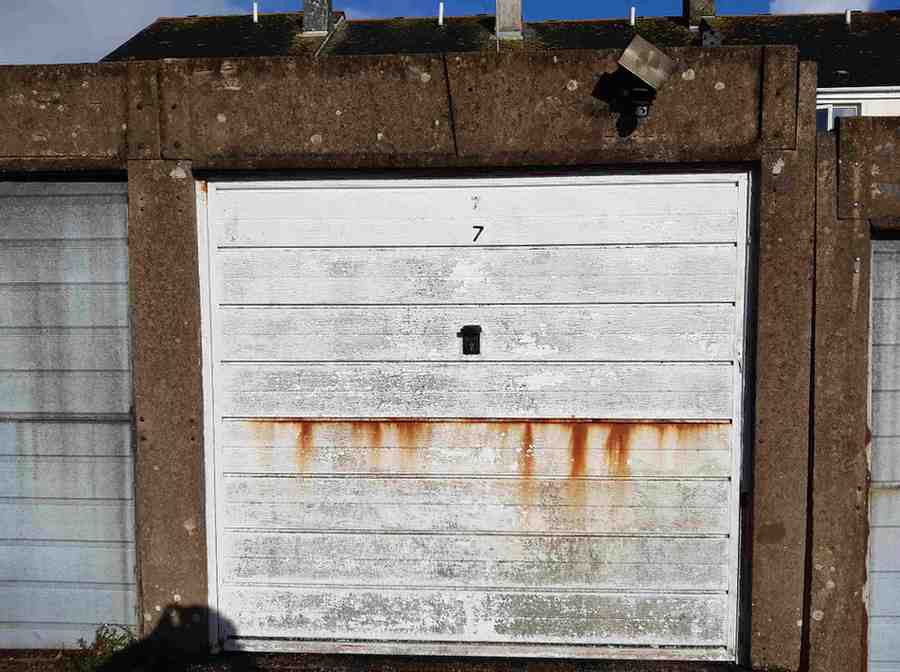
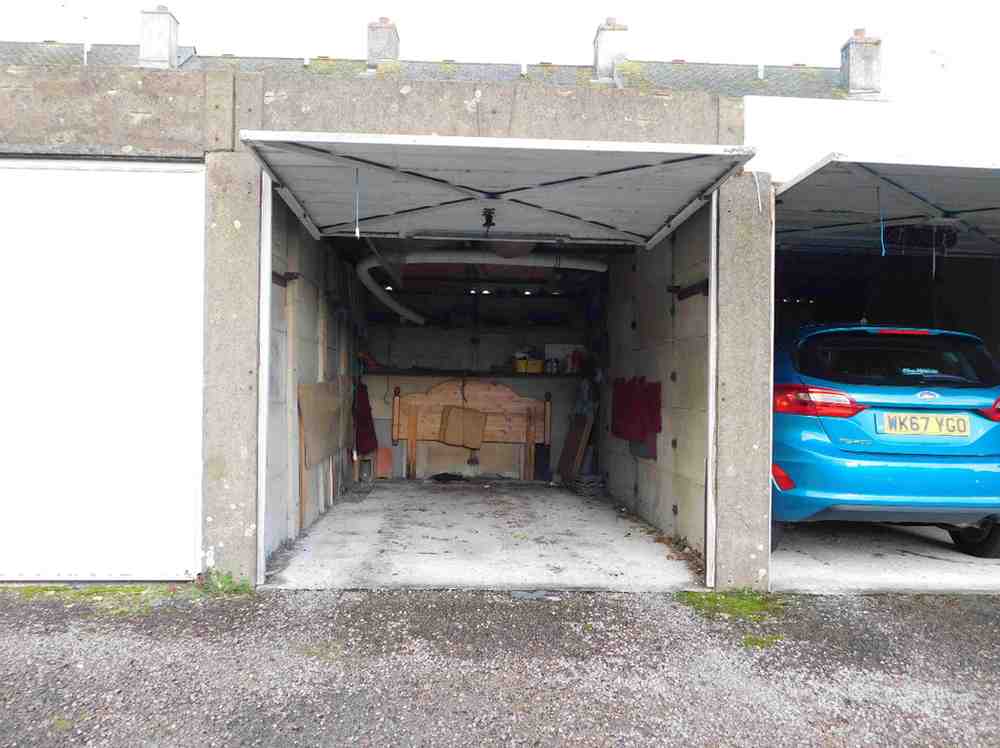
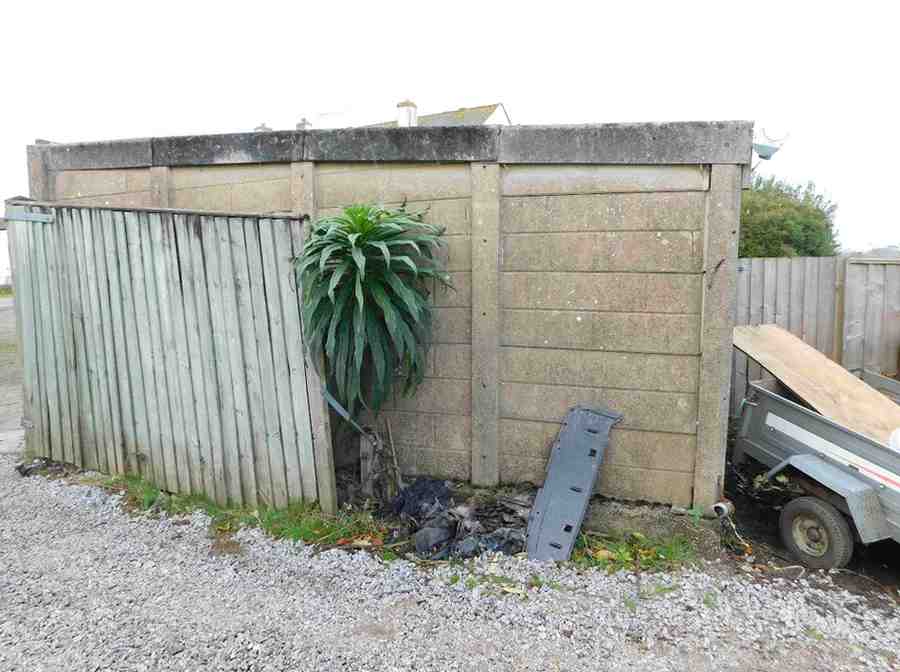
Page 34
System TAR Battery Garage Detail
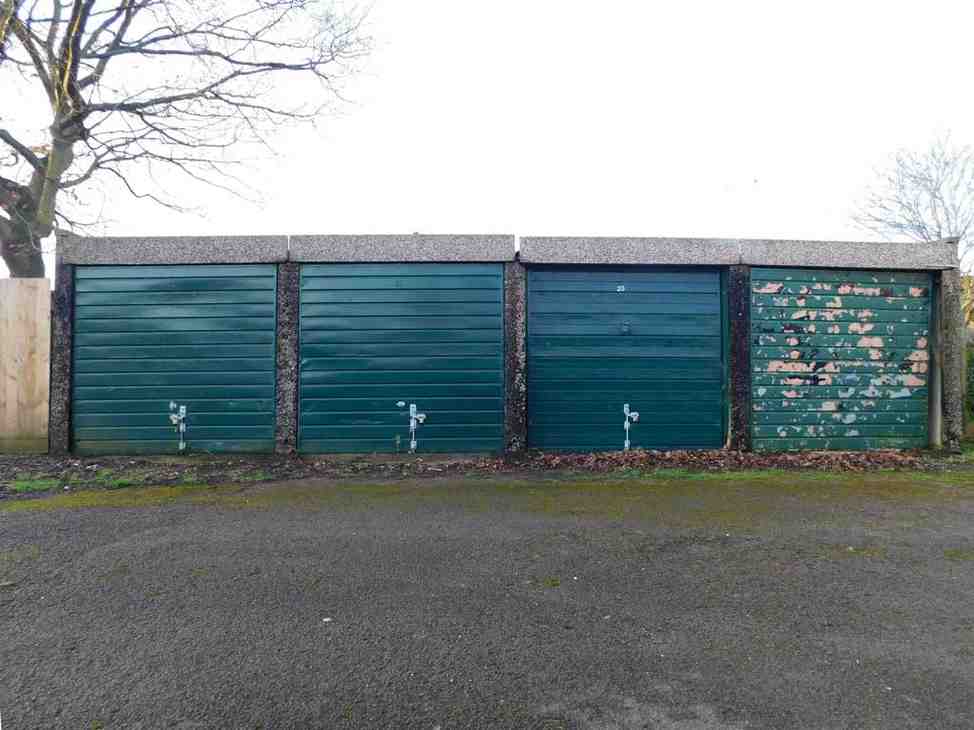
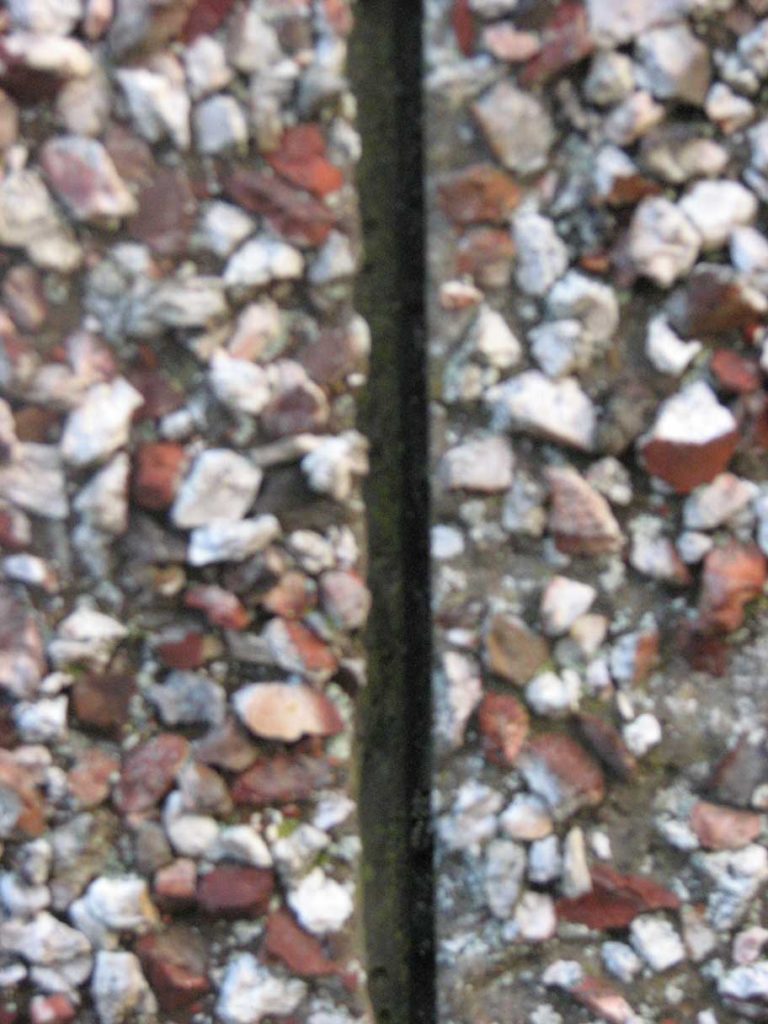
Note also the gap between panels which shows evidence of a tongue and grooved joint although not as pronounced as a Marley joint. Can be upgraded to System X.
Page 35
System TPP Battery Garage Detail
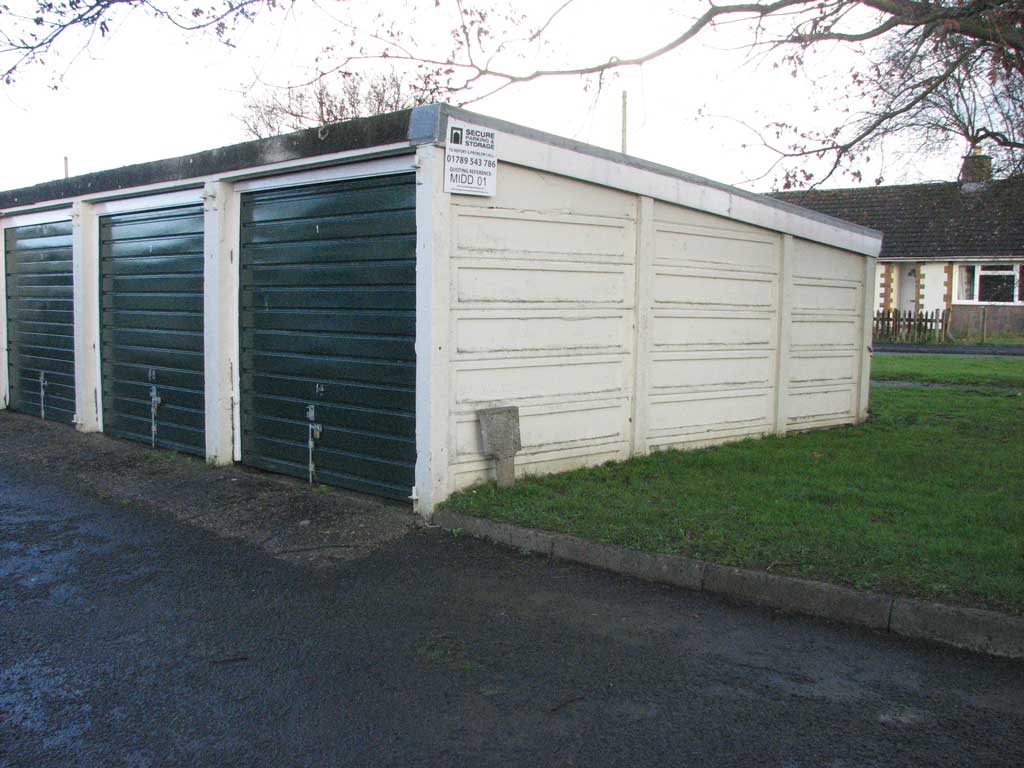
System V Battery Garage Detail
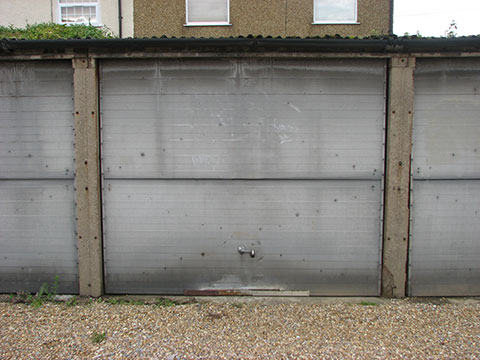
Page 36
System WMR Battery Garage Detail
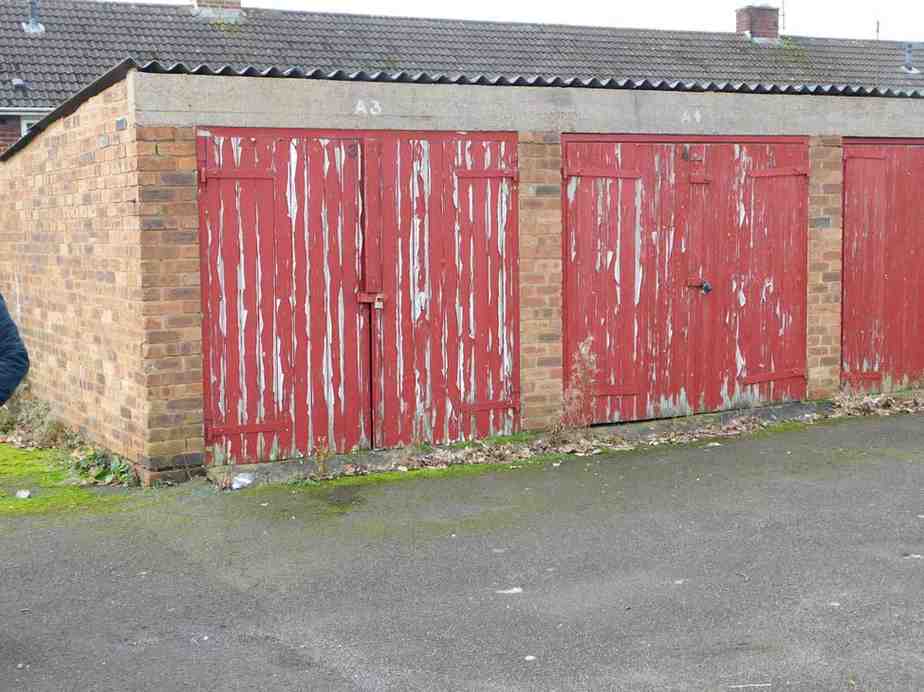
System WPF Battery Garage Detail
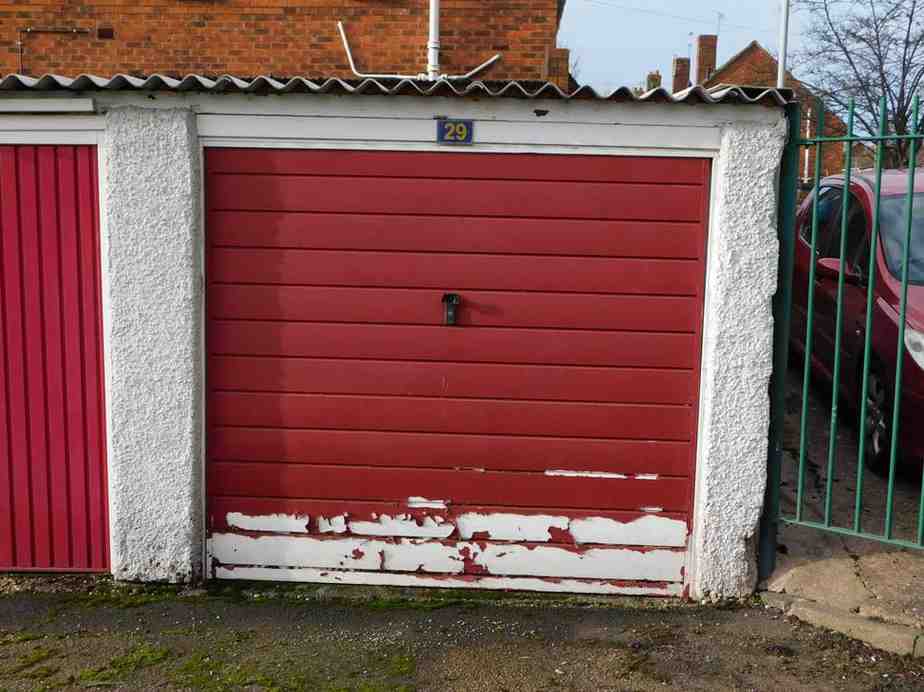
Page 37
System WNR Battery Garage Detail
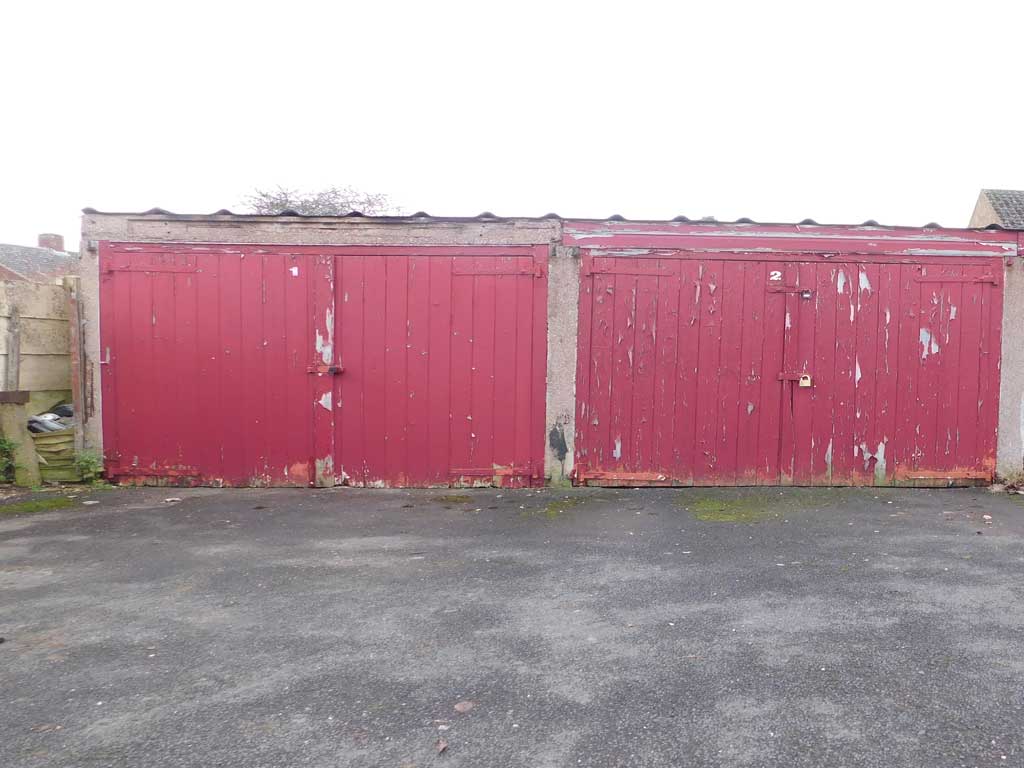
System YPP Battery Garage Detail
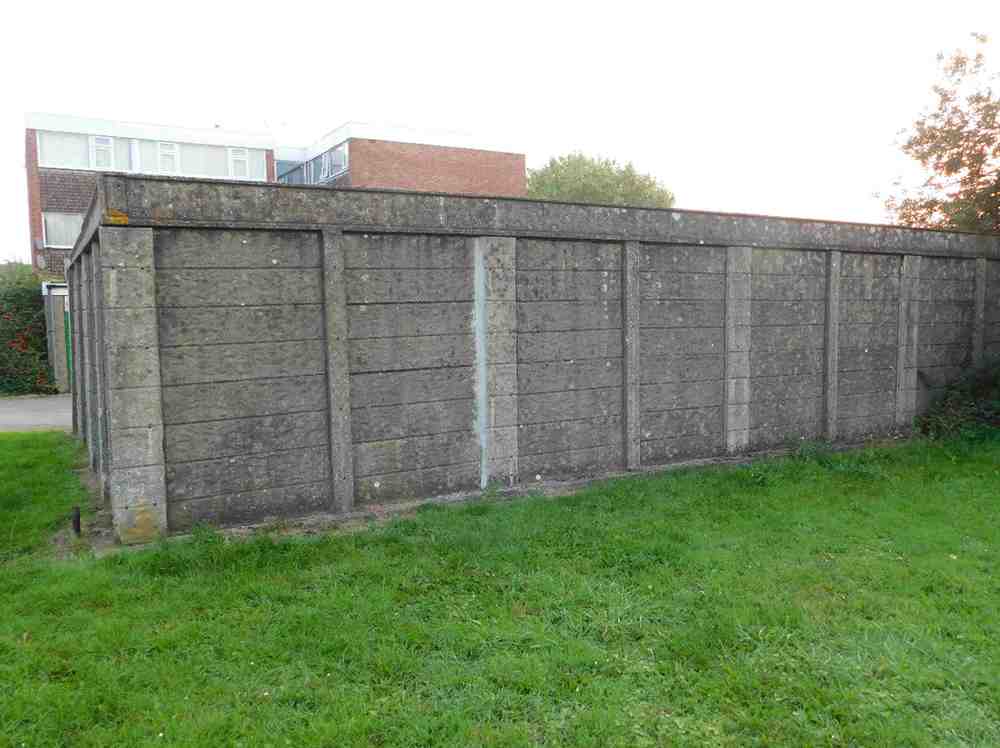
Page 38
Page 39